Introduction
Table of Contents
Cold Isostatic Pressing (CIP) is a versatile manufacturing process that is widely used in various industries. It involves applying equal pressure from all directions to a material in order to achieve uniform compaction. This process is especially beneficial for materials with complex shapes or delicate structures. CIP is also known as isostatic compaction or hydrostatic pressing. It offers several advantages over traditional pressing methods, such as the ability to form intricate shapes and the prevention of defects like porosity. In this blog post, we will explore the concept, methods, process, capabilities, and applications of Cold Isostatic Pressing. So, let's dive in and discover the world of CIP!
Concept of Cold Isostatic Pressing (CIP)
Definition and benefits of CIP
Cold isostatic pressing (CIP) is a method of compacting powdered materials into a solid homogeneous mass before machining or sintering. It involves enclosing the powder in an elastomer mold and applying uniform liquid pressure to compress it. This process is based on Pascal's law, which states that pressure applied in an enclosed fluid is transmitted in all directions without any change in magnitude.
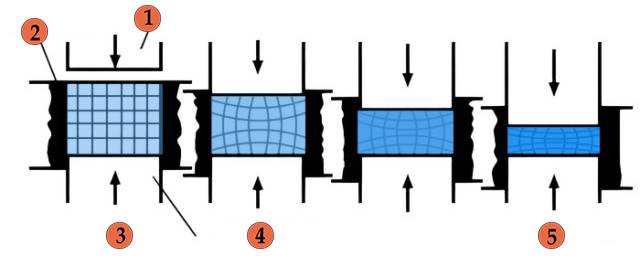
CIP has several benefits, including:
- High-integrity billets or preforms: CIP can produce solid materials with little distortion or cracking when fired, resulting in high-quality finished products.
- Suitable for large parts: CIP is commonly used for parts that are too large to be pressed in uniaxial presses.
- Versatile: CIP can be used for various materials, including plastics, graphite, powdered metallurgy, ceramics, and sputtering targets.
- Improved pressure control: Electrical CIP systems can deliver better pressure control compared to manual CIP.
Alternative name for CIP
CIP is sometimes referred to as hydrostatic pressing. This term is used interchangeably with CIP, as both processes involve applying pressure uniformly from all sides to compact the powdered materials.
Methods of Isostatic Pressing
Isostatic pressing is a powder processing technique that utilizes fluid pressure to compact the part. There are two common methods of isostatic pressing: wet-bag isostatic pressing and dry-bag isostatic pressing.
Wet-bag isostatic pressing
Wet bag isostatic pressing involves placing the powder into a forming mold, also known as the casing, and sealing it. The sealed mold is then immersed in a high-pressure cylinder for pressing. During the pressing process, the mold is completely submerged in a liquid, making direct contact with the pressure transmission medium.
Wet bag isostatic pressing offers strong applicability and is particularly suitable for experimental research and small batch production. It has the capability to simultaneously press multiple different shapes of parts in one high-pressure cylinder, allowing for the production of large and complex parts. Moreover, the production process is short and cost-effective.
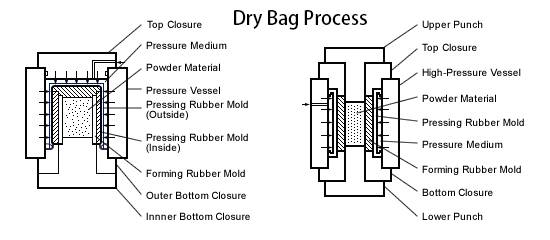
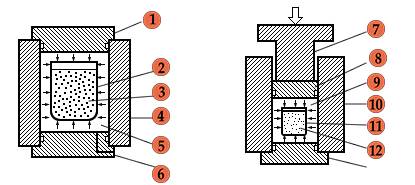
Dry-bag isostatic pressing
Dry-bag isostatic pressing, on the other hand, involves the integration of the mold into the pressure vessel itself. The powder is added to the mold, sealed, and then pressure is applied. Once the pressing is complete, the part is ejected.
