Overview of Cold Isostatic Pressing (CIP) and Hot Isostatic Pressing (HIP)
Table of Contents
- Overview of Cold Isostatic Pressing (CIP) and Hot Isostatic Pressing (HIP)
- Detailed Process of Cold Isostatic Pressing (CIP)
- Detailed Process of Hot Isostatic Pressing (HIP)
- Applications of Hot Isostatic Pressing (HIP)
- Advantages of Isostatic Pressing
- Absence of wall friction
- Uniform grain structure and density regardless of shape
- Shape flexibility
- Component size
- Low tooling cost
- Enhance alloying possibilities
- Reduced lead times
- Material and machining costs
- Advantages of Isostatic Press
- Application of Isostatic Press
- Advantages and Disadvantages of Isostatic Press
- 6 KEY ADVANTAGES OF COLD ISOSTATIC PRESSING VERSUS UNIAXIAL PRESSING
- Working of Isostatic Press
- Process of Producing a PM Component using HIP
- Conclusion
Cold Isostatic Pressing (CIP) and Hot Isostatic Pressing (HIP) are two powder metallurgy techniques used to produce dense and high-quality metal components.
Cold Isostatic Pressing (CIP)
In CIP, metal powder is placed inside a flexible mould made of rubber, urethane, or PVC. The assembly is then pressurized hydrostatically in a chamber, usually using water, with pressures ranging from 400 to 1000MPa. The powder gets compacted, and the green compact is taken out and sintered.
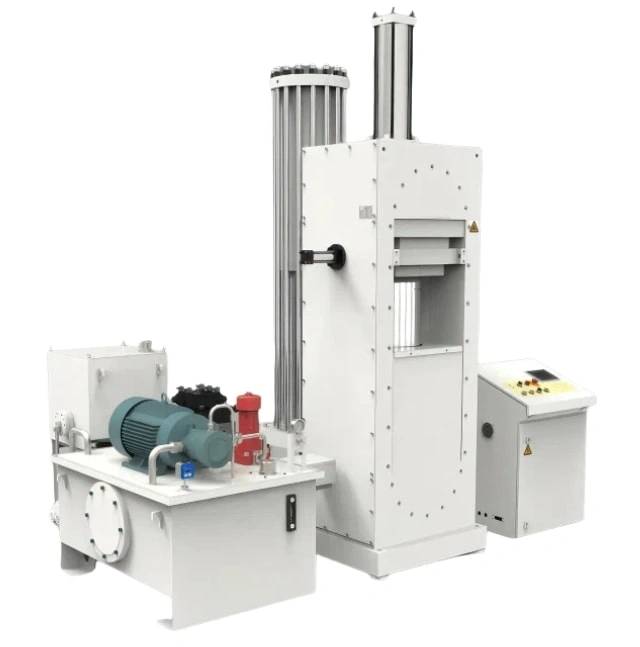
Hot Isostatic Pressing (HIP)
Hot Isostatic Pressing (HIP) takes the process a step further by combining high pressure with elevated temperatures. This method subjects a material to simultaneous high pressure and high temperature within a high-pressure chamber. HIP is used to densify materials, eliminate defects, and enhance properties through diffusion and consolidation. It's especially valuable for materials requiring improved structural integrity, reduced porosity, and higher mechanical properties.
Cold Isostatic Pressing vs. Hot Isostatic Pressing: A Comparative Overview
In the realm of materials processing, Cold Isostatic Pressing (CIP) and Hot Isostatic Pressing (HIP) are two powerful techniques that offer unique advantages. Here's a comparative overview of the two methods:
Cold Isostatic Pressing (CIP)
- Involves subjecting a material to uniform pressure from all sides using a high-pressure fluid medium and hydraulic pressure.
- Effective for shaping and consolidating powdered materials, creating intricate shapes and achieving high green density.
Hot Isostatic Pressing (HIP)
- Combines high pressure with elevated temperatures within a high-pressure chamber.
- Used to densify materials, eliminate defects, and enhance properties through diffusion and consolidation.
- Creates high-performance materials with superior mechanical properties and structural integrity.
