Ceramic materials are widely used in furnace construction due to their exceptional thermal, mechanical, and chemical properties. They are fire-resistant, lightweight, and energy-efficient, making them superior to traditional materials like brick. Ceramic fibers, in particular, provide excellent thermal insulation, ensuring uniform temperatures and safe external surface temperatures. Their low thermal conductivity and density allow for lightweight kiln designs, while their resistance to thermal shock and mechanical vibrations ensures durability. Additionally, ceramics adapt well to rapid heating and cooling cycles, making them ideal for high-temperature applications. These properties collectively make ceramics a preferred choice for modern furnace construction.
Key Points Explained:
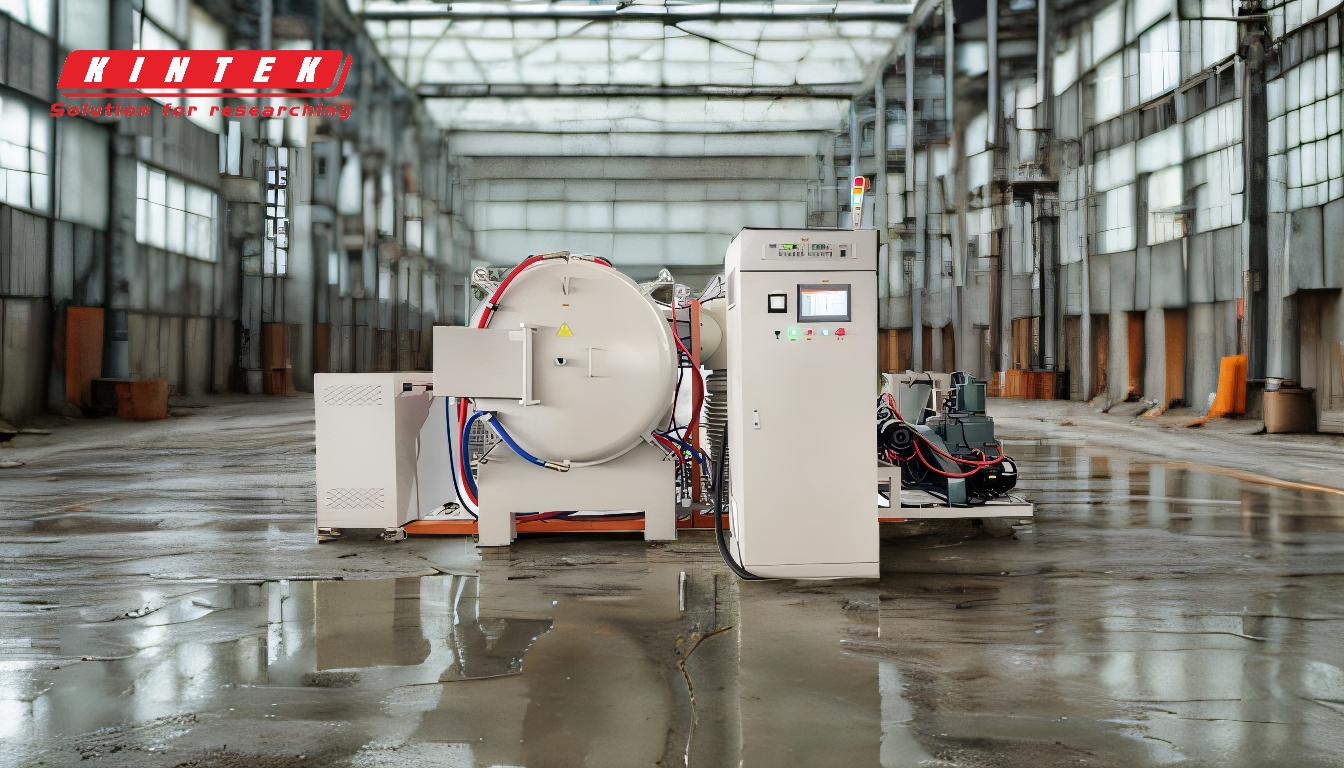
-
Fire Resistance:
- Ceramics are inherently fire-resistant, making them ideal for furnace construction. They can withstand extremely high temperatures without degrading, ensuring the furnace operates safely and efficiently.
- This property is crucial for maintaining structural integrity and preventing fire hazards in high-temperature environments.
-
Lightweight Nature:
- Ceramic fibers are lightweight compared to traditional materials like brick. This reduces the overall weight of the furnace, allowing for the use of lighter steel frames in construction.
- The lightweight nature also simplifies transportation and installation, making ceramic-based furnaces more practical and cost-effective.
-
Energy Efficiency:
- Ceramic materials have low thermal conductivity, meaning they are excellent insulators. This reduces heat loss, making the furnace more energy-efficient.
- The energy-saving aspect is particularly beneficial in industrial applications where energy costs are a significant concern.
-
Thermal Insulation:
- Ceramic fibers provide superior thermal insulation, ensuring uniform and controlled temperatures inside the furnace chamber. This is essential for processes that require precise temperature regulation.
- The insulation properties also help maintain safe external surface temperatures, protecting operators and surrounding equipment.
-
Resistance to Thermal Shock:
- Ceramics can withstand rapid and repeated heating and cooling cycles without cracking or degrading. This makes them ideal for applications that involve frequent temperature changes.
- Their ability to handle thermal shock ensures long-term durability and reduces maintenance costs.
-
Mechanical and Chemical Stability:
- Ceramic materials are resistant to mechanical vibrations and impacts, which is important in industrial environments where equipment is subject to constant movement and stress.
- They also exhibit good chemical stability, meaning they do not react with or degrade when exposed to various chemicals, further enhancing their durability.
-
Flexibility in Design:
- The adaptability of ceramic fibers allows for greater flexibility in furnace design. This enables manufacturers to create customized solutions tailored to specific industrial needs.
- The design flexibility also facilitates the integration of advanced features and technologies, improving overall furnace performance.
-
Time-Saving:
- The lightweight and easy-to-install nature of ceramic materials reduce construction time, allowing for quicker setup and commissioning of furnaces.
- This time-saving aspect is particularly valuable in industries where downtime can lead to significant financial losses.
In summary, the use of ceramics in furnace construction offers a combination of fire resistance, lightweight design, energy efficiency, superior thermal insulation, and durability. These properties make ceramics an ideal material for modern furnaces, ensuring safe, efficient, and reliable operation in high-temperature industrial applications.
Summary Table:
Property | Benefits |
---|---|
Fire Resistance | Withstands high temperatures, ensuring safety and structural integrity. |
Lightweight Nature | Reduces furnace weight, simplifies transportation, and lowers costs. |
Energy Efficiency | Low thermal conductivity minimizes heat loss, saving energy. |
Thermal Insulation | Ensures uniform temperatures and safe external surfaces. |
Resistance to Thermal Shock | Handles rapid heating/cooling cycles without cracking. |
Mechanical Stability | Resists vibrations and impacts, ideal for industrial environments. |
Chemical Stability | Does not degrade when exposed to chemicals, enhancing durability. |
Design Flexibility | Enables customized furnace solutions for specific industrial needs. |
Time-Saving | Quick installation reduces downtime and speeds up furnace commissioning. |
Ready to upgrade your furnace with ceramic materials? Contact our experts today for tailored solutions!