The dry-bag isostatic pressing process lends itself well to automation, making it suitable for pressing relatively long runs of compacts at high production rates. This method eliminates the need for the separate immersion step required in wet-bag isostatic pressing, simplifying the overall process.
Both wet-bag and dry-bag isostatic pressing are forms of cold isostatic pressing, which is a method of compacting powdered materials into a solid homogeneous mass before machining or sintering. This process is capable of producing high-integrity billets or preforms with minimal distortion or cracking when fired. The choice between wet-bag and dry-bag methods depends on factors such as production volume, complexity of parts, and automation requirements.
Isostatic pressing, in general, offers unique advantages for ceramic and refractory applications. It applies a uniform, equal force over the entire product, regardless of its shape or size. This enables the formation of product shapes with precise tolerances, reducing the need for costly machining and driving the commercial development of isostatic pressing.
Overall, isostatic pressing is a versatile powder processing technique that finds applications in various industries, including ceramics, metals, composites, plastics, and carbon. Its ability to provide uniform compaction and precise shaping makes it an attractive option for manufacturing high-quality parts.
Process of Cold Isostatic Pressing
Use of ceramic and metal powder
Cold isostatic pressing (CIP) is a technique used to form powdered materials at room temperature. It involves applying pressure to ceramic and metal powders to create "raw" parts with sufficient strength for handling and processing. The technique uses a liquid medium, such as water or oil, and a rubber or plastic encasing mold material. CIP is commonly used to provide blanks for further sintering or hot isostatic pressing processes. For ceramic powders, CIP achieves a density of about 95%, while for metals, it achieves a density of about 100%.
Role of the pressure vessel
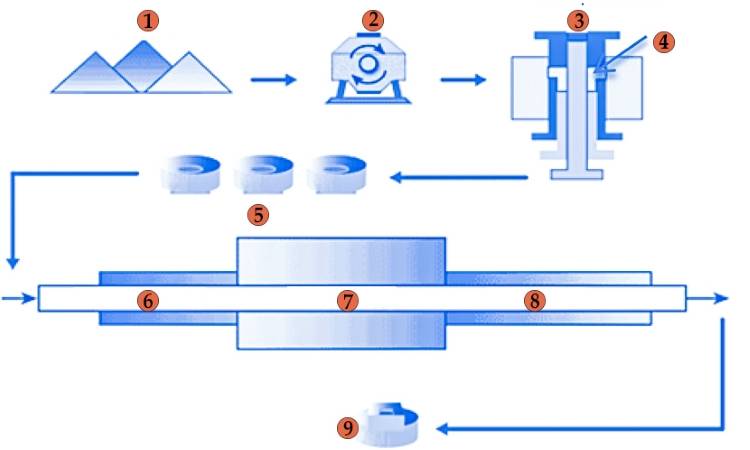
The pressure vessel plays a crucial role in the cold isostatic pressing process. It is responsible for applying the necessary pressure to the powder. The pressure vessel can withstand pressures ranging from 100 to 600 MPa. By subjecting the powder to high pressure, the pressure vessel helps in obtaining a compacted part with sufficient strength for subsequent processing.
Maximum water pressure for compression
In cold isostatic pressing, water is commonly used as the pressure medium. The maximum water pressure for compression typically ranges from 100 to 600 MPa. This pressure is applied to the powder to achieve the desired density and strength in the compacted part. The use of water as the pressure medium allows for uniform compression of the powder, resulting in a high-quality final product.
Cold isostatic pressing is a versatile technique that can be used to produce a wide range of ceramic and metal products. Its advantages include the ability to produce complex shapes, high initial cost savings compared to other pressing methods, and the ability to handle large or complex compacts. With advancements in process capability and powder metallurgy, cold isostatic pressing is increasingly being used for the production of high-performance metal parts as well. It offers solid-state processing, uniform microstructure, shape complexity, low tooling cost, and minimal material waste, making it a viable option for various industries.
