Hardening heat treatment is a critical process in metallurgy aimed at increasing the hardness and strength of metals, particularly steel. The process involves heating the metal to a specific temperature, typically above its upper critical temperature (often over 900°C for steel), holding it at that temperature for a set duration, and then rapidly cooling it through quenching. This rapid cooling transforms the metal's internal structure, creating a harder and more stable crystalline form. The exact temperature and duration depend on the type of metal and the desired properties. Tempering often follows hardening to reduce brittleness and improve toughness. This process is widely used in industries requiring durable and high-strength materials, such as automotive, aerospace, and construction.
Key Points Explained:
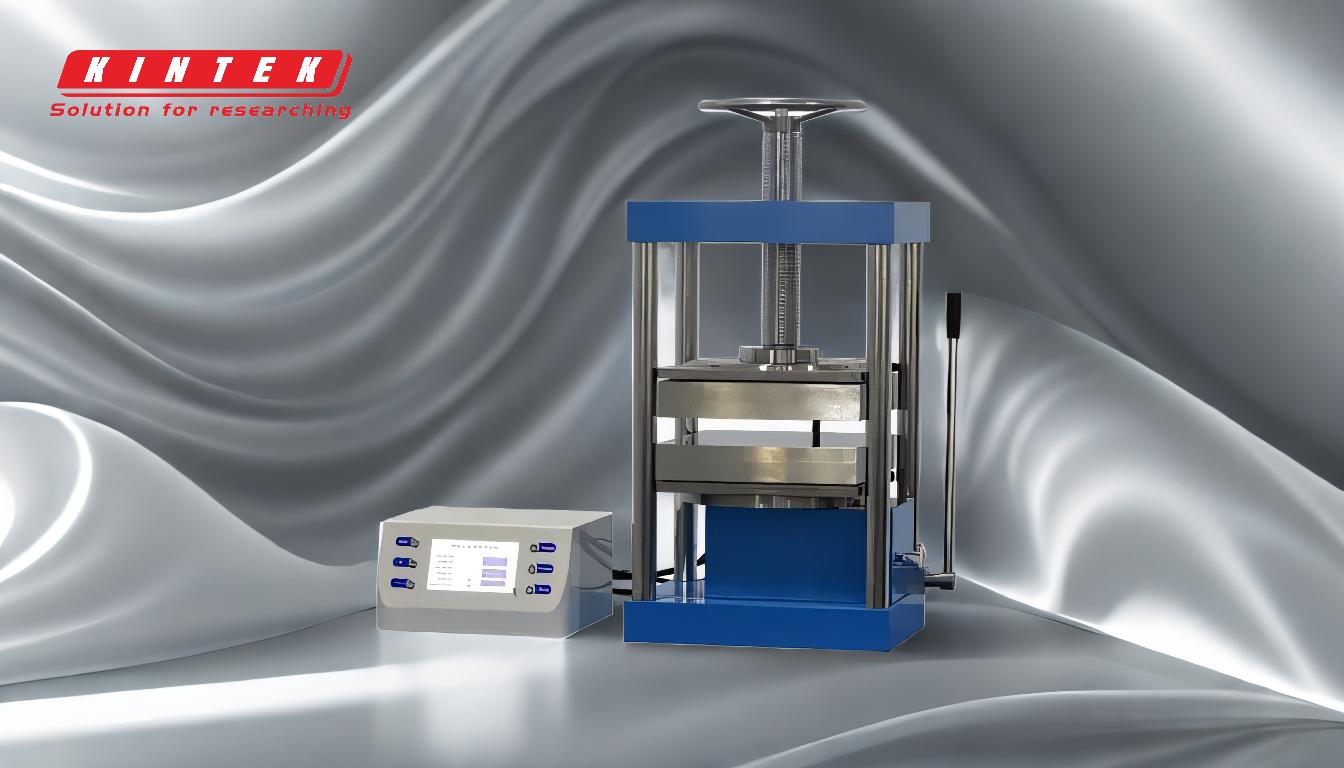
-
Definition of Hardening Heat Treatment:
- Hardening heat treatment is a process used to increase the hardness and strength of metals, particularly steel, by altering their internal crystalline structure.
- It involves heating the metal to a specific temperature, holding it there, and then rapidly cooling it.
-
Temperature Range for Hardening:
- For steel, the hardening temperature is typically above the upper critical temperature, which is often over 900°C.
- This temperature range ensures that the metal's internal structure transforms into austenite, a phase that allows for the formation of a harder structure upon rapid cooling.
-
Importance of Rapid Cooling (Quenching):
- Rapid cooling, or quenching, is essential to lock in the hardened structure.
- Quenching mediums include oil, water, brine, or gas, each chosen based on the metal type and desired properties.
- The cooling rate must be carefully controlled to avoid cracking or warping.
-
Soaking Time:
- The metal is held at the hardening temperature for a specific duration, typically one hour per inch of thickness.
- This soaking period ensures uniform heating and transformation of the metal's internal structure.
-
Purpose of Hardening:
- Hardening increases the metal's hardness, wear resistance, and strength.
- It is particularly useful for components subjected to high stress or wear, such as gears, tools, and structural parts.
-
Tempering After Hardening:
- Tempering is often performed after hardening to reduce brittleness and improve toughness.
- It involves reheating the metal to a lower temperature and then cooling it, which introduces ductility and reduces the risk of cracking under pressure.
-
Applications of Hardening Heat Treatment:
- Hardening is widely used in industries requiring durable and high-strength materials, such as automotive, aerospace, construction, and tool manufacturing.
- It is essential for producing components that can withstand high stress, wear, and harsh environments.
-
Types of Hardening Processes:
- Neutral Hardening: Used to produce strength and toughness in highly stressed parts.
- Precipitation Hardening: Increases yield strength or high-temperature strength by subjecting the metal to elevated temperatures.
- Surface Hardening: Enhances the hardness of the metal's surface while maintaining a tough core.
-
Factors Influencing Hardening:
- The type of metal and its composition.
- The desired mechanical properties (e.g., hardness, toughness).
- The quenching medium and cooling rate.
- The size and shape of the metal part.
-
Challenges and Considerations:
- Overheating can lead to grain growth, reducing the metal's strength.
- Improper cooling can cause cracking, warping, or residual stresses.
- The process requires precise control of temperature, time, and cooling rates to achieve the desired properties.
By understanding these key points, a purchaser of equipment or consumables can make informed decisions about the hardening heat treatment process, ensuring that the materials meet the required specifications and performance standards.
Summary Table:
Key Aspect | Details |
---|---|
Definition | Process to increase metal hardness and strength by altering crystalline structure. |
Temperature Range | Typically above 900°C for steel to transform internal structure. |
Quenching Importance | Rapid cooling locks in hardened structure; mediums include oil, water, or gas. |
Soaking Time | 1 hour per inch of thickness for uniform heating. |
Purpose | Increases hardness, wear resistance, and strength for high-stress components. |
Tempering | Reduces brittleness and improves toughness post-hardening. |
Applications | Automotive, aerospace, construction, and tool manufacturing. |
Types of Hardening | Neutral, precipitation, and surface hardening for specific properties. |
Challenges | Overheating, improper cooling, and precise control of parameters required. |
Optimize your metal components with expert hardening heat treatment—contact us today for tailored solutions!