Argon is a critical component in steelmaking due to its inert properties, which make it ideal for creating a non-reactive atmosphere during various stages of the process. Its primary use is in the Argon Oxygen Decarburization (AOD) process, where it helps refine liquid metal by controlling oxygen and carbon levels, removing impurities like hydrogen and nitrogen, and minimizing chromium losses. Argon also aids in the reduction and desulfurization stages, ensuring the production of high-quality steel. While its cost is a drawback, its ability to enhance steel quality and efficiency makes it indispensable in modern steel manufacturing.
Key Points Explained:
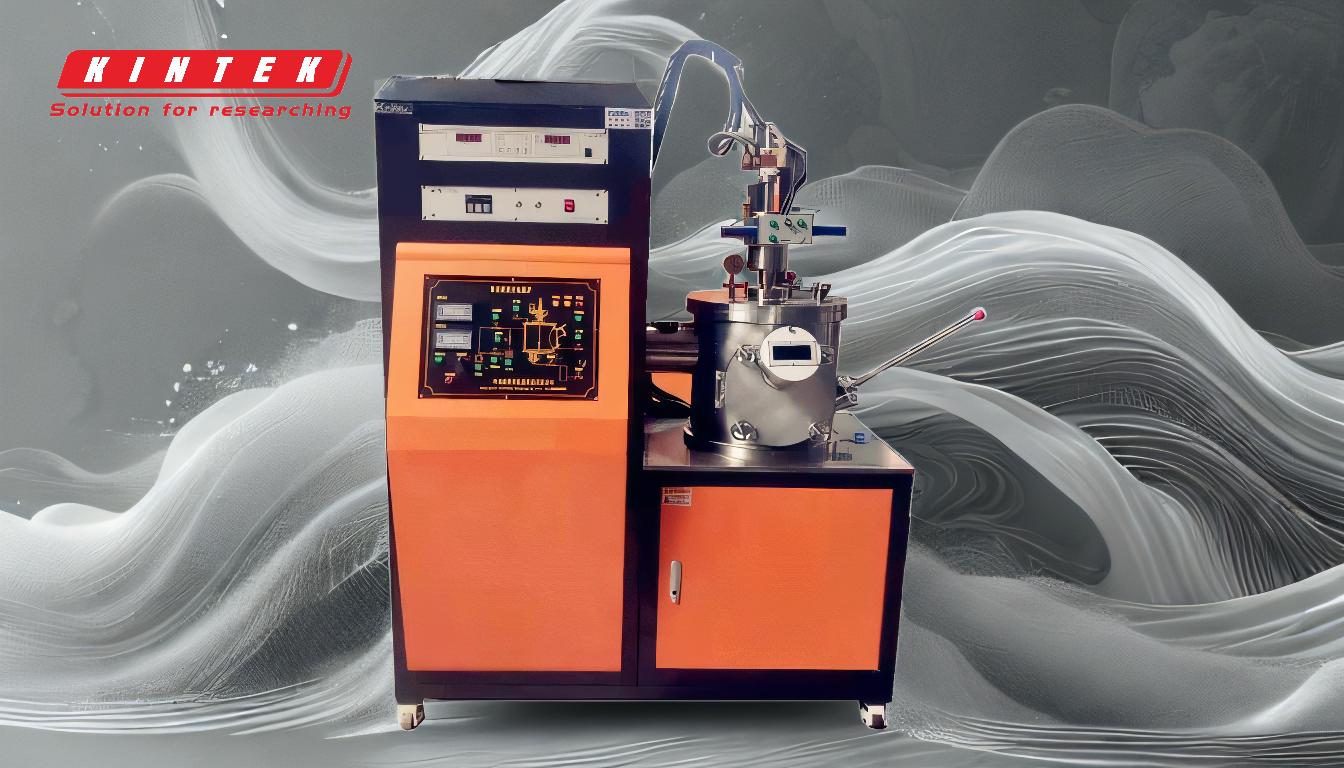
-
Inert Nature of Argon:
- Argon is an inert gas, meaning it does not react with metal surfaces or other elements during the steelmaking process. This property makes it ideal for creating a stable, non-reactive environment, which is crucial for maintaining the integrity and quality of the steel.
-
Argon Oxygen Decarburization (AOD) Process:
- The AOD process is a key application of argon in steelmaking. It involves three stages: decarburization, reduction, and desulfurization.
- Decarburization: During this stage, an argon-oxygen gas mixture is injected into the liquid metal. Argon helps lower the partial pressure of oxygen and carbon monoxide, allowing for controlled oxidation of carbon and other impurities without excessive loss of alloying elements like chromium.
- Reduction and Desulfurization: In these stages, argon aids in mixing and removing unwanted elements such as hydrogen and nitrogen. Alloys, lime, and fluorspar are added to manage slag, a by-product that is later removed. This ensures the final steel product has low sulfur content and high purity.
- The AOD process is a key application of argon in steelmaking. It involves three stages: decarburization, reduction, and desulfurization.
-
Control of Impurities:
- Argon plays a vital role in removing impurities like hydrogen and nitrogen from the molten steel. These elements can weaken the steel and cause defects if not properly managed. By creating a controlled atmosphere, argon ensures these impurities are effectively removed, resulting in higher-quality steel.
-
Minimization of Chromium Losses:
- Chromium is a valuable alloying element that enhances the corrosion resistance and strength of steel. Argon helps minimize chromium losses during the AOD process by reducing the oxidation of chromium, ensuring that more of it remains in the final product.
-
Slag Management:
- Argon aids in the formation and management of slag, a by-product of the steelmaking process. Slag is used in various applications, such as concrete or road production. By improving slag formation and removal, argon contributes to the efficiency and sustainability of the steelmaking process.
-
Cost Considerations:
- While argon is more expensive than some other gases, its benefits in terms of steel quality and process efficiency often justify the cost. The use of argon in steelmaking is a trade-off between cost and the need for high-quality, impurity-free steel.
-
Other Applications in Manufacturing:
- Beyond steelmaking, argon is also used in other manufacturing processes, such as welding and casting, where it serves as a shielding gas to protect metals from oxidation. Its inert properties make it suitable for use in specialty alloys and titanium production, further highlighting its versatility in industrial applications.
In summary, argon's inert nature, ability to control impurities, and role in minimizing chromium losses make it an essential component in modern steelmaking. While its cost is a consideration, the benefits it provides in terms of steel quality and process efficiency make it a valuable resource in the industry.
Summary Table:
Key Role of Argon in Steelmaking | Benefits |
---|---|
Inert Nature | Creates a non-reactive atmosphere, ensuring steel integrity. |
AOD Process | Refines liquid metal by controlling oxygen and carbon levels. |
Impurity Control | Removes hydrogen and nitrogen, enhancing steel quality. |
Chromium Retention | Minimizes chromium losses during refining. |
Slag Management | Improves slag formation and removal for efficiency. |
Cost vs. Quality | Justifies higher cost with superior steel quality and efficiency. |
Other Applications | Used in welding, casting, and specialty alloy production. |
Discover how argon can optimize your steelmaking process—contact our experts today!