Capabilities of Isostatic Pressing
Formation of complex shapes
Isostatic pressing is a powder processing technique that allows for the formation of complex shapes that are difficult or impossible to produce by other methods. The use of fluid pressure to compact the part ensures uniform density and minimal warpage during sintering or hot isostatic pressing. This means that the resulting compacted piece will have uniform shrinkage and little to no distortion.
Isostatic pressing also offers shape flexibility, allowing for the production of a wide range of component sizes, from massive 30-ton near-net PM shapes to densifying less than 100-gram MIM parts. The size of the isostatic pressure chamber is the only limitation for part sizes.
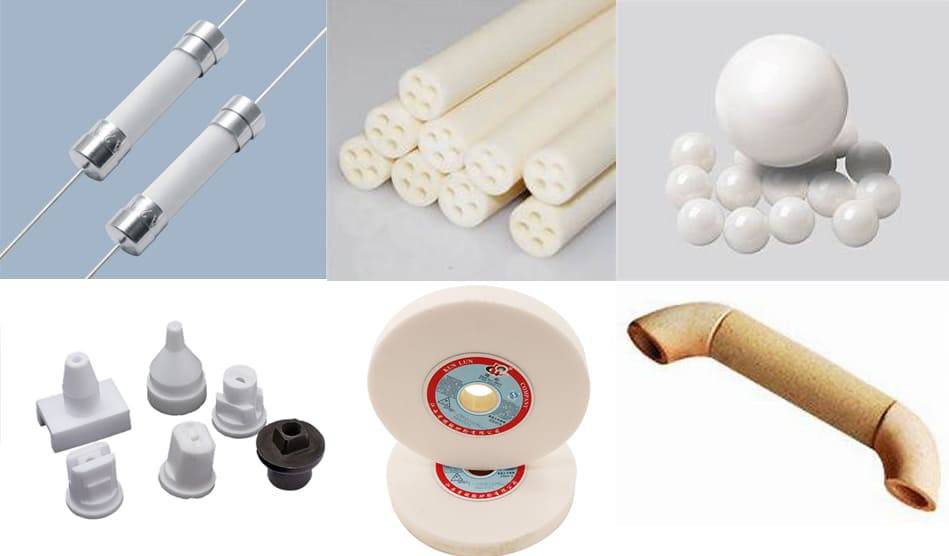
Comparison with uniaxial press or machine press
When comparing isostatic pressing to uniaxial pressing or machine pressing, there are some notable differences. Uniaxial pressing is more suitable for small shapes at high production rates. However, it may result in non-uniform densities, especially for large aspect ratios (greater than 3:1), due to die wall friction.
Isostatic pressing, on the other hand, offers more uniform product properties, greater homogeneity, and more precise control of the finished product dimensions. It is slower than uniaxial pressing but can be used for small or large, simple or complex shapes. Isostatic pressing also eliminates the need for a wax binder, reducing the production steps required.
Low-cost elastomer tooling is used for isostatic pressing, but close tolerances can only be obtained for surfaces that are pressed against a highly accurate steel mandrel. Surfaces in contact with the elastomer tooling may require post-machining for tight tolerances and good surface finishes.
In summary, isostatic pressing has the following advantages:
- Uniform density and minimal warpage
- Shape flexibility for complex shapes
- Wide range of component sizes
- Low tooling cost
- Enhanced alloying possibilities
- Reduced lead times
- Reduced material and machining costs
Isostatic pressing offers a versatile and cost-effective method for producing complex shapes with uniform properties. It is a valuable technique in various industries, including aerospace, automotive, and manufacturing.
