Description of Cold Isostatic Pressing
Table of Contents
- Description of Cold Isostatic Pressing
- Comparison Between Uniaxial Pressing and Cold Isostatic Pressing
- Key Advantages of Cold Isostatic Pressing versus Uniaxial Pressing
- Benefits of Benchtop CIP in Laboratory Settings
- Applications of CIP in the Laboratory
- Cold Isostatic Pressing Wetbags and Molds
- Standard Operating Procedure for the Benchtop Cold Isostatic Press
Definition and process of Cold Isostatic Pressing (CIP)
Cold isostatic pressing (CIP) is a method of processing materials that involves compacting powders by enclosing them in an elastomer mold. The process is based on Pascal's law, which states that pressure applied in an enclosed fluid is transmitted in all directions throughout the fluid without any change in magnitude.
In CIP, an elastomer mold is used because it has low resistance to deformation. The powders are enclosed in the mold, and then liquid pressure is applied uniformly to the mold to compress it. This results in a highly compact solid. CIP can be used for various materials such as plastics, graphite, powdered metallurgy, ceramics, and sputtering targets.
Applications of CIP in various industries such as medical, aerospace, and automotive
CIP has a wide range of applications in different industries.
In the medical industry, CIP is used in the production of components for medical applications. The process helps to reduce distortion, improve accuracy, and minimize the risk of air entrapment and voids. Components produced using CIP are used in medical devices and implants.
In the aerospace industry, CIP is used for shaping and compacting powders into components used in aircraft and spacecraft. This method ensures high integrity and little distortion or cracking when the components are fired. CIP is particularly useful for parts that are too large to be pressed in other methods and do not require high precision in the sintered state.
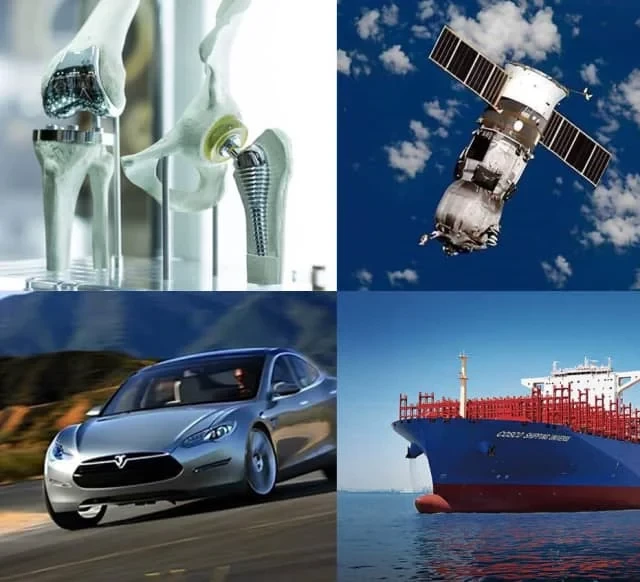
In the automotive industry, CIP is employed in the production of various components. The process helps to achieve a uniform density of the powders, resulting in high-quality components. CIP is used for parts such as engine components, transmission parts, and suspension components.
Overall, Cold Isostatic Pressing (CIP) is a valuable method for shaping and compacting powders into components of varying sizes and shapes. Its applications in industries such as medical, aerospace, and automotive highlight its versatility and importance in the manufacturing process.
Comparison Between Uniaxial Pressing and Cold Isostatic Pressing
Differences in the process and applications of uniaxial pressing and CIP
Both uniaxial pressing and Cold Isostatic Pressing (CIP) are methods for compacting powder samples. Uniaxial pressing involves applying force along one axis, typically up or down. It is used for pressing simple shapes with fixed dimensions, such as cylinders or squares. Uniaxial pressing requires a mold and a hydraulic press, making it a relatively inexpensive process. However, it has limitations. Firstly, it is suitable for samples with a short aspect ratio, as the powder close to the pressing surfaces is compacted more than the powder further away. Secondly, it can only be used for simple shapes.
On the other hand, CIP, also known as cold isostatic pressing, is similar to uniaxial pressing in terms of powder requirements and general process steps. However, there are significant differences. In CIP, compaction occurs under hydrostatic conditions, meaning the pressure is transmitted equally in all directions. This reduces or eliminates die wall friction. Additionally, CIP uses elastomeric molds instead of rigid dies. The powder is loaded into the flexible mold, sealed, and pressure is applied via a liquid in a pressure vessel. It is important to note that CIP is distinct from hot isostatic pressing (HIP), which is carried out at high temperatures.
