Hydrogen is used in vacuum annealing furnaces primarily because of its unique properties as a reducing agent and its ability to create a controlled atmosphere that prevents oxidation and scaling during the annealing process. Hydrogen ensures a clean, oxide-free surface, which reduces the need for additional post-processing steps. It is particularly effective for annealing low carbon steels, stainless steels, and other materials like tungsten crucible and advanced ceramics components. However, its use requires careful control, as hydrogen can cause decarburization or hydrogen embrittlement in certain materials, especially at high temperatures. The purity of hydrogen, its ability to act as a deoxidizer, and its role in creating a protective atmosphere make it indispensable in high-temperature annealing processes.
Key Points Explained:
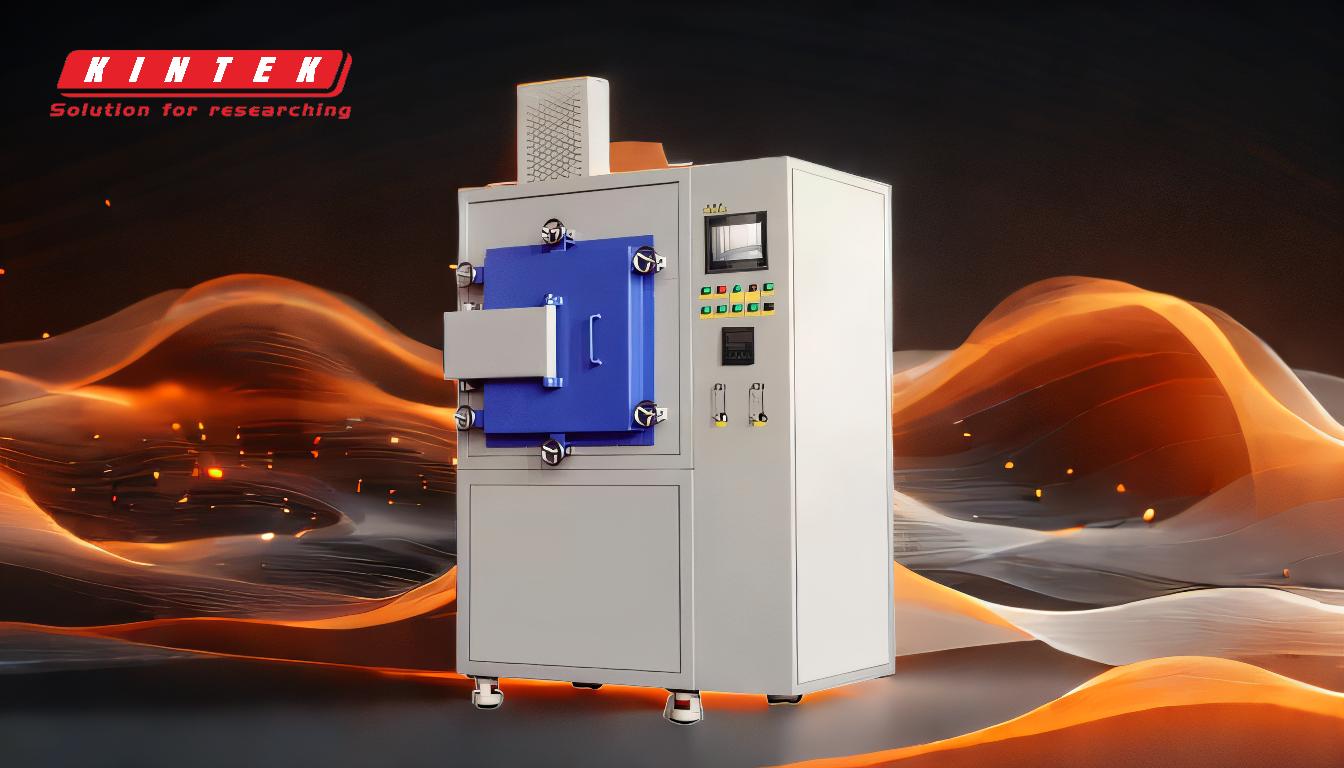
-
Hydrogen as a Reducing Agent:
- Hydrogen prevents oxidation and scaling of materials during annealing by acting as a reducing agent. This ensures that the surface of the material remains clean and oxide-free, which is critical for achieving high-quality results.
