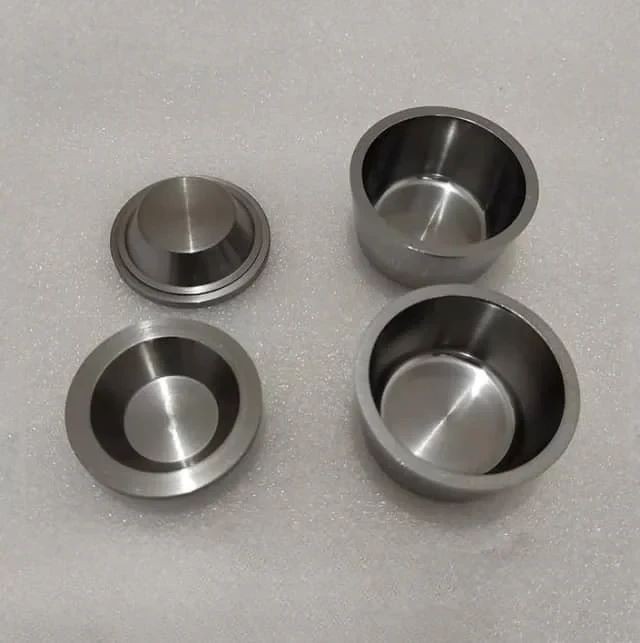
Thin Film Deposition Parts
Electron Beam Evaporation Coating Tungsten Crucible / Molybdenum Crucible
Item Number : KMS04
Price varies based on specs and customizations
- Material
- Molybdenum / Tungsten
- Specification
- 30-50mm*15-25mm
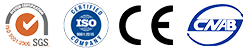
Shipping:
Contact us to get shipping details Enjoy On-time Dispatch Guarantee.
Application
Electron beam evaporation (EBE) is a physical vapor deposition (PVD) technique for thin film deposition. In EBE, a beam of high-energy electrons is used to heat and vaporize a solid material, which then condenses onto a substrate to form a thin film. Tungsten and molybdenum crucibles are commonly used in electron beam evaporation processes due to their excellent thermal and mechanical properties. Tungsten/Molybdenum crucibles are commonly used for thin film deposition in the production of microelectronics, such as integrated circuits (ICs) and microprocessors; optical coating processes, to deposit thin films onto lenses, mirrors or other optical components; are thin-film depositions for anti-reflective coatings or conductive layers;Wear-resistant coatings: Tungsten crucibles can be used to deposit wear-resistant coatings on various components, such as cutting tools or engine parts, etc.
Detail & Parts
Technical specifications
Outer diameter & High | 30*15mm | 34*20mm | 35*17mm | 40*17mm | 42*19mm | 45*22mm | 50mm*22 |
The crucibles we show are available in different sizes and custom sizes are available on request.
Advantages
- Very high melting point; suitable for processing high melting point materials. High thermal conductivity for efficient heat transfer during evaporation.
- High purity; using a tungsten crucible helps ensure the purity of the deposited film.
- High mechanical strength; Tungsten is known for its excellent mechanical strength and resistance to deformation at high temperatures.
- Low Vapor Pressure; Tungsten has a low vapor pressure that helps minimize contamination and maintain a clean vacuum environment during evaporation.
FAQ
What Are Thermal Evaporation Sources?
What Are Tungsten Boats?
What Are The Advantages Of Using Tungsten Boats?
What Is Physical Vapor Deposition (PVD)?
What Are The Main Types Of Thermal Evaporation Sources?
What Is Magnetron Sputtering?
How Do Thermal Evaporation Sources Work?
Why Magnetron Sputtering?
What Are The Advantages Of Using Thermal Evaporation Sources?
What Are The Common Materials Used For Evaporating Crucibles?
What Are The Advantages Of Using Evaporation Boats?
What Are The Materials Used In Thin Film Deposition?
