Ceramics are widely used for furnace linings due to their exceptional thermal insulation properties, heat resistance, and chemical stability. They are particularly effective in maintaining stable and controlled temperatures, which is critical for industrial and laboratory processes. Ceramic materials, such as ceramic fiber, offer low thermal conductivity, reducing heat loss and improving energy efficiency. Additionally, their resistance to chemical corrosion makes them ideal for environments where exposure to high temperatures and corrosive substances is common. These properties ensure durability, safety, and optimal performance in furnace operations.
Key Points Explained:
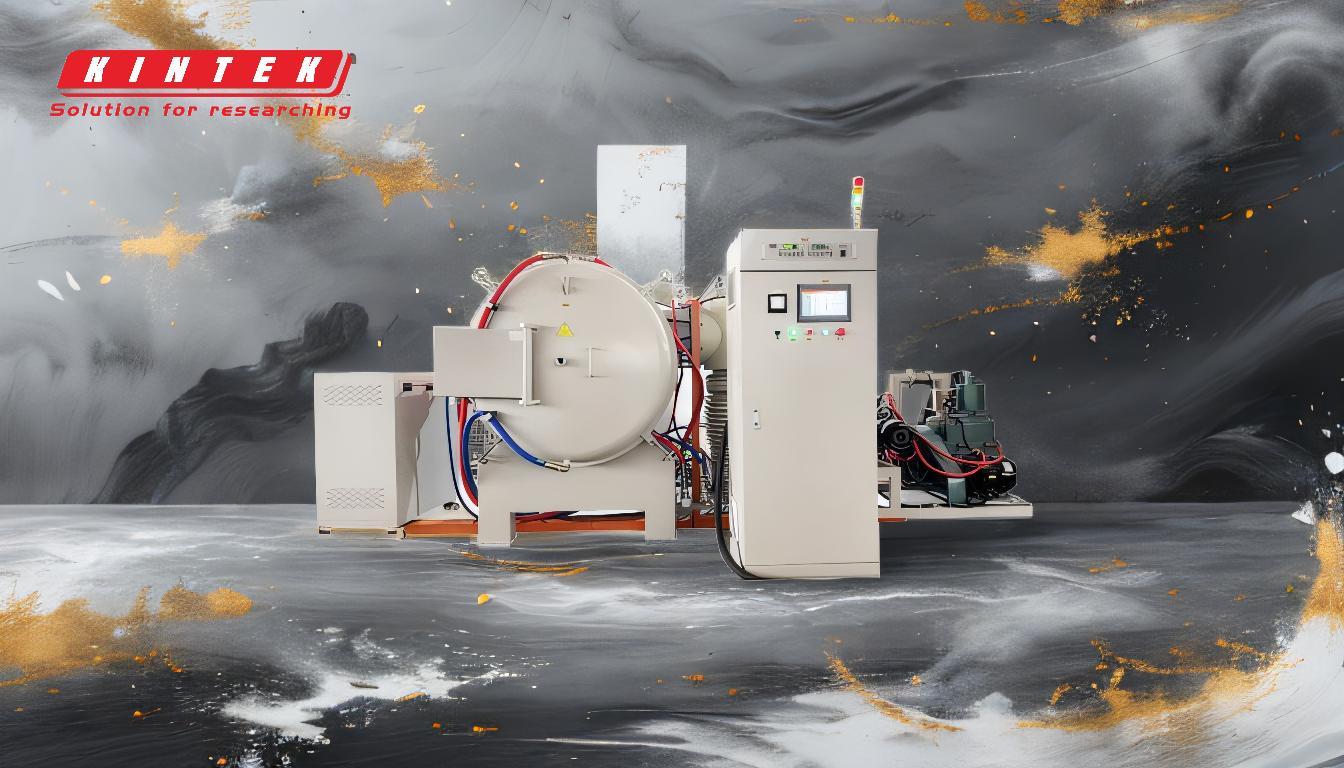
-
Thermal Insulation Properties
- Ceramics, especially ceramic fiber, are known for their excellent thermal insulation capabilities.
- They minimize heat transfer, ensuring that the furnace retains heat efficiently and operates at consistent temperatures.
- This property is crucial for processes requiring precise temperature control, such as metal heat treatment or glass manufacturing.
-
Heat Resistance
- Ceramics can withstand extremely high temperatures without degrading, making them suitable for furnace linings.
- Their ability to maintain structural integrity under thermal stress ensures long-term durability and reliability.
- This heat resistance is vital for applications like kilns, where temperatures can exceed 1000°C.
-
Low Thermal Conductivity
- The low thermal conductivity of ceramics reduces heat loss, improving the energy efficiency of the furnace.
- This property helps in maintaining uniform temperatures throughout the furnace, which is essential for consistent process outcomes.
-
Chemical Corrosion Resistance
- Ceramics are highly resistant to chemical corrosion, even in harsh environments.
- This makes them ideal for furnaces that handle corrosive materials or gases, such as those used in chemical processing or metallurgy.
- Their resistance to chemical degradation ensures a longer lifespan for the furnace lining.
-
Durability and Safety
- The combination of thermal and chemical resistance makes ceramics a durable and safe choice for furnace linings.
- They reduce the risk of furnace failure, which can lead to costly downtime or safety hazards.
- Their stability under extreme conditions ensures reliable performance over extended periods.
-
Applications in Industrial and Laboratory Settings
- Ceramic linings are used in a variety of furnaces, including muffle furnaces, kilns, and industrial ovens.
- Their versatility makes them suitable for diverse applications, from metalworking to glassmaking and chemical processing.
- The use of ceramics ensures that these processes are carried out efficiently and safely.
In summary, ceramics are an ideal material for furnace linings due to their thermal insulation, heat resistance, low thermal conductivity, and chemical corrosion resistance. These properties make them indispensable in both industrial and laboratory settings, ensuring efficient, safe, and reliable furnace operations.
Summary Table:
Property | Benefits |
---|---|
Thermal Insulation | Minimizes heat transfer, ensures consistent temperatures, and improves efficiency. |
Heat Resistance | Withstands extreme temperatures, ensuring durability and reliability. |
Low Thermal Conductivity | Reduces heat loss, maintains uniform temperatures, and enhances energy efficiency. |
Chemical Corrosion Resistance | Resists degradation in harsh environments, extending furnace lining lifespan. |
Durability and Safety | Combines thermal and chemical resistance for safe, long-lasting performance. |
Applications | Suitable for muffle furnaces, kilns, and industrial ovens across various industries. |
Upgrade your furnace performance with ceramic linings—contact our experts today to learn more!