Atomic layer deposition (ALD) is the deposition technique that allows for the deposition of ultra-thin layers with atomic layer precision. ALD achieves this through sequential, self-limiting surface reactions, where precursor gases are alternately introduced into the reaction chamber. Each precursor reacts with the substrate or the previously deposited layer, forming a chemisorbed monolayer. Once the surface is fully saturated, excess precursor and reaction byproducts are purged before introducing the next precursor. This cycle is repeated until the desired film thickness is achieved. ALD is unique in its ability to control film thickness at the atomic level, making it ideal for applications requiring ultra-thin, uniform, and defect-free coatings.
Key Points Explained:
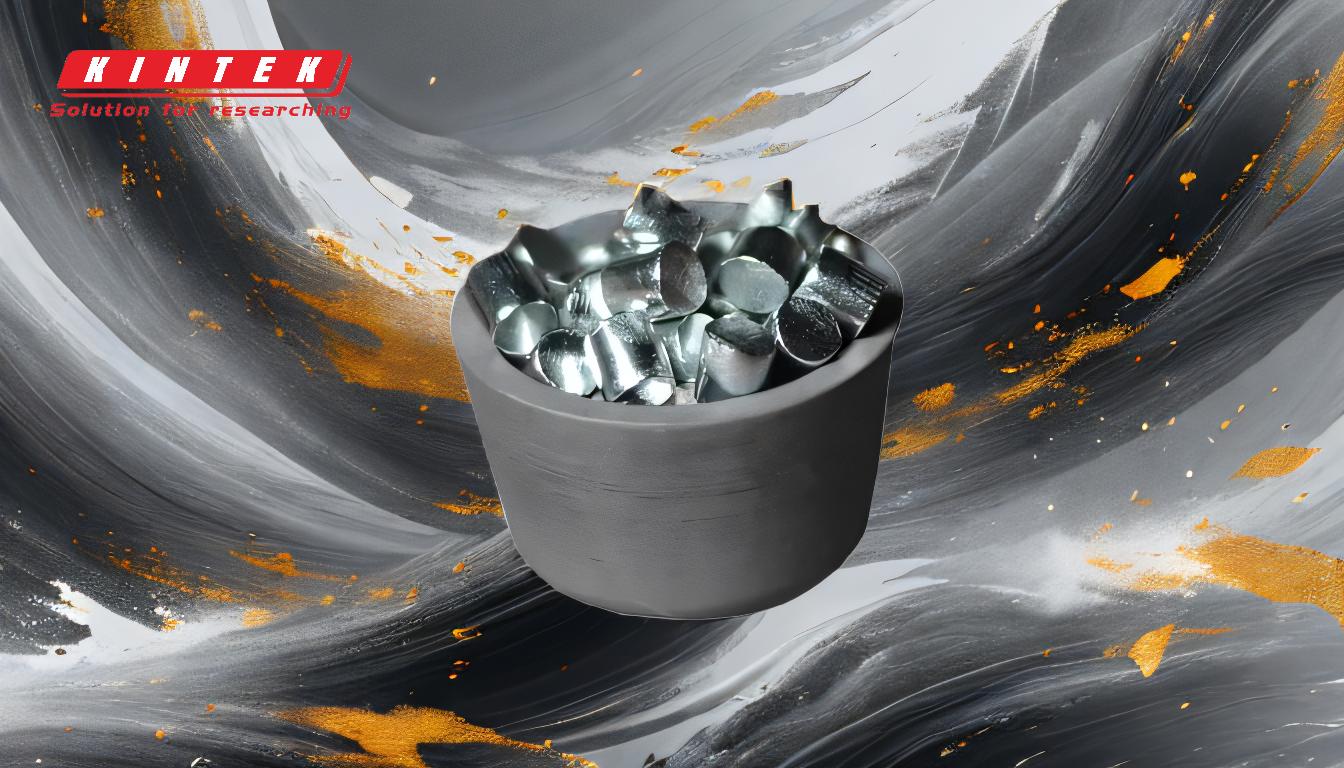
-
Atomic Layer Deposition (ALD) Overview:
- ALD is a chemical deposition technique that enables the deposition of ultra-thin layers with atomic precision.
- It operates through sequential, self-limiting surface reactions, ensuring precise control over film thickness.
-
Mechanism of ALD:
- Sequential Precursor Introduction: Two or more precursor gases are alternately introduced into the reaction chamber.
- Self-Limiting Reactions: Each precursor reacts with the substrate or the previously deposited layer, forming a chemisorbed monolayer.
- Purging: Excess precursor and reaction byproducts are purged before introducing the next precursor.
- Cycle Repetition: The process is repeated until the desired film thickness is achieved.
-
Advantages of ALD:
- Atomic Layer Precision: ALD allows for the deposition of films with atomic layer precision, making it ideal for applications requiring ultra-thin coatings.
- Uniformity and Conformality: The self-limiting nature of the reactions ensures uniform and conformal coatings, even on complex geometries.
- Defect-Free Coatings: ALD produces high-purity coatings with low levels of defects, suitable for high-performance applications.
-
Comparison with Other Deposition Techniques:
- Physical Vapor Deposition (PVD): Techniques like magnetron sputtering and electron beam evaporation are commonly used for thin film deposition but do not offer the same level of atomic precision as ALD.
- Chemical Vapor Deposition (CVD): While CVD can produce high-quality films, it lacks the self-limiting mechanism of ALD, making it less precise for ultra-thin layers.
- Other Chemical Methods: Techniques like electroplating, sol-gel, dip coating, and spin coating are less precise and do not offer atomic layer control.
-
Applications of ALD:
- Semiconductor Industry: ALD is widely used in the semiconductor industry for depositing high-k dielectrics, gate oxides, and other critical layers in integrated circuits.
- Nanotechnology: ALD is essential for fabricating nanostructures and nanodevices that require precise thickness control.
- Optoelectronics: ALD is used to deposit thin films for LEDs, solar cells, and other optoelectronic devices.
- Protective Coatings: ALD is employed to create ultra-thin protective coatings for corrosion resistance and barrier layers in various applications.
-
Limitations of ALD:
- Deposition Rate: ALD is generally slower compared to other deposition techniques due to its sequential nature.
- Cost: The equipment and precursors used in ALD can be expensive, making it less suitable for high-volume production.
- Material Limitations: Not all materials can be deposited using ALD, and the choice of precursors is critical for successful deposition.
In summary, atomic layer deposition (ALD) stands out as the premier technique for depositing ultra-thin layers with atomic precision. Its unique self-limiting mechanism ensures uniform, conformal, and defect-free coatings, making it indispensable in advanced applications across various industries. While it has some limitations in terms of deposition rate and cost, its unparalleled precision and control make it the go-to method for applications requiring atomic layer accuracy.
Summary Table:
Key Aspect | Details |
---|---|
Mechanism | Sequential, self-limiting surface reactions with precursor gases. |
Advantages | Atomic layer precision, uniformity, conformality, and defect-free coatings. |
Applications | Semiconductors, nanotechnology, optoelectronics, and protective coatings. |
Limitations | Slower deposition rate, higher cost, and material limitations. |
Comparison with PVD & CVD | Superior atomic precision compared to PVD and CVD techniques. |
Unlock the potential of atomic layer deposition for your projects—contact our experts today!