Thin film deposition commonly utilizes metals, oxides, and compounds as materials, each with its unique advantages and disadvantages. Metals are preferred for their durability and ease of deposition but are relatively expensive. Oxides are highly durable, can withstand high temperatures, and can be deposited at low temperatures, but can be brittle and challenging to work with. Compounds offer strength and durability, can be deposited at low temperatures and tailored to exhibit specific properties.
The selection of material for a thin film coating is dependent on the application requirements. Metals are ideal for thermal and electrical conduction, while oxides are effective in offering protection. Compounds can be tailored to suit specific needs. Ultimately, the best material for a particular project will depend on the specific needs of the application.
What Applications Are Thermal Evaporation Sources Used For?
What Are The Advantages Of Using Evaporating Crucibles?
What Is The Typical Lifespan Of An Evaporation Boat?
What Are The Methods To Achieve Optimal Thin Film Deposition?
To achieve thin films with desirable properties, high-quality sputtering targets and evaporation materials are essential. The quality of these materials can be influenced by various factors, such as purity, grain size, and surface condition.
The purity of sputtering targets or evaporation materials plays a crucial role, as impurities can cause defects in the resulting thin film. Grain size also affects the quality of the thin film, with larger grains leading to poor film properties. Additionally, the surface condition is crucial, since rough surfaces can result in defects in the film.
To attain the highest quality sputtering targets and evaporation materials, it is crucial to select materials that possess high purity, small grain size, and smooth surfaces.
Uses Of Thin Film Deposition
Zinc Oxide-Based Thin Films
ZnO thin films find applications in several industries such as thermal, optical, magnetic, and electrical, but their primary use is in coatings and semiconductor devices.
Thin-Film Resistors
Thin-film resistors are crucial for modern technology and are used in radio receivers, circuit boards, computers, radiofrequency devices, monitors, wireless routers, Bluetooth modules, and cell phone receivers.
Magnetic Thin Films
Magnetic thin films are used in electronics, data storage, radio-frequency identification, microwave devices, displays, circuit boards, and optoelectronics as key components.
Optical Thin Films
Optical coatings and optoelectronics are standard applications of optical thin films. Molecular beam epitaxy can produce optoelectronic thin-film devices (semiconductors), where epitaxial films are deposited one atom at a time onto the substrate.
Polymer Thin Films
Polymer thin films are used in memory chips, solar cells, and electronic devices. Chemical deposition techniques (CVD) offer precise control of polymer film coatings, including conformance and coating thickness.
Thin-Film Batteries
Thin-film batteries power electronic devices such as implantable medical devices, and the lithium-ion battery has advanced significantly thanks to the use of thin films.
Thin-Film Coatings
Thin-film coatings enhance the chemical and mechanical characteristics of target materials in various industries and technological fields. Anti-reflective coatings, anti-ultraviolet or anti-infrared coatings, anti-scratch coatings, and lens polarization are some common examples.
Thin-Film Solar Cells
Thin-film solar cells are essential to the solar energy industry, enabling the production of relatively cheap and clean electricity. Photovoltaic systems and thermal energy are the two main applicable technologies.
How Should Evaporating Crucibles Be Handled And Maintained?
Can Evaporation Boats Be Reused?
Factors And Parameters That Influence Deposition Of Thin Films
Deposition Rate:
The rate at which the film is produced, typically measured in thickness divided by time, is crucial for selecting a technology suitable for the application. Moderate deposition rates are sufficient for thin films, while quick deposition rates are necessary for thick films. It is important to strike a balance between speed and precise film thickness control.
Uniformity:
The consistency of the film across the substrate is known as uniformity, which usually refers to film thickness but can also relate to other properties such as the index of refraction. It is important to have a good understanding of the application to avoid under- or over-specifying uniformity.
Fill Capability:
Fill capability or step coverage refers to how well the deposition process covers the substrate's topography. The deposition method used (e.g., CVD, PVD, IBD, or ALD) has a significant impact on step coverage and fill.