Hot isostatic press
Key Differences
- Pressure and Temperature: CIP involves cold compaction using isostatic pressure, while HIP employs both high pressure and high temperature to achieve densification and enhanced properties.
- Applications: CIP is often used for shaping and initial consolidation of powdered materials, while HIP is favored for creating high-performance materials with superior mechanical properties and structural integrity.
Detailed Process of Cold Isostatic Pressing (CIP)
Preparation of the metal powder and mould
Cold isostatic pressing (CIP) is a method of compacting powdered materials into a solid homogeneous mass before machining or sintering. It involves compacting powders by enclosing them in an elastomer mold. An elastomer mold is used because it has low resistance to deformation. Liquid pressure is then applied uniformly to the mold to compress it.
Pressurization process
The pressurization process in cold isostatic pressing is based on Pascal's law, which states that pressure applied in an enclosed fluid is transmitted in all directions throughout the fluid without any change in magnitude. The mold is placed in a pressure chamber, and a liquid medium is pumped in. The mold is uniformly subjected to high pressure from all sides. This process helps to reduce distortion, improve accuracy, and reduce the risk of air entrapment and voids.
Compaction of the powder
During the cold isostatic pressing process, the powder is compacted to a very uniform density. This results in a highly compact solid that is ready for further processing such as machining or sintering. The good green strength obtained with this forming method allows for premachining before sintering without causing breakage.
The sintering process
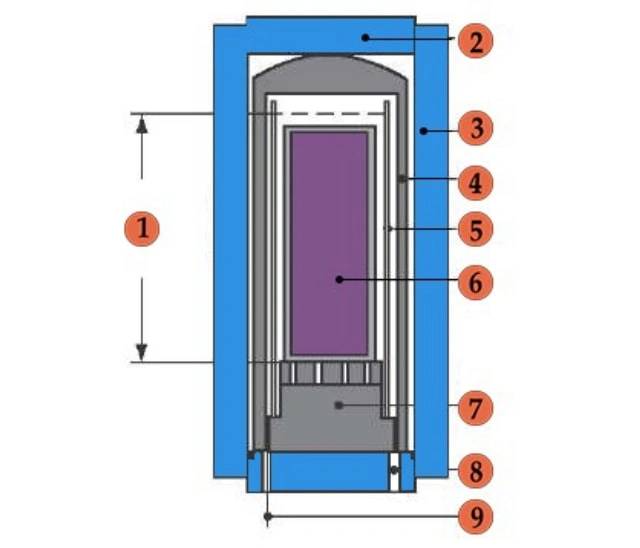
After the cold isostatic pressing process, the compacted powder is usually sintered conventionally to produce the desired part. Sintering involves heating the compacted powder to a high temperature, below its melting point, to cause bonding between the particles. This helps to further strengthen the part and improve its mechanical properties.
Conclusion
Cold isostatic pressing (CIP) is a valuable method for compacting powdered materials into solid homogeneous masses. It offers advantages such as high-integrity billets or preforms with little distortion or cracking, and the ability to process materials that are too large for uniaxial presses. The process involves the preparation of the metal powder and mold, the pressurization process based on Pascal's law, the compaction of the powder, and the sintering process. CIP is widely used in various industries, including plastics, graphite, powdered metallurgy, ceramics, and sputtering targets.
Detailed Process of Hot Isostatic Pressing (HIP)
Hot Isostatic Pressing (HIP) is a material processing method that involves the simultaneous application of heat and high pressure to materials. It is used to improve the characteristics of additive manufactured products by removing porosity and improving the microstructure, resulting in enhanced mechanical properties.
Preparation of the metal powder and container
Before the HIP process begins, the metal powder and container need to be prepared. The metal powder is typically made from alloys such as titanium, steels, aluminum, copper, and magnesium. The container needs to be gas tight to ensure that the process can be carried out in a gaseous atmosphere.
