Physical Vapor Deposition (PVD) is a widely used technique in materials science and engineering to deposit thin films of material onto a substrate. The process involves the vaporization of a solid material in a vacuum environment, which then condenses onto the substrate to form a thin film. The vacuum environment is crucial for several reasons, including controlling the vapor pressure, ensuring the purity of the deposition, and enabling the formation of a uniform and adherent film. Below, we will explore why a vacuum is necessary in PVD processes.
Key Points Explained:
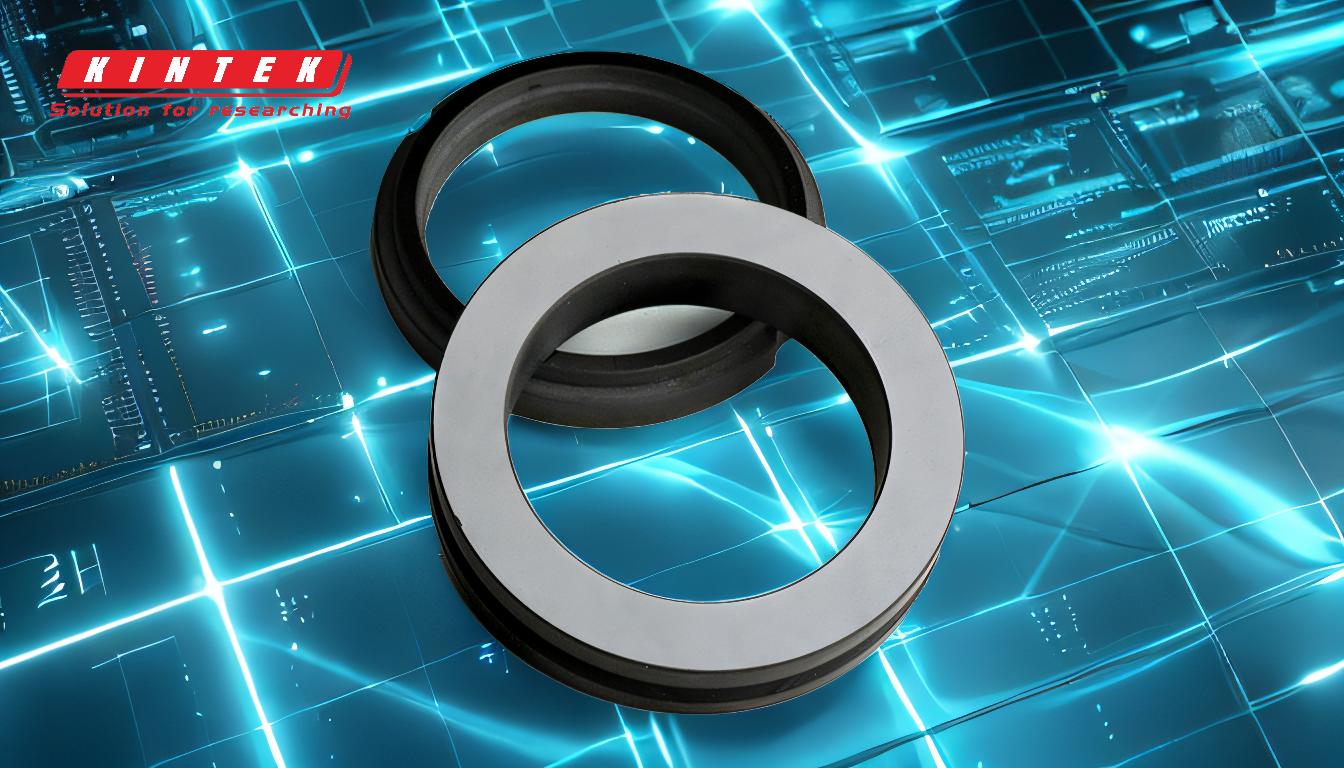
-
Control of Vapor Pressure:
- In PVD, the material to be deposited is typically vaporized through methods such as sputtering or evaporation. The vapor pressure of a material is the pressure exerted by its vapor when it is in equilibrium with its solid or liquid phase at a given temperature. In a vacuum environment, the vapor pressure can be precisely controlled by adjusting the temperature and pressure conditions. This control is essential because it determines the rate at which the material vaporizes and subsequently condenses onto the substrate. Without a vacuum, the vapor pressure would be influenced by atmospheric pressure, making it difficult to achieve consistent and controlled deposition rates.
-
Prevention of Contamination:
- A vacuum environment significantly reduces the presence of contaminants such as oxygen, nitrogen, and water vapor, which can react with the deposition material or the substrate. These contaminants can lead to the formation of oxides, nitrides, or other undesirable compounds that can degrade the quality of the deposited film. By maintaining a high vacuum, the likelihood of such reactions is minimized, ensuring that the deposited film is pure and adheres well to the substrate.
-
Uniform Film Deposition:
- The vacuum environment in PVD processes allows for the uniform distribution of the vaporized material across the substrate. In the absence of a vacuum, the vaporized particles would collide with gas molecules in the air, leading to scattering and uneven deposition. The vacuum ensures that the vaporized particles travel in straight lines from the source to the substrate, resulting in a more uniform and consistent film thickness. This uniformity is critical for applications where precise control over film properties, such as thickness and composition, is required.
-
Reduction of Particle Collisions:
- In a vacuum, the mean free path of the vaporized particles (the average distance a particle travels before colliding with another particle) is significantly increased. This means that the vaporized particles can travel from the source to the substrate without being deflected or scattered by collisions with gas molecules. This direct path ensures that the particles arrive at the substrate with sufficient energy to adhere properly, leading to a more adherent and dense film. In contrast, in a non-vacuum environment, frequent collisions with gas molecules would reduce the energy of the particles, resulting in a less adherent and more porous film.
-
Enhanced Film Properties:
- The vacuum environment not only improves the uniformity and purity of the deposited film but also enhances its mechanical, electrical, and optical properties. For example, films deposited in a vacuum tend to have better adhesion, higher density, and fewer defects compared to those deposited in the presence of air. These improved properties are essential for applications in electronics, optics, and coatings, where the performance of the film is directly related to its quality.
In summary, the vacuum environment in Physical Vapor Deposition (PVD) is essential for controlling vapor pressure, preventing contamination, ensuring uniform film deposition, reducing particle collisions, and enhancing the overall properties of the deposited film. Without a vacuum, it would be challenging to achieve the high-quality, consistent, and adherent films required for advanced technological applications.
Summary Table:
Reason | Explanation |
---|---|
Control of Vapor Pressure | Ensures precise vaporization and deposition rates by adjusting temperature and pressure. |
Prevention of Contamination | Reduces contaminants like oxygen and water vapor, ensuring film purity and adhesion. |
Uniform Film Deposition | Allows vaporized particles to travel directly, creating consistent film thickness. |
Reduction of Particle Collisions | Increases mean free path for particles, enhancing adhesion and film density. |
Enhanced Film Properties | Improves mechanical, electrical, and optical properties of the deposited film. |
Want to learn more about how vacuum enhances PVD processes? Contact our experts today!