Hot isostatic pressing (HIP) is a manufacturing process that was invented in the mid-20th century. It involves applying high temperature and uniform pressure to materials to improve their density and mechanical properties. This technique is widely used in industries such as aerospace, automotive, and medical devices to produce high-performance components. The invention of HIP marked a significant advancement in materials science, enabling the production of complex shapes with enhanced structural integrity.
Key Points Explained:
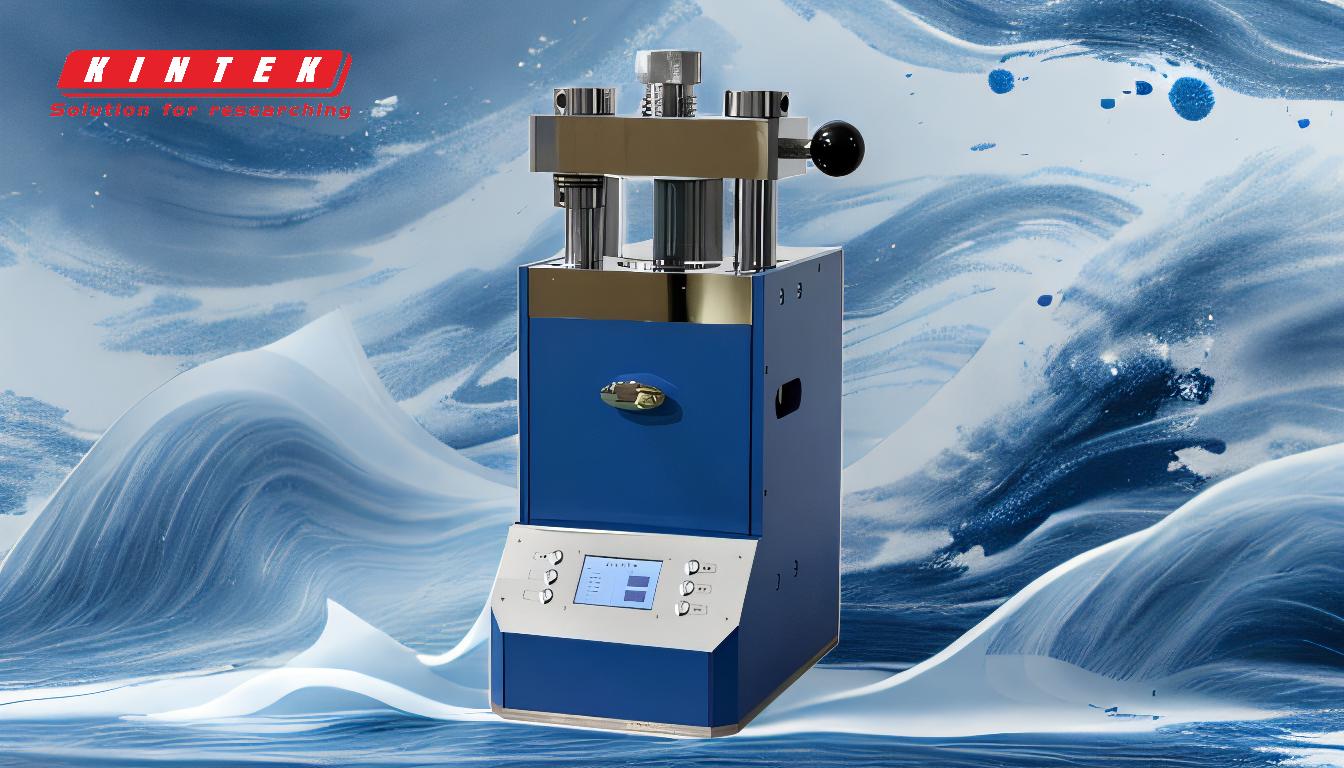
-
Definition of Hot Isostatic Pressing (HIP):
- HIP is a process that uses high temperature and isostatic pressure to densify materials, such as metals, ceramics, and composites. This method ensures uniform pressure distribution, which eliminates voids and improves material properties.
-
Invention Timeline:
- Hot isostatic pressing was invented in the 1950s. The process was developed as a solution to address the limitations of traditional manufacturing methods, particularly in achieving high-density materials with minimal defects.
-
Key Applications:
- HIP is widely used in industries requiring high-performance materials, such as:
- Aerospace: For manufacturing turbine blades and other critical components.
- Medical: To produce biocompatible implants like hip joints and dental prosthetics.
- Automotive: For creating lightweight, durable parts.
- The process is also essential in the production of advanced ceramics and composite materials.
- HIP is widely used in industries requiring high-performance materials, such as:
-
Advantages of HIP:
- Improved Density: HIP eliminates porosity, resulting in materials with higher density and better mechanical properties.
- Enhanced Strength: The process improves the fatigue resistance and overall strength of components.
- Complex Shapes: HIP enables the production of intricate geometries that are difficult to achieve with conventional methods.
-
Comparison with Warm Isostatic Pressing:
- While HIP operates at high temperatures, warm isostatic press is a similar process but conducted at lower temperatures. Warm isostatic pressing is often used for materials that cannot withstand the extreme heat of HIP, making it a versatile alternative for specific applications.
-
Evolution and Modern Use:
- Since its invention, HIP has evolved with advancements in technology, such as improved pressure vessels and control systems. Today, it is a cornerstone of advanced manufacturing, enabling the production of high-quality, reliable components for critical applications.
In summary, hot isostatic pressing was invented in the 1950s and has since become a vital process in materials science and manufacturing. Its ability to produce high-density, defect-free materials makes it indispensable in industries requiring precision and performance.
Summary Table:
Aspect | Details |
---|---|
Invention Year | 1950s |
Key Industries | Aerospace, Medical, Automotive, Advanced Ceramics |
Main Advantages | Improved density, enhanced strength, ability to produce complex shapes |
Comparison with WIP | HIP uses high temperatures; WIP operates at lower temperatures |
Modern Applications | Critical components in aerospace, medical implants, lightweight auto parts |
Learn how hot isostatic pressing can transform your manufacturing process—contact us today!