Pressurization and high temperature process
Once the metal powder and container are prepared, the HIP process can begin. The metal powder is placed inside the container, which is then sealed. The container is then subjected to high pressure, usually using an inert gas such as argon. At the same time, the temperature is elevated to several hundreds to 2000 °C. The combination of high pressure and high temperature allows for plastic deformation, creep, and diffusion to occur.
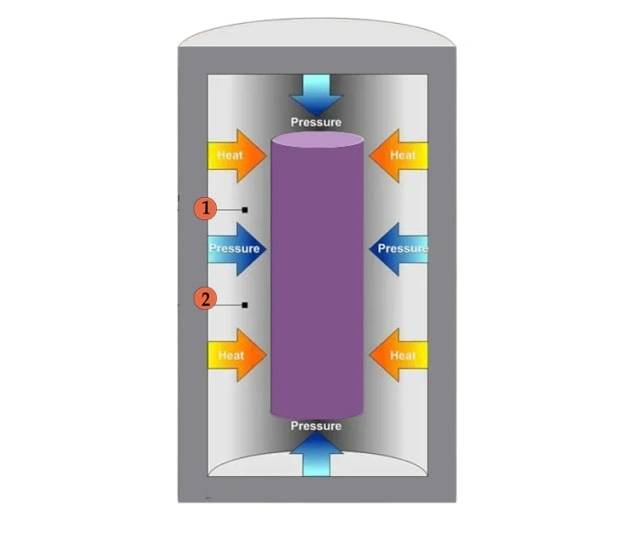
The role of inert gas
The inert gas, such as argon, plays a crucial role in the HIP process. It provides the pressure needed to compress the materials and ensures that the pressure is applied uniformly in all directions. The inert gas also helps to create a gaseous atmosphere for the process to take place.
Sintering of the compacted powder
During the HIP process, the metal powder is compacted under high pressure and high temperature. This results in the elimination of internal voids or porosity and the improvement of the microstructure. The compacted powder becomes a solid with a homogeneous annealed microstructure, making it suitable for various applications.
Hot Isostatic Pressing (HIP) is a versatile process that has been used for more than 50 years. It is commonly used in industries such as aerospace, energy, and manufacturing. The process allows for the production of components with improved material properties and near-net shape parts.
Overall, Hot Isostatic Pressing (HIP) is an effective method for enhancing the properties of materials through the application of heat and pressure. It is widely used in various industries and offers numerous benefits, including the elimination of porosity and the improvement of mechanical properties.
Applications of Hot Isostatic Pressing (HIP)
Hot Isostatic Pressing (HIP) is a versatile technology that finds applications in various industries. Let's explore some of the key applications of HIP:
Production of super alloy components for the aerospace industry
HIP is widely used in the production of super alloy components for the aerospace industry. Super alloys are known for their excellent strength and corrosion resistance, making them ideal for aerospace applications. The HIP process helps eliminate internal voids and porosity in the super alloy components, resulting in improved mechanical properties and overall performance.
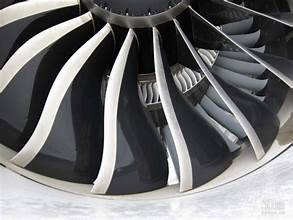
Densification of WC cutting tools and PM tool steels
Hot Isostatic Pressing is also utilized in the densification of WC (tungsten carbide) cutting tools and powder metallurgy (PM) tool steels. By subjecting these materials to high temperature and pressure, the HIP process helps achieve a fully dense and homogeneous microstructure, enhancing the performance and durability of cutting tools and tool steels.
Improvement of properties in superalloy and Ti alloy castings
HIP plays a crucial role in improving the properties of superalloy and titanium alloy castings. Castings for critical applications often have internal microporosity that can compromise their mechanical properties. The HIP process helps eliminate these defects by applying high pressure and temperature, resulting in densification and improved mechanical properties of the castings.
In addition to these specific applications, Hot Isostatic Pressing is also used more broadly in industries such as powder metallurgy, sintering, and metal matrix composites. The technology enables the production of fully dense and high-performance components with improved material properties.
