High vacuum deposition results in processes like Physical Vapor Deposition (PVD), including techniques such as electron-beam evaporation, resistive evaporation, and magnetron sputtering. These methods are favored in high vacuum environments because they minimize contamination, ensure long mean free paths for particles, and provide precise control over the deposition process. High vacuum conditions are particularly beneficial for producing high-purity, defect-free thin films, which are essential in applications like nanotechnology and semiconductor manufacturing. The reduced particle density in high vacuum environments also allows for cleaner and more controlled deposition, making it ideal for achieving high-quality coatings.
Key Points Explained:
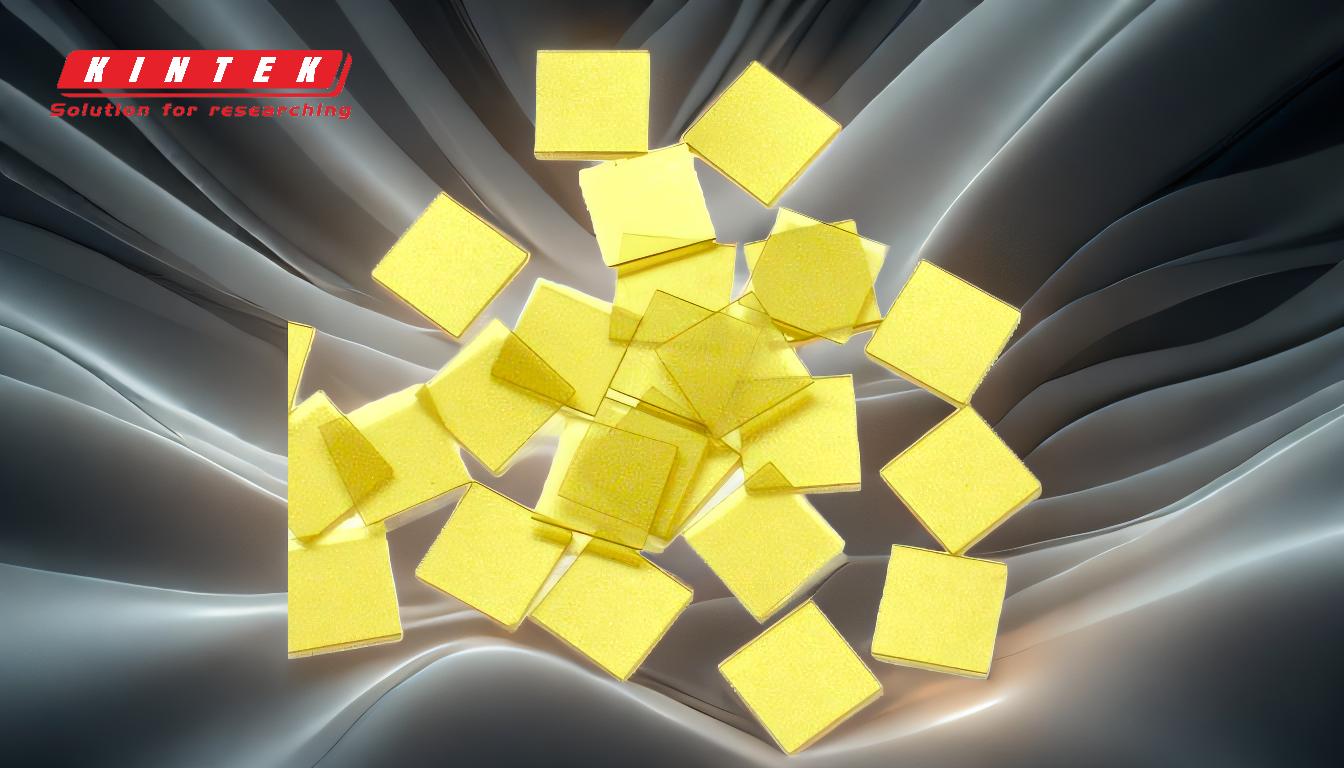
-
High Vacuum Deposition Techniques:
- Physical Vapor Deposition (PVD): This is a common type of deposition that occurs in high vacuum environments. PVD includes methods like electron-beam evaporation, resistive evaporation, and magnetron sputtering.
- Electron-Beam Evaporation: This technique uses a high-energy electron beam to heat and vaporize the material, which then condenses on the substrate. It is particularly effective for depositing high-purity thin films.
- Resistive Evaporation: In this method, the material is heated using a resistive element until it vaporizes and deposits onto the substrate. It is flexible and suitable for most metals.
- Magnetron Sputtering: This technique involves bombarding a target material with ions to eject atoms, which then deposit onto the substrate. It is known for producing high-purity coatings with minimal defects.
-
Advantages of High Vacuum Deposition:
- Reduced Contamination: High vacuum environments minimize the presence of undesirable atoms and molecules, leading to cleaner and more controlled deposition processes.
- Long Mean Free Path: The reduced particle density in high vacuum conditions allows particles to travel longer distances without collisions, ensuring a more uniform deposition.
- Precise Control: High vacuum provides a means for controlling gas and vapor composition, as well as mass flow into the processing chamber, which is crucial for achieving high-quality coatings.
-
Applications of High Vacuum Deposition:
- Nanotechnology: High vacuum deposition techniques like magnetron sputtering are widely used in nanotechnology to produce high-purity, defect-free thin films.
- Semiconductor Manufacturing: The precise control and reduced contamination offered by high vacuum deposition are essential for producing high-quality semiconductor devices.
- Optical Coatings: High vacuum deposition is used to create optical coatings with specific reflective or anti-reflective properties, which are critical in various optical applications.
-
Comparison with Other Deposition Techniques:
- Chemical Vapor Deposition (CVD): Unlike PVD, CVD involves chemical reactions to deposit materials. High vacuum CVD (UHV-CVD) is used for extremely clean and controlled environments.
- Atmospheric Pressure CVD (APCVD): This technique operates at ambient pressure and is less controlled compared to high vacuum methods, making it less suitable for high-purity applications.
- Plasma Enhanced CVD (PECVD): This method uses plasma to enhance the chemical reactions, but it still operates at higher pressures compared to high vacuum techniques, which can introduce more contaminants.
-
Process Steps in High Vacuum Deposition:
- Ramp Up: The chamber is prepared by gradually increasing temperature and decreasing pressure to achieve high vacuum conditions.
- Etching: The substrate is cleaned using plasma etching to improve adhesion of the deposited material.
- Coating: The material is projected onto the substrate using techniques like electron-beam evaporation or magnetron sputtering.
- Ramp Down: The chamber is returned to room temperature and ambient pressure using a cooling system, completing the deposition process.
In summary, high vacuum deposition is essential for producing high-quality, contamination-free thin films. Techniques like PVD, including electron-beam evaporation and magnetron sputtering, are particularly effective in these environments due to their ability to provide precise control and reduce contamination. These methods are widely used in critical applications such as nanotechnology and semiconductor manufacturing, where the quality and purity of the deposited films are paramount.
Summary Table:
Aspect | Details |
---|---|
Techniques | Physical Vapor Deposition (PVD), Electron-Beam Evaporation, Magnetron Sputtering |
Advantages | Reduced contamination, long mean free path, precise control |
Applications | Nanotechnology, semiconductor manufacturing, optical coatings |
Comparison | Superior to CVD, APCVD, and PECVD for high-purity applications |
Process Steps | Ramp up, etching, coating, ramp down |
Discover how high vacuum deposition can elevate your manufacturing process—contact our experts today!