Film Characteristics:
The characteristics of the film depend on the application's requirements, which can be categorized as photonic, optical, electronic, mechanical, or chemical. Most films must meet requirements in more than one category.
Process Temperature:
Film characteristics are significantly affected by process temperature, which may be limited by the application.
Damage:
Each deposition technology has the potential to damage the material being deposited upon, with smaller features being more susceptible to process damage. Pollution, UV radiation, and ion bombardment are among the potential sources of damage. It is crucial to understand the limitations of the materials and tools.
How Do You Select The Appropriate Evaporation Boat Material?
4.8
out of
5
Electron beam evaporation coating made simple and efficient with Kintek Solution's tools.
4.9
out of
5
Kintek Solution's crucibles have taken our manufacturing process to the next level. The quality and durability are second to none.
4.7
out of
5
The expertise of Kintek Solution in electron beam evaporation coating is evident in their outstanding products.
4.8
out of
5
Kintek Solution's crucibles have revolutionized our thin film deposition process, delivering exceptional results.
4.7
out of
5
Kintek Solution has set a new standard for electron beam evaporation coating. Their products are a testament to their commitment to quality.
4.9
out of
5
Kintek Solution's crucibles have accelerated our manufacturing process, enabling us to meet increasing demands efficiently.
4.6
out of
5
Kintek Solution's electron beam evaporation coating solution has transformed our manufacturing process, delivering exceptional results.
4.7
out of
5
Kintek Solution's crucibles have exceeded our expectations, providing superior outcomes in our electron beam evaporation process.
4.8
out of
5
Kintek Solution's electron beam evaporation coating products are a game-changer, delivering precision and reliability.
PDF - Electron Beam Evaporation Coating Tungsten Crucible / Molybdenum Crucible
disabled = false, 3000)"> DownloadCatalog of Thin Film Deposition Parts
disabled = false, 3000)"> DownloadCatalog of Thermal Evaporation Sources
disabled = false, 3000)"> DownloadCatalog of Evaporation Crucible
disabled = false, 3000)"> DownloadCatalog of Tungsten Boat
disabled = false, 3000)"> DownloadCatalog of Evaporation Boat
disabled = false, 3000)"> DownloadCatalog of Thin Film Deposition Materials
disabled = false, 3000)"> DownloadREQUEST A QUOTE
Our professional team will reply to you within one business day. Please feel free to contact us!
Related Products
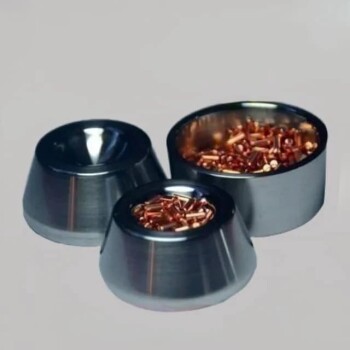
Electron Beam Evaporation Coating / Gold Plating / Tungsten Crucible / Molybdenum Crucible
These crucibles act as containers for the gold material evaporated by the electron evaporation beam while precisely directing the electron beam for precise deposition.
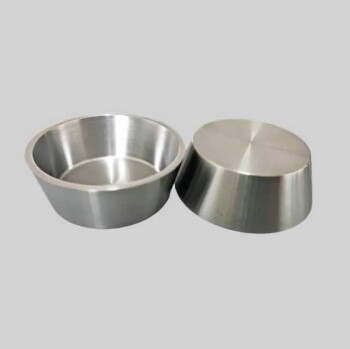
In the context of electron gun beam evaporation, a crucible is a container or source holder used to contain and evaporate the material to be deposited onto a substrate.