Overall, Hot Isostatic Pressing (HIP) is a powerful manufacturing technique that offers numerous benefits in terms of densification, elimination of defects, and improvement of material properties. Its applications range from aerospace components to cutting tools and castings, making it a valuable process in various industries.
Advantages of Isostatic Pressing
Absence of wall friction
Isostatic pressing eliminates the need for lubricants, resulting in a high and uniform density that can be achieved without any warpage or distortion during sintering or hot isostatic pressing. The absence of wall friction allows for consistent compaction in all directions.
Uniform grain structure and density regardless of shape
Isostatic pressing offers shape flexibility, making it practical to produce complex shapes and dimensions that are difficult or impossible to achieve with other methods. This process ensures uniform density and grain structure, regardless of the shape of the component.
Shape flexibility
Isostatic pressing enables the production of shapes and dimensions that are challenging to achieve with other manufacturing methods. It allows for the fabrication of complex shapes, making it suitable for a wide range of component sizes.
Component size
Isostatic pressing can be used to produce a wide range of component sizes, from massive 30-ton near-net PM shapes to smaller, densified less than 100-gram MIM parts. The size of the parts is only limited by the size of the isostatic pressure chamber.
Low tooling cost
Compared to other manufacturing methods, isostatic pressing offers low tooling costs for short production runs. This makes it economically viable for producing complex shapes from prototype to production quantities.
Enhance alloying possibilities
Isostatic pressing allows for the enhancement of alloying elements in the material without inducing segregation. This opens up possibilities for creating materials with improved properties and performance.
Reduced lead times
Isostatic pressing significantly reduces lead times for the production of complex shapes. It offers shorter lead times compared to traditional methods such as forgings or machined components.
Material and machining costs
By producing near-net shape parts, isostatic pressing helps reduce material waste and machining costs. The process can fabricate components with high precision, minimizing the need for additional machining.
Advantages of Isostatic Press
Isostatic pressing compacted the powder with the same pressure in all directions, leading to high and uniform density without the need for lubricants. This process removes constraints on part geometry that exist in rigid die compaction methods. It is particularly suitable for difficult-to-compact and expensive materials such as superalloys, titanium, tool steels, stainless steel, and beryllium.
Application of Isostatic Press
Isostatic pressing finds applications in various industries, including pharmaceuticals, explosives, chemicals, food, nuclear fuel, and ferrites. It is a versatile manufacturing process that can be used for a wide range of materials and products.
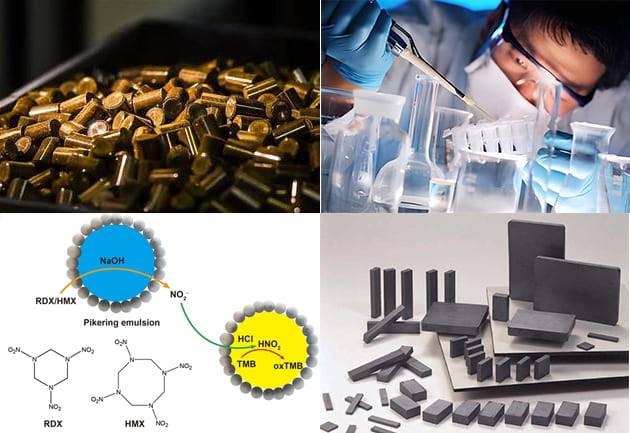
Advantages and Disadvantages of Isostatic Press
Isostatic pressing is chosen for achieving high compact densities and accessing shapes that cannot be compacted using uniaxial presses. Complex shapes can be engineered into the elastomeric molds, offering flexibility in design. However, the wet bag variation is better suited for larger parts, while the dry bag process offers higher automation and production rates. The tooling cost and process complexity are higher for isostatic pressing compared to uniaxial pressing.
6 KEY ADVANTAGES OF COLD ISOSTATIC PRESSING VERSUS UNIAXIAL PRESSING
- More uniform product properties, greater homogeneity, and precise control of finished product dimensions.
- Greater flexibility in the shape and size of the finished product.
- Longer aspect ratios possible, allowing for the production of long thin pellets.
- Improved compaction of the powder, leading to enhanced densification.
