Stainless steel is challenging to braze due to its dense oxide layer, which, while preventing oxidation, also hinders the wetting and bonding of the filler metal. To achieve effective brazing, this oxide layer must be removed through strict cleaning processes. Brazing can be performed using methods such as flame, induction, or furnace heating, with vacuum brazing being particularly effective. The process involves preparation, assembly with filler metal, and post-brazing inspection to ensure high-quality joints.
Key Points Explained:
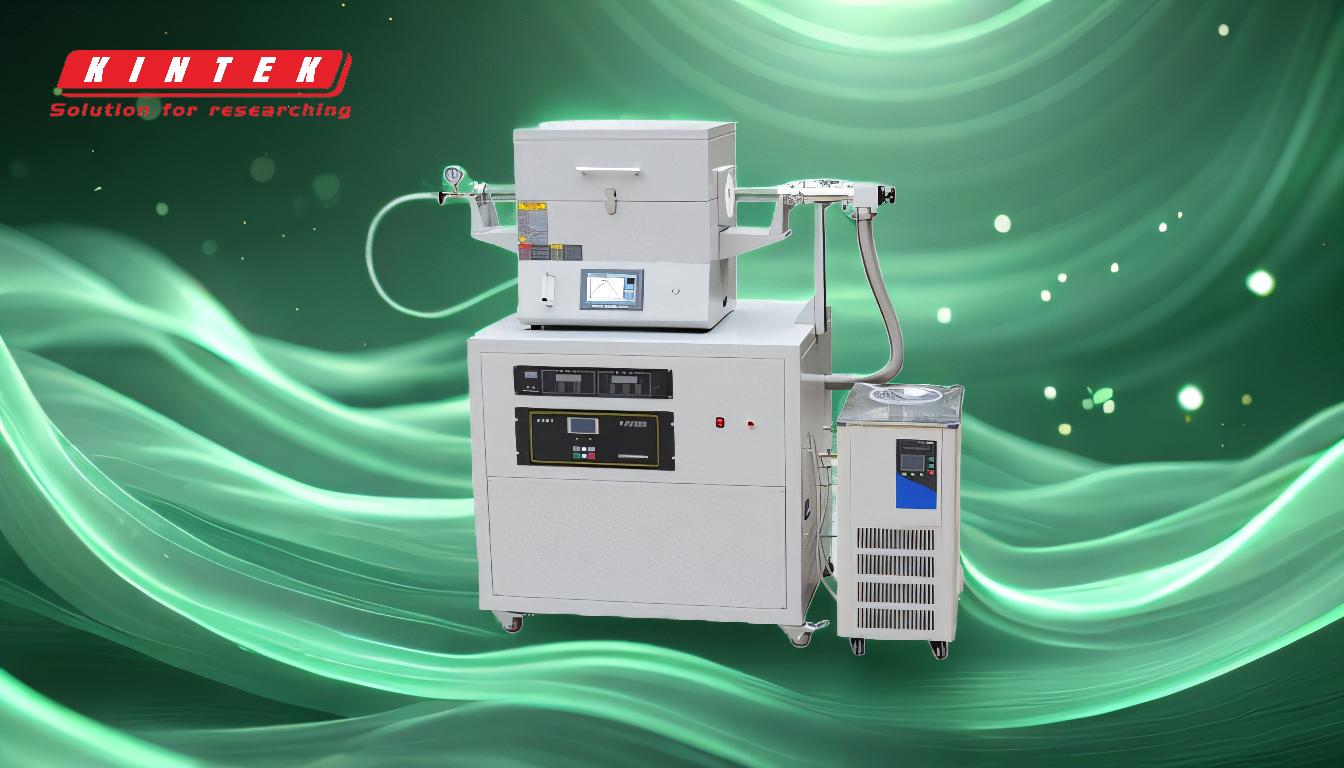
-
Dense Oxide Layer on Stainless Steel:
- Stainless steel naturally forms a dense oxide layer that protects it from corrosion and oxidation. However, this layer also acts as a barrier during brazing, preventing the filler metal from wetting and bonding effectively with the base material.
- To achieve a strong and reliable joint, this oxide layer must be removed before brazing. This is typically done through chemical cleaning, mechanical abrasion, or by using a controlled atmosphere like vacuum brazing.
-
Importance of Cleaning Before Brazing:
- Before brazing, stainless steel must undergo stringent cleaning to remove contaminants such as grease, oil films, and other residues. These contaminants can interfere with the brazing process and compromise joint quality.
- Cleaning methods include degreasing with solvents, ultrasonic cleaning, or abrasive techniques. After cleaning, brazing should be performed immediately to prevent reformation of the oxide layer.
-
Brazing Methods for Stainless Steel:
- Stainless steel can be brazed using various heating methods, including flame, induction, and furnace heating. Each method has its advantages depending on the application and required precision.
- Vacuum brazing is particularly effective for stainless steel because it eliminates the need for flux and prevents oxidation during the process. This method ensures a clean and high-quality joint.
-
Vacuum Brazing Process:
- The vacuum brazing process for stainless steel involves three main steps:
- Preparation: Cleaning the stainless steel surfaces and ensuring proper alignment of the parts to be joined.
- Assembly and Filler Metal Application: Placing the filler metal in the joint and assembling the components. The filler metal is chosen based on its compatibility with stainless steel and the desired joint properties.
- Inspection: After the brazing process, the joint is inspected for defects, such as voids, cracks, or incomplete bonding, to ensure it meets quality standards.
- The vacuum brazing process for stainless steel involves three main steps:
-
Challenges and Solutions in Brazing Stainless Steel:
- The primary challenge in brazing stainless steel is overcoming the oxide layer and ensuring proper wetting of the filler metal. This can be addressed by using appropriate cleaning techniques and controlled atmospheres like vacuum brazing.
- Another challenge is selecting the right filler metal, which must have a lower melting point than stainless steel and good compatibility with it. Common filler metals include silver-based alloys and nickel-based alloys.
By understanding these key points, equipment and consumable purchasers can make informed decisions about the materials and processes required for successful stainless steel brazing.
Summary Table:
Key Aspect | Details |
---|---|
Dense Oxide Layer | Prevents wetting and bonding; must be removed for effective brazing. |
Cleaning Process | Degreasing, ultrasonic cleaning, or abrasion to remove contaminants. |
Brazing Methods | Flame, induction, furnace heating, or vacuum brazing for optimal results. |
Vacuum Brazing Steps | Preparation, assembly with filler metal, and post-brazing inspection. |
Filler Metal Selection | Silver-based or nickel-based alloys with lower melting points. |
Need expert advice on stainless steel brazing? Contact us today for tailored solutions!