Refractory linings in furnaces are critical for maintaining high temperatures, ensuring thermal insulation, and protecting the furnace structure. The choice of material depends on the furnace type, operating temperature, and specific application requirements. Common materials include fire clay, high alumina, silica, magnesia, silicon carbide, and alumina fibers. Each material offers unique properties such as high service temperature, thermal insulation, rapid heat resistance, and durability. Multi-layer designs incorporating lightweight alumina ceramic fibers and insulation boards are also used to enhance energy efficiency and reduce heat loss.
Key Points Explained:
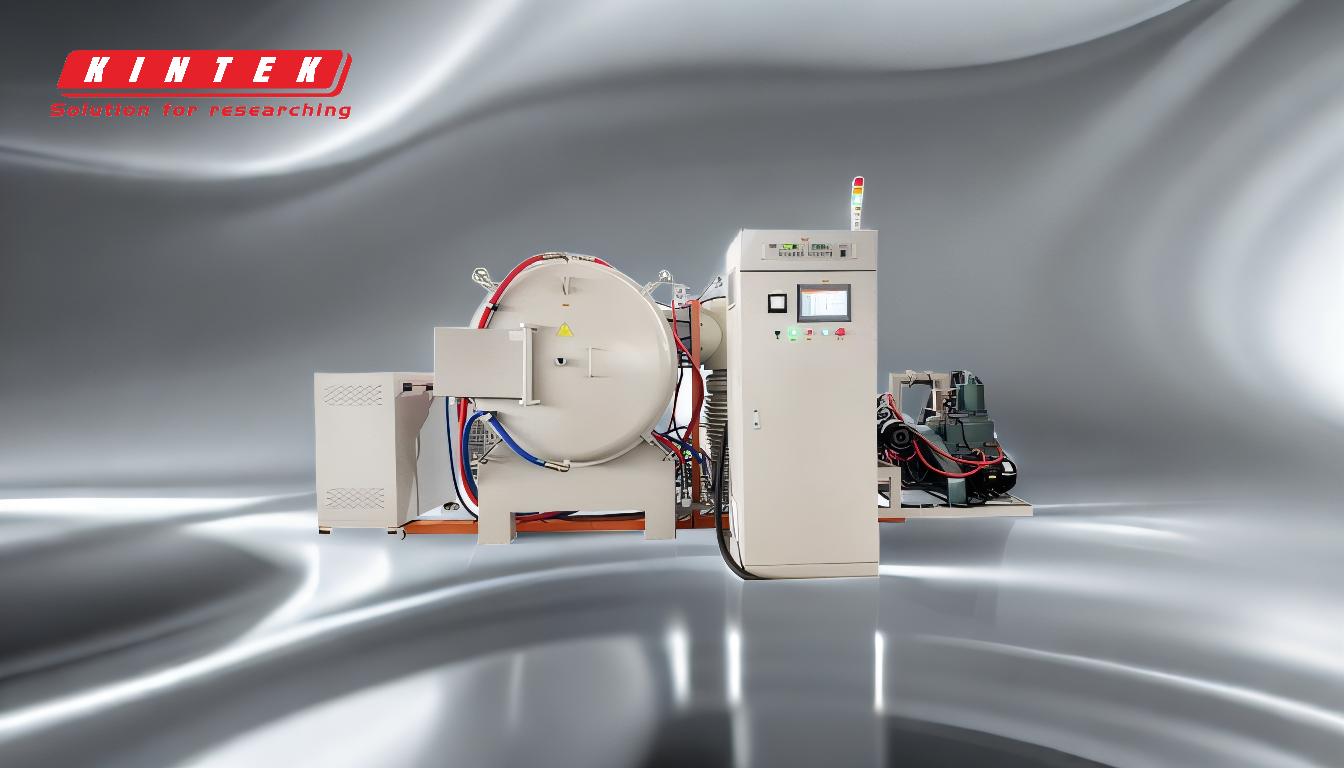
-
Common Refractory Materials:
- Fire Clay: Made from clay, it is suitable for lower-temperature furnaces due to its cost-effectiveness and adequate thermal resistance.
- High Alumina: Offers superior strength and resistance to high temperatures, making it ideal for demanding applications.
- Silica: Known for its excellent thermal shock resistance and stability at high temperatures.
- Magnesia: Used in high-temperature environments, particularly in basic oxygen furnaces, due to its resistance to alkaline slags.
- Silicon Carbide (SiC): Provides high thermal conductivity, strength, and resistance to thermal shock, often used in muffle furnaces.
- Alumina Fibers: Lightweight and highly insulating, these fibers are used in vacuum-formed materials and multi-layer designs for energy efficiency.
-
Material Properties and Applications:
- High-Purity Alumina Fiber: Ensures high service temperatures, small heat storage capacity, rapid heat and cold resistance, and excellent thermal insulation. It is often used in vacuum-formed materials and lightweight hollow aluminum oxide plates.
- Multi-Layer Insulation Design: Combines lightweight alumina ceramic fibers with high-quality insulation boards. This design minimizes heat loss, reduces energy consumption, and avoids the use of asbestos, making it environmentally friendly.
-
Advantages of Specific Materials:
- Fire Clay: Economical and suitable for less demanding applications.
- High Alumina and Silicon Carbide: Provide durability and precision in high-temperature processes, such as in muffle furnaces.
- Alumina Fibers and Multi-Layer Designs: Offer superior thermal insulation, rapid heating and cooling capabilities, and resistance to cracking and slag formation.
-
Selection Criteria:
- Temperature Requirements: Materials like high alumina and silicon carbide are chosen for high-temperature applications.
- Thermal Insulation Needs: Alumina fibers and multi-layer designs are preferred for their low heat loss and energy efficiency.
- Mechanical Strength: High-strength materials like silicon carbide and high alumina are selected for their durability and resistance to wear.
-
Environmental and Safety Considerations:
- Asbestos-Free Designs: Modern refractory materials avoid asbestos, ensuring safer working conditions and compliance with environmental regulations.
- Energy Efficiency: Multi-layer insulation designs and lightweight materials contribute to reduced energy consumption and operational costs.
By understanding these key points, a purchaser can make informed decisions based on the specific requirements of their furnace application, ensuring optimal performance and longevity of the refractory lining.
Summary Table:
Material | Key Properties | Applications |
---|---|---|
Fire Clay | Cost-effective, adequate thermal resistance | Lower-temperature furnaces |
High Alumina | Superior strength, high-temperature resistance | Demanding high-temperature applications |
Silica | Excellent thermal shock resistance, stability at high temperatures | High-temperature stability |
Magnesia | Resistance to alkaline slags | Basic oxygen furnaces |
Silicon Carbide | High thermal conductivity, strength, thermal shock resistance | Muffle furnaces |
Alumina Fibers | Lightweight, highly insulating, rapid heat and cold resistance | Multi-layer designs, energy-efficient applications |
Need the right refractory lining for your furnace? Contact our experts today for tailored solutions!