- Example: In the annealing of stainless steels, hydrogen helps maintain the material's corrosion resistance by preventing the formation of oxides on the surface.
-
Controlled Atmosphere for Annealing:
- Hydrogen is used to create a controlled atmosphere in annealing furnaces, either in pure form or as a mixture with nitrogen (forming gas). This atmosphere protects the material from reacting with oxygen or other contaminants during the heating process.
- Example: A hydrogen content greater than 5% in forming gas is sufficient to provide a protective environment for annealing processes.
-
Purity and Impurities in Commercial Hydrogen:
- Commercial hydrogen is typically 98-99.9% pure, with traces of water vapor, oxygen, nitrogen, carbon dioxide, and methane. These impurities can affect the annealing process, so the moisture content must be carefully controlled.
- Example: Dry hydrogen is preferred for sintering tungsten carbide to avoid unwanted reactions caused by moisture.
-
Decarburization and Hydrogen Embrittlement:
- At high temperatures, hydrogen can decarburize high carbon materials, leading to the formation of methane. This can weaken the material and is a critical consideration in processes involving high carbon steels.
- Hydrogen embrittlement is another risk, particularly in high carbon substances, where hydrogen atoms can diffuse into the material and cause brittleness.
- Example: In the annealing of high carbon steels, careful temperature and atmosphere control are required to avoid these issues.
-
Applications in Various Industries:
- Hydrogen annealing furnaces are used for a wide range of applications, including sintering tungsten carbide, annealing low carbon and stainless steels, and processing ceramic and magnetic materials.
- Example: In the semiconductor industry, hydrogen is used for alloy processing and brazing, where a clean, oxide-free surface is essential.
-
Operational Characteristics of Hydrogen Annealing Furnaces:
- These furnaces offer precise temperature control (±1℃) and uniformity (±3℃ to ±10℃), making them suitable for a variety of annealing processes.
- They can store multiple heating programs, allowing for flexibility in meeting different process requirements.
- Example: A furnace with a maximum temperature of 1600℃ can handle high-temperature annealing and sintering processes for refractory metals.
-
Advantages Over Other Atmospheres:
- Hydrogen provides a cleaner and more effective reducing atmosphere compared to other gases like nitrogen or argon. This reduces the need for additional cleaning or surface treatment after annealing.
- Example: In the direct reduction of metal ores, hydrogen is preferred for its ability to remove oxygen from the ore efficiently.
-
Challenges and Limitations:
- While hydrogen is highly effective, its use requires careful handling due to its flammability and potential safety risks.
- The risk of hydrogen embrittlement and decarburization limits its use in certain high carbon materials unless proper precautions are taken.
- Example: In the annealing of high carbon steels, alternative atmospheres or post-treatment processes may be required to mitigate these risks.
By leveraging hydrogen's unique properties, annealing furnaces can achieve superior results in terms of surface quality and material properties. However, the process must be carefully managed to avoid potential drawbacks such as decarburization and hydrogen embrittlement.
Summary Table:
Key Aspect | Details |
---|---|
Reducing Agent | Prevents oxidation and scaling, ensuring clean, oxide-free surfaces. |
Controlled Atmosphere | Protects materials from contaminants; used in pure form or with nitrogen. |
Purity & Impurities | 98-99.9% pure; moisture control is critical to avoid unwanted reactions. |
Decarburization & Embrittlement | Risks include methane formation and material brittleness at high temps. |
Applications | Used for stainless steels, tungsten carbide, ceramics, and semiconductors. |
Operational Characteristics | Precise temp control (±1℃), uniformity (±3℃ to ±10℃), and program storage. |
Advantages | Cleaner reducing atmosphere; reduces post-processing needs. |
Challenges | Flammability, embrittlement, and decarburization risks require careful use. |
Discover how hydrogen annealing furnaces can optimize your processes—contact us today for expert advice!