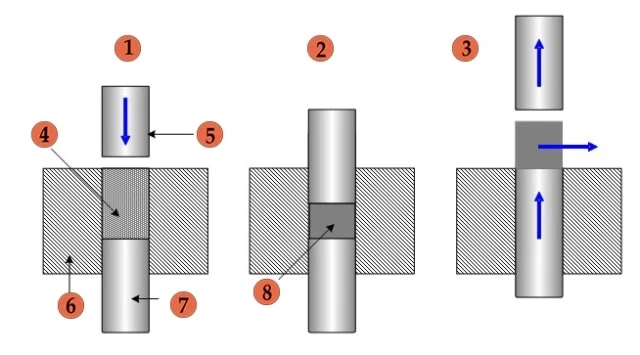
Limitations of uniaxial pressing
Uniaxial pressing is more suitable for small shapes and high production rates. Non-uniform densities may occur, especially for large aspect ratios (greater than 3:1), due to die wall friction. Therefore, it may not be suitable for achieving uniform properties and shape control.
Advantages and limitations of CIP
CIP is slower compared to uniaxial pressing but offers more versatility in terms of shape and size. It can be used to produce small or large, simple or complex shapes. The uniform green density achieved with CIP allows for more even shrinkage during sintering, which is crucial for good shape control and uniform properties. Unlike uniaxial pressing, CIP does not require a wax binder, eliminating the need for dewaxing operations.
CIP utilizes low-cost elastomer tooling, but close tolerances can only be obtained for surfaces pressed against a highly accurate steel mandrel. Surfaces in contact with the elastomer tooling may require post-machining for tight tolerances and good surface finishes.
Comparison of Isostatic Pressing Methods

When comparing uniaxial pressing to CIP, it is evident that CIP offers several advantages:
- More uniform product properties, greater homogeneity, and more precise control of finished product dimensions.
- Greater flexibility in the shape and size of the finished product.
- Longer aspect ratios are possible, allowing for the production of long, thin pellets.
- Improved compaction of the powder, leading to enhanced densification.
- Ability to process materials with different characteristics and shapes.
- Reduced cycle times and improved productivity.
In CIP, the sample can either be preformed into a shape using uniaxial pressing or placed in a flexible mold that can take almost any form. The sample is then placed into a hydraulic fluid chamber and subjected to high pressure. This uniform pressure from all directions allows for higher compaction compared to uniaxial pressing, making it suitable for producing large samples. CIP's benefit lies in its ability to produce complex samples with uniform density and shape. However, it should be noted that CIP can be a more expensive process compared to uniaxial pressing due to the equipment and materials required.
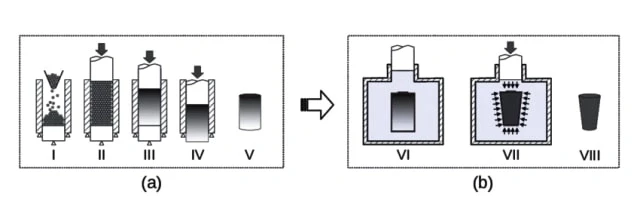
Key Advantages of Cold Isostatic Pressing versus Uniaxial Pressing
Uniformity and precision of CIP
Cold Isostatic Pressing (CIP) offers several advantages over Uniaxial Pressing when it comes to uniformity and precision. In CIP, pressure is applied uniformly over the entire surface of the mold, resulting in more uniform densities compared to uniaxial pressing. The absence of die-wall friction in CIP eliminates density distribution issues that may occur in cold-pressed parts. The elimination of die-wall lubricants in CIP also allows for higher pressed densities and eliminates problems associated with lubricant removal during final sintering. Additionally, CIP allows for the evacuation of air from the loose powder before compaction, resulting in increased and more uniform density.
Flexibility in shape and size
CIP offers greater flexibility in the shape and size of the finished product compared to uniaxial pressing. While uniaxial pressing is limited to simple shapes with fixed dimensions, CIP can be used to compact more complex shapes. The uniform compaction pressure in CIP does not limit the cross section-to-height ratio of the part, allowing for longer aspect ratios and the production of long, thin pellets. This flexibility in shape and size allows for more diverse applications and enables the production of parts with specific design requirements.
Improved powder compaction and densification
CIP provides improved compaction of the powder, leading to improved densification compared to uniaxial pressing. The uniform compaction pressure in CIP ensures more even shrinkage during sintering, resulting in better shape control and uniform properties of the finished product. The uniform green density achieved in CIP offers more consistent and predictable sintering behavior, which is essential for achieving desired product characteristics.