- Ability to process materials with different characteristics and shapes.
- Reduced cycle times and improved productivity.
Working of Isostatic Press
Isostatic pressing involves compacting powder mixture by applying pressure equally from all directions. The powder mixture is encapsulated using isostatic pressure, with a flexible membrane or hermetic container acting as a pressure barrier. This process reduces the porosity of the powder mixture and achieves high and uniform density without the need for lubricants.
Isostatic pressing offers advantages such as uniform density, shape flexibility, and the ability to process difficult-to-compact materials. It is a versatile manufacturing process with applications across various industries.
Process of Producing a PM Component using HIP
Use of a mold and secondary pressing media
To produce a PM component using HIP (Hot Isostatic Pressing), a mold is used. Metal powder is filled into the mold and surrounded by a secondary pressing media. This helps in achieving uniform pressure distribution during the HIP process.
Application of vacuum and placement in an autoclave chamber
After filling the mold with metal powder, vacuum is applied to remove any trapped air or gases. The entire assembly, including the mold and powder, is then placed in an autoclave chamber. This chamber provides a controlled environment for the HIP process.
Application of pressure and temperature
Once inside the autoclave chamber, the necessary pressure is applied. The pressure is typically achieved by using inert gas, such as Argon, which is evenly distributed throughout the chamber. Along with pressure, a specific temperature is maintained to optimize the sintering process.
Sintering of the compacted metal powder
Under the applied pressure and temperature, the compacted metal powder undergoes a process called sintering. Sintering is the bonding of particles in the powder to form a solid mass. This results in the consolidation and densification of the metal powder, forming the desired PM component.
Extraction of the finished part
After the sintering process is completed, the HIP unit is cooled down, and the finished part is extracted from the mold. The part is now fully consolidated, with improved mechanical properties and reduced porosity.
Hot Isostatic Pressing (HIP) is a valuable manufacturing technique that can be used for producing complex, near-net shape metal components. It is particularly useful for small production runs of special parts, including those used in the aerospace industry. HIP can also be used as a secondary operation to eliminate porosity and improve the mechanical properties of parts manufactured by other methods.
The HIP process involves the use of elevated temperatures and high pressure to form, densify, or bond raw materials or preformed components. It utilizes a pressure vessel and an inert gas as the pressure-transmitting media. The parts are loaded into the vessel, pressurization occurs simultaneously with heating, and then the parts are cooled and removed from the vessel.
In recent years, HIP has become a high-performance, high-quality, and cost-effective process for the production of metal components. It offers advantages such as improved material properties, elimination of internal voids and microporosity, and the ability to produce intricate geometries and thin walls.
HIPing is also being used as a post-processing technique for metal 3D printed parts. It helps in achieving full density and improved mechanical properties within the printed parts. The process involves loading the parts into a pressure vessel, heating, pressurization with an inert gas, and holding at a specified temperature and pressure. This helps in eliminating porosity and improving the overall quality of the 3D printed parts.
Overall, the HIP process is a valuable tool in the production of PM components. It allows for the consolidation and densification of metal powder, resulting in finished parts with improved properties. Whether used as a primary manufacturing method or as a secondary operation, HIP offers numerous benefits for the production of high-quality metal components.
Conclusion
In conclusion, Cold Isostatic Pressing (CIP) and Hot Isostatic Pressing (HIP) are essential processes in powder metallurgy. CIP involves the pressurization and compaction of metal powder, followed by sintering, while HIP includes high temperature and pressurization processes with the use of inert gas. These techniques have a wide range of applications, such as the production of components for the aerospace industry and the improvement of properties in castings. The advantages of isostatic pressing include the absence of wall friction and the ability to achieve uniform grain structure and density regardless of shape. Overall, CIP and HIP play a crucial role in the manufacturing of high-quality PM components.
CONTACT US FOR A FREE CONSULTATION
KINTEK LAB SOLUTION's products and services have been recognized by customers around the world. Our staff will be happy to assist with any inquiry you might have. Contact us for a free consultation and talk to a product specialist to find the most suitable solution for your application needs!