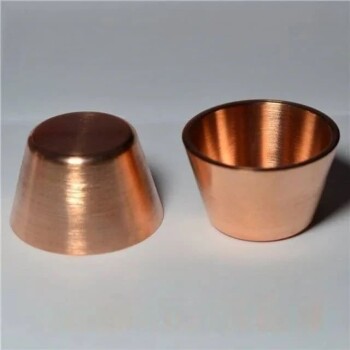
Electron Beam Evaporation Coating Oxygen-Free Copper Crucible
Electron Beam Evaporation Coating Oxygen-Free Copper Crucible enables precise co-deposition of various materials. Its controlled temperature and water-cooled design ensure pure and efficient thin film deposition.
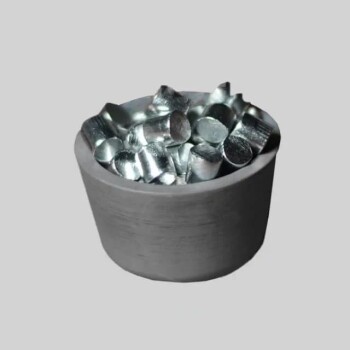
Electron Beam Evaporation Coating Conductive Boron Nitride Crucible (BN Crucible)
High-purity and smooth conductive boron nitride crucible for electron beam evaporation coating, with high temperature and thermal cycling performance.
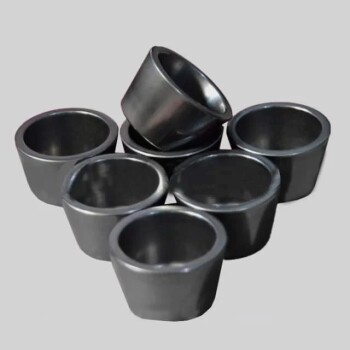
Electron Beam Evaporation Graphite Crucible
A technology mainly used in the field of power electronics. It is a graphite film made of carbon source material by material deposition using electron beam technology.
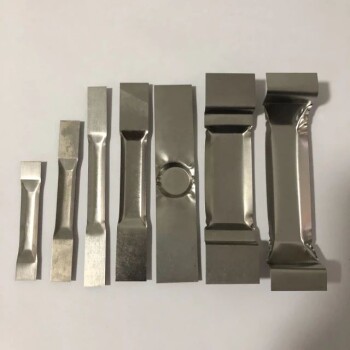
Learn about tungsten boats, also known as evaporated or coated tungsten boats. With a high tungsten content of 99.95%, these boats are ideal for high-temperature environments and widely used in various industries. Discover their properties and applications here.
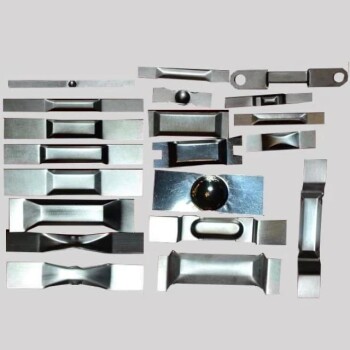
Molybdenum/tungsten/tantalum evaporation boat - special shape
Tungsten Evaporation Boat is ideal for vacuum coating industry and sintering furnace or vacuum annealing. we offers tungsten evaporation boats that are designed to be durable and robust, with long operating lifetimes and to ensure consistent smooth and even spreading of the molten metals.
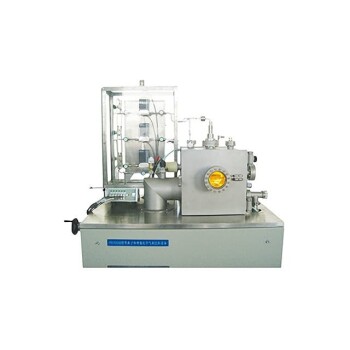
Plasma enhanced evaporation deposition PECVD coating machine
Upgrade your coating process with PECVD coating equipment. Ideal for LED, power semiconductors, MEMS and more. Deposits high-quality solid films at low temps.
