Heating elements are critical components in various industrial and laboratory applications, and selecting the right material is essential for efficiency, durability, and performance. Molybdenum disilicide (MoSi2) is one of the most advanced materials used for heating elements, offering unique advantages such as high operating temperatures, stable resistance, and long life. However, it also comes with certain disadvantages, including higher costs and the need for specialized power control equipment. This analysis explores the suitability of MoSi2 as a heating element, its advantages, disadvantages, and applications, providing a comprehensive understanding for potential purchasers.
Key Points Explained:
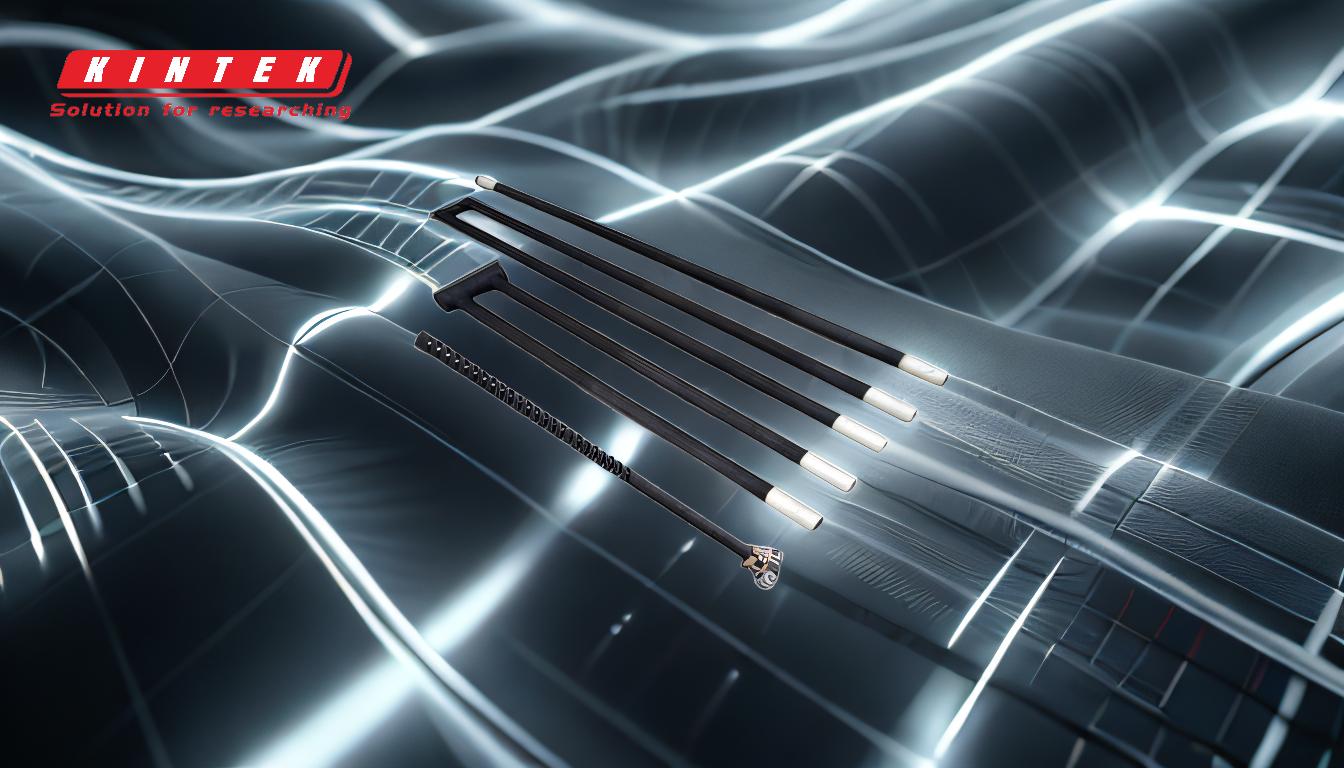
-
Advantages of MoSi2 Heating Elements
- High Operating Temperatures: MoSi2 heating elements can withstand the highest operating temperatures among comparable materials, making them ideal for applications requiring extreme heat.
- Stable Resistance: Their resistance remains stable over time, allowing for the series connection of new and old elements without performance degradation.
- Fast Thermal Cycling: MoSi2 elements can undergo rapid heating and cooling cycles without degradation, ensuring consistent performance in dynamic environments.
- Ease of Replacement: These elements can be replaced even while the furnace is hot, minimizing downtime in industrial processes.
- Long Life: MoSi2 heating elements have the longest inherent lifespan among electric heating elements, reducing the frequency of replacements and maintenance costs.
- Versatility: They are available in various shapes and sizes, making them adaptable to a wide range of furnace designs and applications.
For more details, refer to the MoSi2 heating element topic.
-
Purity Grades of MoSi2 Heating Elements
- Industrial Purity: Suitable for general laboratory and industrial applications, offering a balance of performance and cost-effectiveness.
- High Purity: Designed for specialized applications such as dental, medical, optical, and semiconductor industries, where contamination must be minimized.
-
Disadvantages of MoSi2 Heating Elements
- Cost: MoSi2 elements are the most expensive among heating element materials, which may be a limiting factor for budget-conscious projects.
- Power Control Requirements: They require more costly power control equipment, including transformers, due to their low voltage and high startup current characteristics.
- Fragility: Being ceramic-based, MoSi2 elements are prone to fracture if mishandled or exposed to mechanical stress.
-
Applications of MoSi2 Heating Elements
- High-Temperature Furnaces: Ideal for applications requiring temperatures above 1700°C, such as sintering, annealing, and heat treatment processes.
- Clean Environments: High-purity MoSi2 elements are used in industries like semiconductor manufacturing, where contamination control is critical.
- Research and Development: Their stability and long life make them suitable for R&D applications involving repeated thermal cycling.
-
Comparison with Other Heating Element Materials
- Metallic Elements: While metallic elements like Kanthal or Nichrome are more cost-effective and easier to control, they cannot match the high-temperature capabilities and longevity of MoSi2.
- Silicon Carbide (SiC): SiC elements are also used in high-temperature applications but are less durable and more prone to oxidation compared to MoSi2.
-
Considerations for Purchasers
- Application Requirements: Evaluate the temperature range, thermal cycling needs, and environmental conditions of your application.
- Budget: Consider the initial cost of MoSi2 elements and the associated power control equipment.
- Maintenance and Lifespan: Factor in the long-term benefits of reduced maintenance and longer lifespan when comparing costs.
- Fragility: Ensure proper handling and installation to minimize the risk of fracture.
In conclusion, MoSi2 heating elements are a premium choice for high-temperature applications, offering unmatched performance, durability, and versatility. However, their higher cost and specialized requirements make them more suitable for applications where these factors are justified by the need for extreme temperatures, stability, and long-term reliability.
Summary Table:
Aspect | Details |
---|---|
Advantages | High operating temps, stable resistance, fast thermal cycling, long life |
Purity Grades | Industrial (general use), High (specialized applications) |
Disadvantages | High cost, specialized power control, fragility |
Applications | High-temp furnaces, clean environments, R&D |
Comparison | Outperforms metallic and SiC elements in high-temp durability and longevity |
Ready to enhance your high-temperature processes? Contact us today to learn more about MoSi2 heating elements!