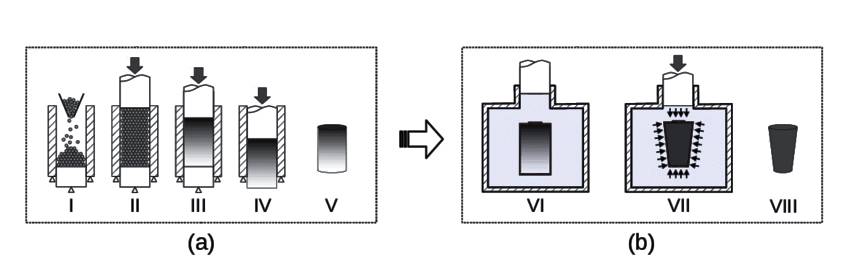
Applications of Cold Isostatic Pressing
Powder forming of various materials
Cold isostatic pressing (CIP) is a technique that applies pressure to powdered materials at room temperature or slightly higher temperatures to form "raw" parts with sufficient strength for handling and processing. This process uses a liquid medium, such as water or oil, and achieves a theoretical density of about 100% for metals and about 95% for ceramic powders.
Cold isostatic pressing is commonly used to form powdered materials at room temperature using rubber or plastic molds and liquid as the pressure medium. It is primarily used to provide blanks for further sintering or hot isostatic pressing processes. This technique allows for the production of simple-shaped small or large powder compacts with a uniform green density, even for parts with large height-to-diameter ratios. However, it may require subsequent machining in the green compact due to sacrifice in pressing speed and dimensional control.
The range of ceramic products produced by cold isostatic pressing is extensive and includes balls, tubes, rods, nozzles, fuse tubes, teeming tubes, lighting tubes, grinding wheels, sodium-sulfur battery electrolyte, spark plug insulators, sewer pipes, dinnerware, crucibles, oxygen sensors, central heating water pump shafts, and rocket nose cones. The technology is also expanding into new applications such as the compression of sputtering targets, coating of valve components, and telecommunications, electronics, aerospace, and automotive applications.
Use in food processing and medical industries
Cold isostatic pressing finds applications in the food processing and medical industries. The consolidation of ceramic powders, graphite, refractory materials, and electrical insulators is common in these industries. Materials such as silicon nitride, silicon carbide, boron nitride, boron carbide, titanium boride, and spinel are compressed using cold isostatic pressing.
In the food processing industry, cold isostatic pressing is used for applications such as the compression of sputtering targets and the coating of valve components used to reduce cylinder wear in engines. In the medical industry, it is utilized for the production of components used in telecommunications, electronics, aerospace, and automotive applications.
Other industries that apply isostatic pressing include pharmaceuticals, explosives, chemicals, and nuclear fuel Ferrites. Isostatic presses can be divided into two main types: cold isostatic presses (CIP) that function at room temperature and hot isostatic presses (HIP) that operate at elevated temperatures.
Overall, cold isostatic pressing is a versatile technique that finds applications in various industries. Its ability to produce parts without the need for expensive pressing dies, its suitability for producing large or complex compacts, and its capability to work with different materials make it a valuable manufacturing process.
Conclusion
Cold Isostatic Pressing (CIP) is a versatile and efficient method for shaping materials. It offers numerous benefits, such as uniform compression, high density, and the ability to form complex shapes. Also known as isostatic pressing, CIP uses a pressure vessel to apply equal force from all directions, resulting in consistent results.
With wet-bag and dry-bag variations, the process accommodates different materials and applications. CIP is widely used in industries like powder forming, food processing, and medical manufacturing. Its capabilities surpass those of traditional uniaxial or machine presses, making it a preferred choice for businesses aiming for precision and quality in their products.
If you are interested in this product you can browse our company website:https://kindle-tech.com/product-categories/isostatic-press, we understand that every customer's needs are unique. Therefore, we offer a flexible customisation service to meet your specific requirements. Whether it is the specification, functionality or design of the equipment, we are able to personalise it to suit your needs. Our dedicated team will work closely with you to ensure that the customised solution will perfectly meet your experimental needs.
CONTACT US FOR A FREE CONSULTATION
KINTEK LAB SOLUTION's products and services have been recognized by customers around the world. Our staff will be happy to assist with any inquiry you might have. Contact us for a free consultation and talk to a product specialist to find the most suitable solution for your application needs!