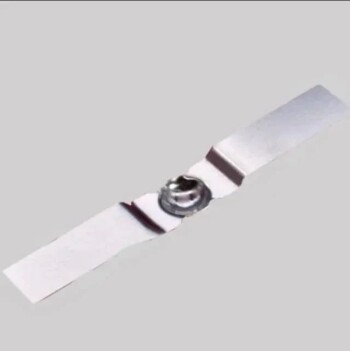
Hemispherical Bottom Tungsten / Molybdenum Evaporation Boat
Used for gold plating, silver plating, platinum, palladium, suitable for a small amount of thin film materials. Reduce the waste of film materials and reduce heat dissipation.
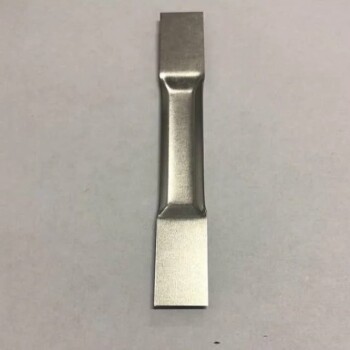
Molybdenum / Tungsten / Tantalum Evaporation Boat
Evaporation boat sources are used in thermal evaporation systems and are suitable for depositing various metals, alloys and materials. Evaporation boat sources are available in different thicknesses of tungsten, tantalum and molybdenum to ensure compatibility with a variety of power sources. As a container, it is used for vacuum evaporation of materials. They can be used for thin film deposition of various materials, or designed to be compatible with techniques such as electron beam fabrication.
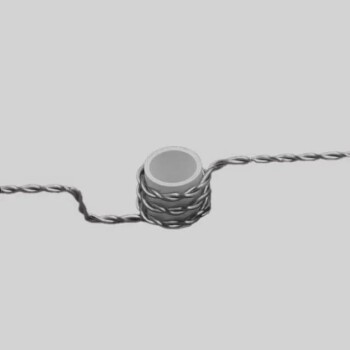
It can be used for vapor deposition of various metals and alloys. Most metals can be evaporated completely without loss. Evaporation baskets are reusable.1
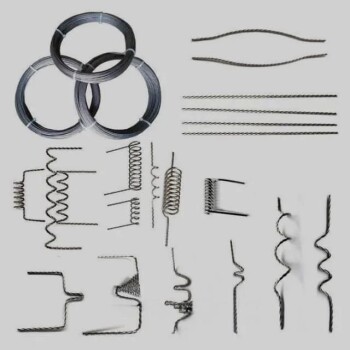
Thermally evaporated tungsten wire
It has a high melting point, thermal and electrical conductivity, and corrosion resistance. It is a valuable material for high temperature, vacuum and other industries.
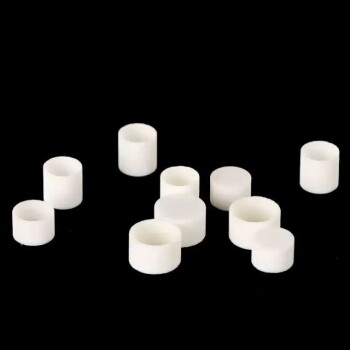
Alumina Crucibles (Al2O3) Covered Thermal Analysis / TGA / DTA
TGA/DTA thermal analysis vessels are made of aluminum oxide (corundum or aluminum oxide). It can withstand high temperature and is suitable for analyzing materials that require high temperature testing.
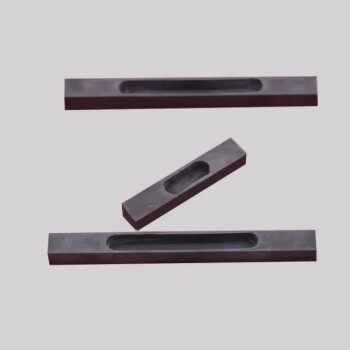
Vessels for high temperature applications, where materials are kept at extremely high temperatures to evaporate, allowing thin films to be deposited on substrates.
