Determining ash content in coal is crucial for evaluating its quality and suitability for various applications. Ash content represents the inorganic residue left after coal combustion, primarily composed of minerals and impurities. Measuring ash content helps assess the efficiency of coal combustion, its environmental impact, and its economic value. High ash content reduces the calorific value of coal, increases transportation costs, and necessitates additional handling and disposal measures. It also impacts the performance of boilers and other combustion equipment, as ash can cause slagging, fouling, and corrosion. By analyzing ash content, industries can optimize coal usage, reduce operational costs, and comply with environmental regulations.
Key Points Explained:
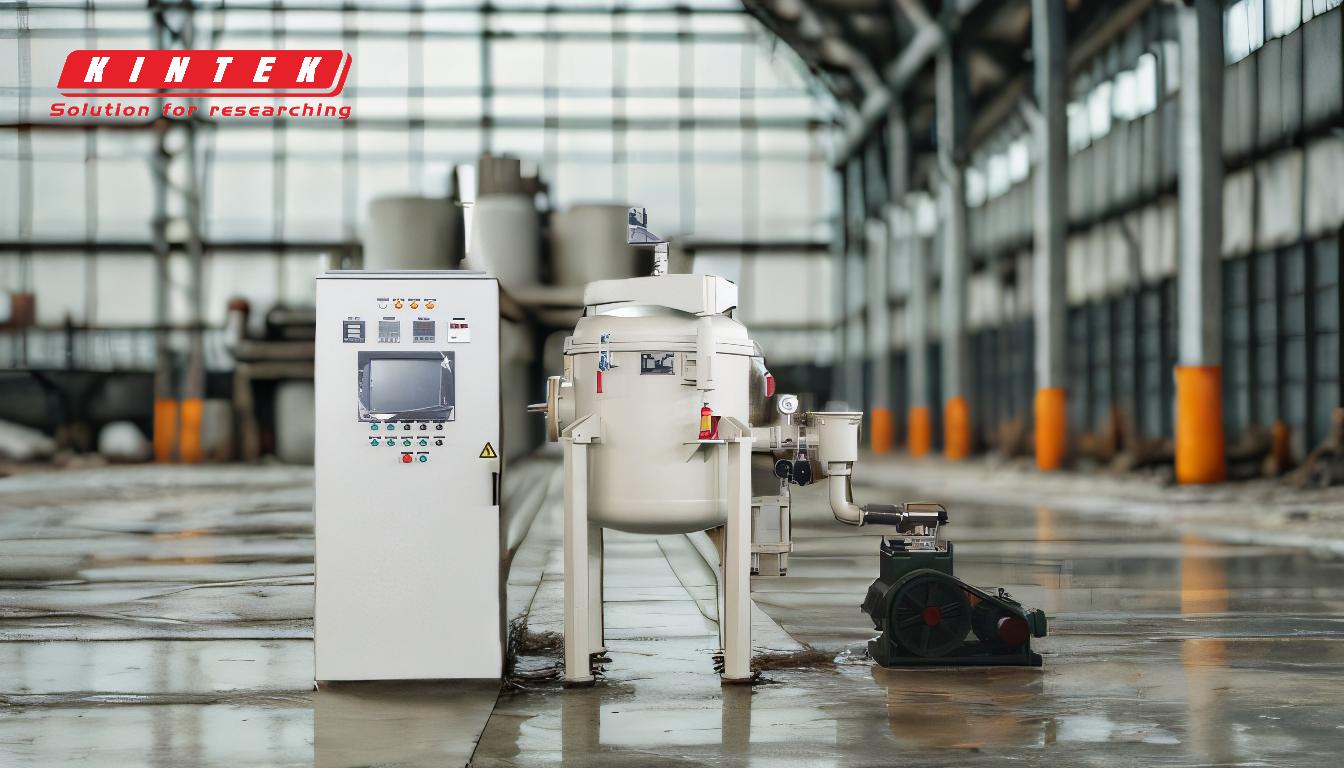
-
Understanding Ash Content in Coal
- Ash content refers to the inorganic, non-combustible residue left after coal is burned.
- It primarily consists of minerals such as silica, alumina, iron oxide, and other trace elements.
- The determination of ash content is a critical parameter in coal quality assessment.
-
Importance of Measuring Ash Content
- Combustion Efficiency: High ash content reduces the calorific value of coal, meaning less energy is produced per unit of coal burned.
- Economic Impact: Coal with high ash content is less economical due to increased transportation and handling costs.
- Environmental Concerns: Ash contains pollutants that can be released into the environment, contributing to air and water pollution.
- Equipment Performance: Ash can cause operational issues such as slagging, fouling, and corrosion in boilers and other combustion equipment.
-
Methods for Determining Ash Content
- Proximate Analysis: A standard method used to determine ash content by burning a coal sample in a controlled environment and measuring the residue.
- Elemental Analysis: Provides detailed information about the composition of ash, including the presence of specific minerals and trace elements.
-
Applications of Ash Content Data
- Coal Grading: Helps classify coal based on its quality and suitability for specific uses, such as power generation or metallurgical processes.
- Process Optimization: Enables industries to adjust combustion parameters to minimize ash-related issues and improve efficiency.
- Regulatory Compliance: Ensures adherence to environmental standards by monitoring and controlling emissions and waste disposal.
-
Challenges Associated with High Ash Content
- Increased Waste Disposal: High ash content generates more waste, requiring proper disposal methods to prevent environmental contamination.
- Operational Costs: Cleaning and maintaining equipment to handle ash increases operational expenses.
- Reduced Energy Output: Lower calorific value means more coal is needed to produce the same amount of energy, increasing fuel consumption.
-
Environmental and Sustainability Considerations
- Pollution Control: Measuring ash content helps identify and mitigate the release of harmful pollutants during combustion.
- Resource Management: Efficient use of coal with lower ash content reduces the demand for mining and transportation, contributing to sustainability.
- Waste Utilization: Ash can be repurposed in construction materials (e.g., cement) or land reclamation projects, reducing its environmental impact.
By determining ash content, industries can make informed decisions about coal selection, optimize combustion processes, and minimize environmental and economic impacts. This analysis is essential for ensuring the efficient and sustainable use of coal as an energy resource.
Summary Table:
Key Aspect | Details |
---|---|
Ash Content Definition | Inorganic residue left after coal combustion, composed of minerals. |
Importance | - Affects combustion efficiency, economic value, and environmental impact. |
Measurement Methods | - Proximate Analysis: Measures residue. - Elemental Analysis: Details composition. |
Applications | - Coal grading, process optimization, and regulatory compliance. |
Challenges | - Increased waste disposal, higher operational costs, reduced energy output. |
Sustainability | - Pollution control, resource management, and waste utilization. |
Optimize your coal usage and reduce costs—contact our experts today for tailored solutions!