Stainless steel is known for its corrosion resistance and durability, but these properties also make it challenging to braze. The primary issue lies in the presence of oxide films on the surface, which hinder the wettability and spreading of the filler metal. To achieve a successful brazing process, strict cleaning procedures must be followed to remove contaminants like grease and oil films. Brazing methods such as flame, induction, or furnace heating can be used, with vacuum brazing being a particularly effective approach due to its ability to minimize oxidation. The process involves careful preparation, assembly, and post-brazing inspection to ensure a strong and reliable joint.
Key Points Explained:
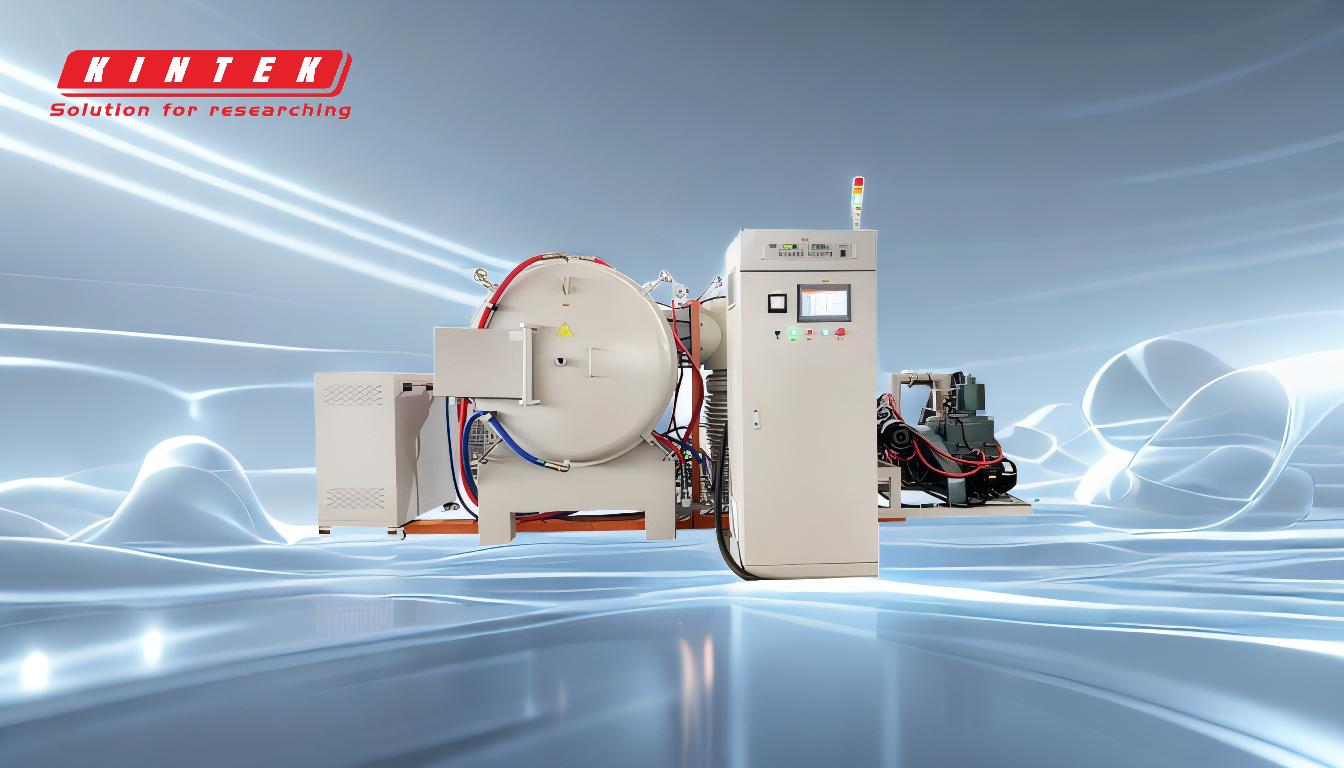
-
Oxide Films on Stainless Steel:
- Stainless steel naturally forms a thin oxide layer on its surface, which is crucial for its corrosion resistance. However, this oxide layer becomes a significant obstacle during brazing.
- The oxide film reduces the wettability of the filler metal, meaning the molten filler metal cannot spread evenly across the surface. This results in poor adhesion and weak joints.
- To overcome this, the oxide layer must be removed or minimized before brazing. This can be achieved through mechanical cleaning, chemical treatments, or by using a controlled atmosphere during brazing.
-
Importance of Cleaning:
- Before brazing, stainless steel must undergo stringent cleaning to remove grease, oil, and other contaminants. These impurities can interfere with the brazing process by creating additional barriers between the base metal and the filler metal.
- Cleaning methods include degreasing with solvents, abrasive cleaning, or chemical etching. After cleaning, brazing should be performed immediately to prevent reformation of the oxide layer.
-
Brazing Methods:
- Stainless steel can be brazed using various heating methods, including flame, induction, and furnace heating. Each method has its advantages and is chosen based on the specific application and requirements.
- Flame brazing is suitable for small-scale or manual operations, while induction brazing offers precise and localized heating. Furnace brazing, especially in a vacuum or controlled atmosphere, is ideal for complex or high-volume production.
-
Vacuum Brazing Process:
- Vacuum brazing is particularly effective for stainless steel because it eliminates the presence of oxygen, preventing the formation of oxide films during the process.
- The process involves three main steps:
- Preparation: Cleaning the stainless steel components and preparing the filler metal.
- Assembly and Filling: Positioning the components and placing the filler metal in the joint area.
- Inspection: After the furnace process, the brazed joint is inspected for quality, strength, and integrity.
-
Filler Metal Selection:
- The choice of filler metal is critical in brazing stainless steel. Commonly used filler metals include silver-based alloys, nickel-based alloys, and copper-based alloys.
- The filler metal must have a lower melting point than the base metal and should be compatible with stainless steel to ensure proper bonding and joint strength.
-
Post-Brazing Considerations:
- After brazing, the joint should be inspected for defects such as voids, cracks, or incomplete bonding. Non-destructive testing methods like X-ray or ultrasonic inspection can be used.
- Proper cooling and post-brazing treatments may also be required to relieve stresses and enhance the joint's mechanical properties.
By addressing these key points, the challenges of brazing stainless steel can be effectively managed, leading to strong and durable joints suitable for various industrial applications.
Summary Table:
Key Challenge | Solution |
---|---|
Oxide Films on Surface | Remove or minimize oxide layers via cleaning or controlled atmosphere. |
Contaminants (Grease/Oil) | Use degreasing, abrasive cleaning, or chemical etching for thorough cleaning. |
Brazing Methods | Flame, induction, or furnace heating; vacuum brazing minimizes oxidation. |
Filler Metal Selection | Choose compatible alloys (silver, nickel, copper) with lower melting points. |
Post-Brazing Inspection | Inspect joints for defects using X-ray or ultrasonic methods. |
Need expert advice on brazing stainless steel? Contact us today for tailored solutions!