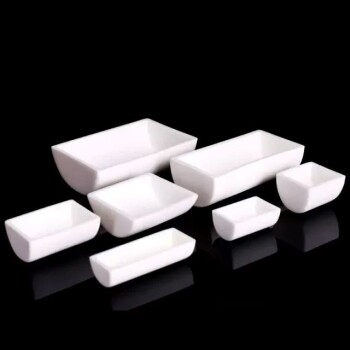
Alumina (Al2O3) Ceramic Crucible Semicircle Boat with Lid
Crucibles are containers widely used for melting and processing various materials, and semicircular boat-shaped crucibles are suitable for special smelting and processing requirements. Their types and uses vary by material and shape.
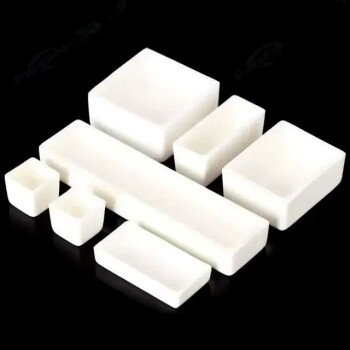
Alumina (Al2O3) Ceramic Crucible For Laboratory Muffle Furnace
Alumina ceramic crucibles are used in some materials and metal melting tools, and flat-bottomed crucibles are suitable for melting and processing larger batches of materials with better stability and uniformity.
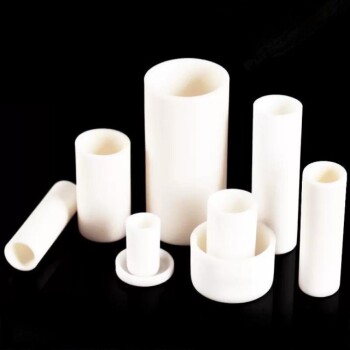
Alumina (Al2O3) Crucible With Lid Cylindrical Laboratory Crucible
Cylindrical Crucibles Cylindrical crucibles are one of the most common crucible shapes, suitable for melting and processing a wide variety of materials, and are easy to handle and clean.
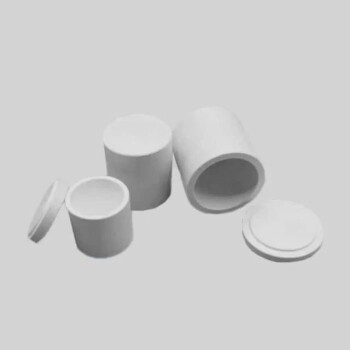
Evaporation Crucible for Organic Matter
An evaporation crucible for organic matter, referred to as an evaporation crucible, is a container for evaporating organic solvents in a laboratory environment.
Related Articles
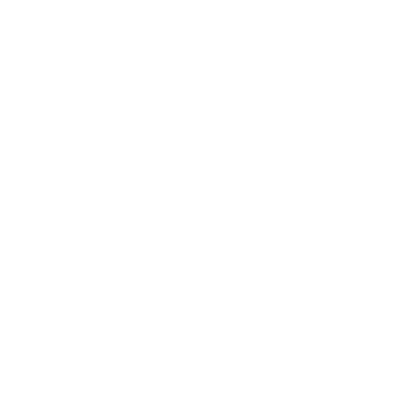
Exploring the Benefits of Using Tungsten for Furnace Heating
Tungsten has a number of properties that make it well-suited for use in high-temperature furnaces.
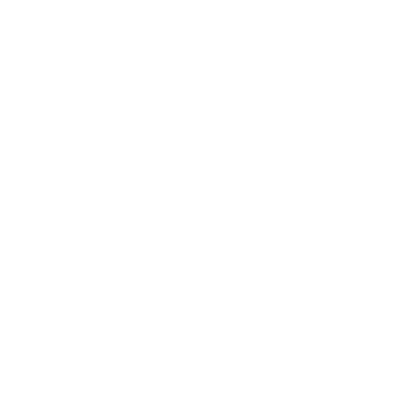
A Comparative Study of Evaporation and Sputtering Techniques in Thin Film Deposition
The two most common techniques used for thin film deposition are evaporation and sputtering.
