Heat treat furnaces for specialty alloys often have atmosphere controls to ensure the success of the heat treatment process. These controls are essential because the atmosphere within the furnace can either protect the metal from harmful elements or facilitate surface reactions that enhance material properties. By precisely regulating gas flow rates, mixtures, and pressure levels, the furnace atmosphere can be tailored to meet specific requirements, ensuring consistent and repeatable results. This controlled environment is crucial for achieving desired material properties, preventing surface defects, and enabling processes like carburizing or hardening. Without proper atmosphere control, the heat treatment of specialty alloys would be inconsistent and unreliable, leading to suboptimal performance in demanding applications.
Key Points Explained:
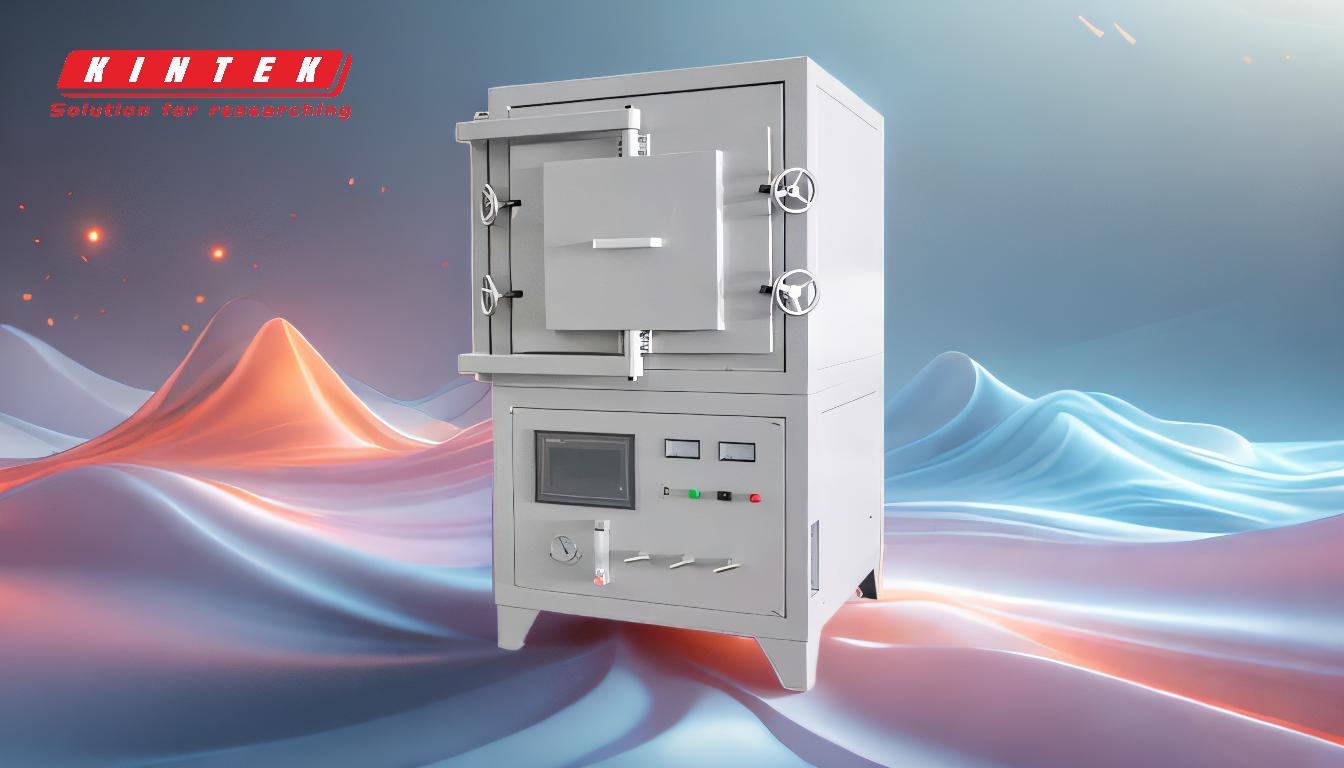
-
Protection from Harmful Elements:
- Purpose: The furnace atmosphere can shield the metal from exposure to harmful elements like oxygen, which can cause oxidation or scaling.