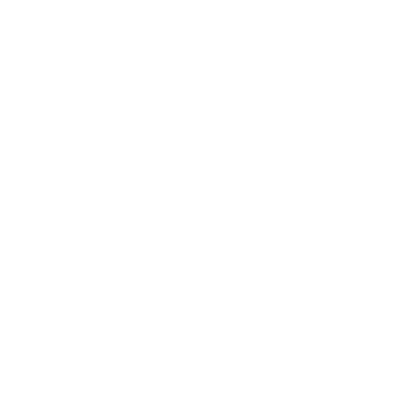
Electron Beam Evaporation Coating Technology and Material Selection
An in-depth look at the principles and applications of electron beam evaporation coating technology, including material selection and various fields of application.
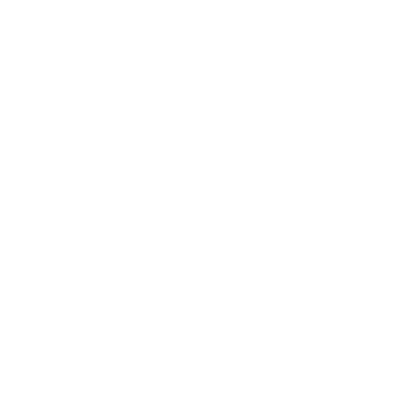
Understanding Warm Isostatic Press: An Essential Tool in Electronics Manufacture
Warm Isostatic Press (WIP) equipment, also known as Warm Isostatic Laminator, is a cutting-edge technology that combines isostatic pressing with a heating element. It utilizes warm water or a similar medium to apply uniform pressure to powdered products from all directions. The process involves shaping and pressing the powder material using flexible materials as a jacket mold and hydraulic pressure as a pressure medium.
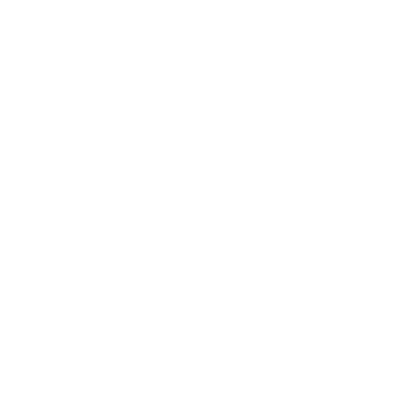
Electron Beam Evaporation Technology in Vacuum Coating
An in-depth look at electron beam evaporation, its types, advantages, and disadvantages in vacuum coating processes.
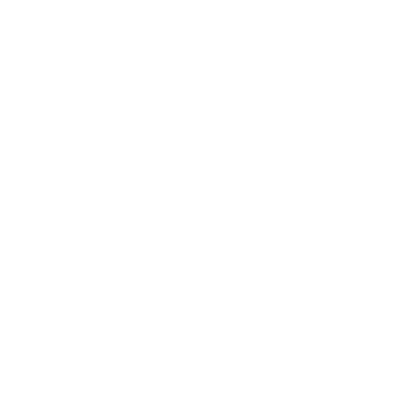
Electron Beam Evaporation Coating: Principles, Characteristics, and Applications
An in-depth analysis of electron beam evaporation coating technology, its advantages, disadvantages, and applications in thin film manufacturing.
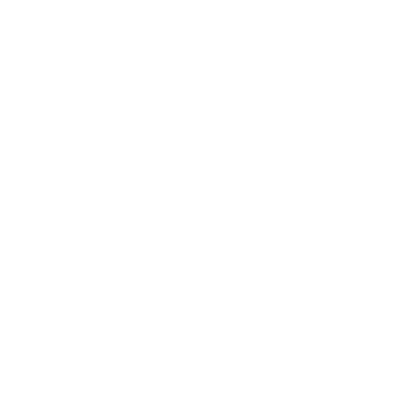
Electron Beam Evaporation Coating: Advantages, Disadvantages, and Applications
An in-depth look at the pros and cons of electron beam evaporation coating and its various applications in industries.