- Mechanism: Inert gases, such as nitrogen or argon, are often used to create a chemically inert environment that prevents unwanted surface reactions.
- Importance: This protection is critical for maintaining the integrity and surface quality of specialty alloys, which are often used in high-performance applications.
-
Facilitation of Surface Reactions:
- Purpose: The atmosphere can also be chemically active, allowing for controlled surface reactions that enhance material properties.
- Mechanism: Gases like carbon monoxide or methane can be introduced to facilitate processes such as carburizing, where carbon is diffused into the surface of the metal to increase hardness.
- Importance: These reactions are essential for achieving specific material characteristics, such as wear resistance or fatigue strength, which are critical for the performance of specialty alloys.
-
Consistency and Repeatability:
- Purpose: Atmosphere controls ensure that the heat treatment process is consistent and repeatable.
- Mechanism: By precisely regulating gas flow rates, mixtures, and pressure levels, the furnace can maintain a stable and uniform environment throughout the process.
- Importance: Consistency is vital for industrial applications where large quantities of parts are treated, and repeatability ensures that each part meets the required specifications.
-
Temperature Control and Uniformity:
- Purpose: Proper atmosphere control contributes to uniform temperature distribution within the furnace.
- Mechanism: The flow of gases helps to distribute heat evenly, preventing hot spots or cold zones that could lead to uneven treatment.
- Importance: Uniform temperature distribution is crucial for achieving the desired material properties and preventing defects such as warping or cracking.
-
Prevention of External Interference:
- Purpose: A tightly sealed furnace environment prevents external contaminants from affecting the heat treatment process.
- Mechanism: The controlled atmosphere is isolated from the external environment, ensuring that only the desired gases are present.
- Importance: This isolation is essential for maintaining the purity of the atmosphere and ensuring that the heat treatment process is not compromised by external factors.
-
Adaptability to Different Processes:
- Purpose: Atmosphere controls allow the furnace to be adapted for different heat treatment processes.
- Mechanism: By adjusting the gas composition and flow rates, the furnace can be configured for processes such as annealing, hardening, or nitriding.
- Importance: This adaptability is crucial for treating a wide range of specialty alloys, each requiring specific conditions to achieve the desired properties.
-
Monitoring and Control:
- Purpose: Advanced atmosphere control systems include monitoring and feedback mechanisms to ensure precise control.
- Mechanism: Sensors and control systems continuously monitor the atmosphere and make adjustments as needed to maintain the desired conditions.
- Importance: This level of control is essential for achieving high-quality results and ensuring that the heat treatment process meets the required standards.
In summary, atmosphere controls in heat treat furnaces for specialty alloys are essential for protecting the metal, facilitating surface reactions, ensuring consistency, maintaining uniform temperatures, preventing external interference, adapting to different processes, and providing precise monitoring and control. These factors collectively ensure that the heat treatment process is successful and that the treated materials meet the required specifications for their intended applications.
Summary Table:
Key Benefit | Purpose | Mechanism | Importance |
---|---|---|---|
Protection from Harmful Elements | Shield metal from oxidation or scaling | Use of inert gases like nitrogen or argon | Maintains integrity and surface quality of specialty alloys |
Facilitation of Surface Reactions | Enable controlled surface reactions to enhance material properties | Introduction of gases like carbon monoxide or methane for processes like carburizing | Achieves wear resistance, fatigue strength, and other critical material traits |
Consistency and Repeatability | Ensure uniform and repeatable heat treatment | Precise regulation of gas flow rates, mixtures, and pressure levels | Vital for industrial applications and meeting required specifications |
Temperature Control and Uniformity | Maintain even temperature distribution | Gas flow helps distribute heat evenly, preventing hot or cold zones | Prevents defects like warping or cracking |
Prevention of External Interference | Isolate the furnace environment from contaminants | Tightly sealed furnace with controlled atmosphere | Ensures purity and prevents process compromise |
Adaptability to Different Processes | Enable flexibility for various heat treatment processes | Adjust gas composition and flow rates for annealing, hardening, or nitriding | Crucial for treating diverse specialty alloys |
Monitoring and Control | Provide precise control over the furnace atmosphere | Sensors and control systems monitor and adjust conditions in real-time | Ensures high-quality results and compliance with standards |
Discover how advanced atmosphere controls can optimize your heat treatment process—contact our experts today!