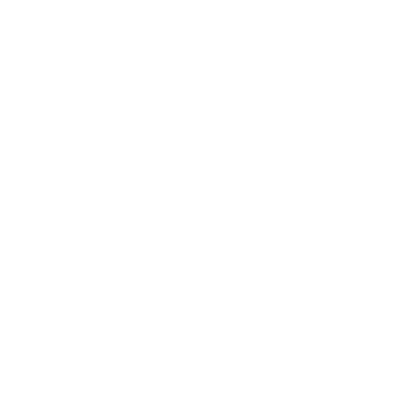
Vacuum Melting Furnace: A Comprehensive Guide to Vacuum Induction Melting
Discover the intricacies of vacuum induction melting furnaces, their components, operation, advantages, and applications. Explore how these furnaces revolutionize metal processing and achieve exceptional material properties.
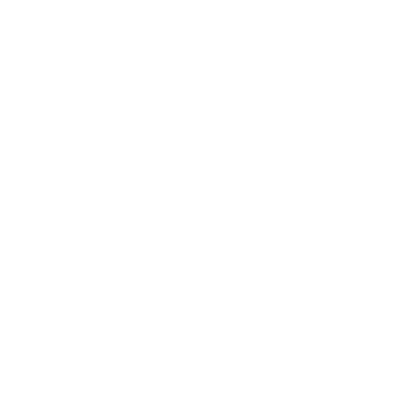
Electron Beam Evaporation: Advanced Thin Film Creation
Explores the technology and applications of electron beam evaporation in thin film production.
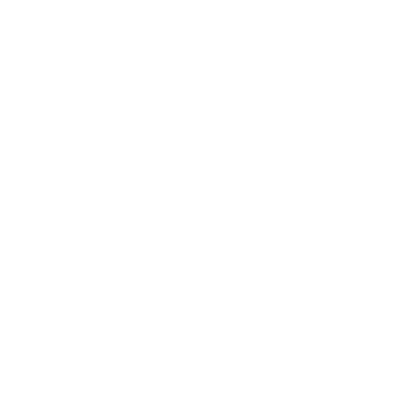
Challenges in the Development and Application of Tantalum in Vacuum Deposition Equipment
This article discusses the role of tantalum in vacuum deposition equipment, focusing on its properties, manufacturing challenges, and its critical applications in industries like OLED screen production.
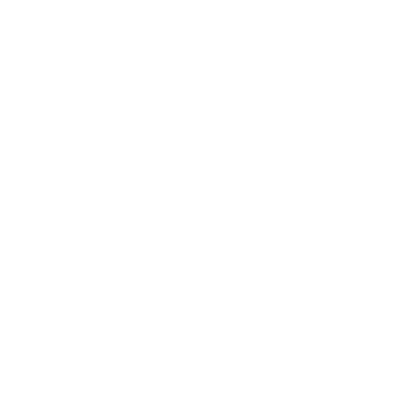
Selecting Vacuum Coating Materials: Key Factors and Considerations
Guidelines on choosing the right vacuum coating materials based on application, material properties, deposition methods, economy, substrate compatibility, and safety.
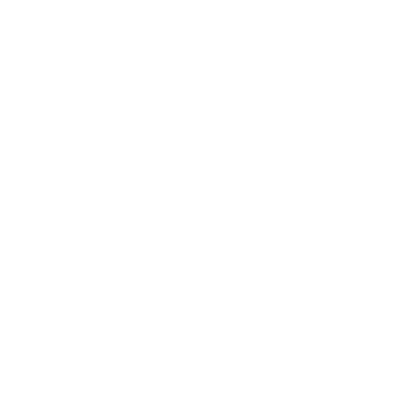
Comprehensive Overview of Vacuum Evaporation Systems
An in-depth look at vacuum evaporation systems, their principles, components, and applications.