Ability to process varied materials and shapes
CIP has the ability to process materials with different characteristics and shapes compared to uniaxial pressing. It is suitable for both small and large, simple or complex shapes. CIP can be used to compact brittle or fine powders, providing increased density and relative freedom from compact defects. This makes CIP an ideal choice for applications where material properties and complex shapes are critical factors.
Reduced cycle times and improved productivity
While CIP may be slower than uniaxial pressing, it offers improved productivity in terms of reduced cycle times. The uniform compaction pressure in CIP allows for faster and more efficient processing, resulting in improved productivity. This can be particularly beneficial for high-volume production where cycle time reduction is a key factor.
In conclusion, Cold Isostatic Pressing (CIP) offers several advantages over Uniaxial Pressing, including uniformity and precision, flexibility in shape and size, improved powder compaction and densification, ability to process varied materials and shapes, and reduced cycle times and improved productivity. These advantages make CIP a preferred method for compacting powder samples in various industries.
Benefits of Benchtop CIP in Laboratory Settings
Cost-effectiveness of Benchtop CIP
Using a benchtop industrial oven in laboratory settings can offer significant cost savings. These smaller ovens are more energy-efficient compared to larger upright ones, making them ideal for heat-treating a small number of samples. Less energy is used and wasted, resulting in lower operating costs. Additionally, benchtop industrial ovens have a smaller footprint, allowing labs to utilize their space more effectively.
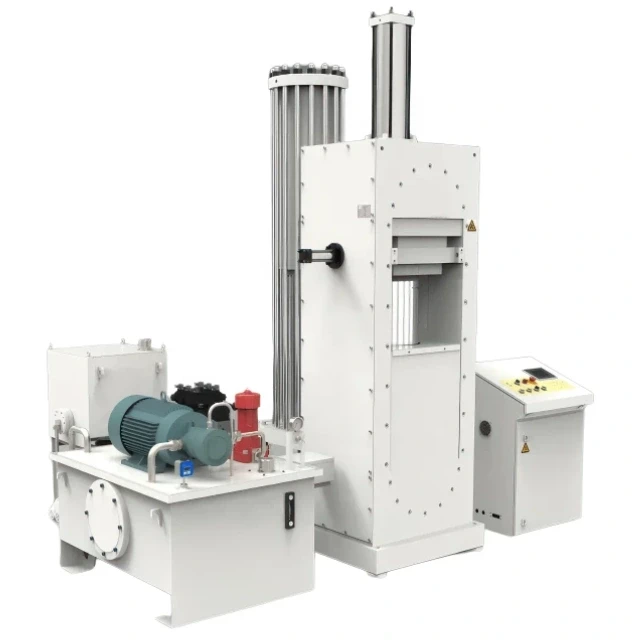
Efficiency in loading and unloading
One of the advantages of benchtop industrial ovens is their ease of loading and unloading. Due to their size, these ovens are easier to maneuver and reposition within the lab if needed. While they may not cater to large batch loads, they are perfect for labs that heat-treat a small number of samples. This efficiency in loading and unloading saves time and improves overall productivity.
Advantages in terms of size, weight, and maintenance
Benchtop CIP (Cold Isostatic Pressing) equipment offers several advantages in laboratory settings. These benchtop systems have a larger chamber diameter compared to piston-style ones while being five times lighter. This eliminates the need for additional heavy presses, reducing costs and maintenance requirements. Additionally, benchtop CIP equipment uses a static O-ring, resulting in longer O-ring life and reduced maintenance needs.
Ease of operation and mobility
Another benefit of benchtop CIP equipment is its ease of operation. These systems are designed to be user-friendly, allowing for easy operation even for non-experts. Moreover, benchtop CIP equipment is highly mobile, making it convenient to move between labs if required. This mobility enhances flexibility and enables labs to optimize their workflow.
In summary, benchtop CIP equipment offers numerous benefits in laboratory settings. It is cost-effective, efficient in loading and unloading, and provides advantages in terms of size, weight, and maintenance. Additionally, its ease of operation and mobility make it a valuable tool for laboratories. By utilizing benchtop CIP equipment, labs can improve productivity, save costs, and enhance their overall workflow.
Applications of CIP in the Laboratory
Situations where CIP is beneficial
CIP, or Cold Isostatic Pressing, offers several advantages in a laboratory setting:
- Reduced cost: Benchtop CIP reduces costs compared to traditional methods, such as piston-style presses. It is 5 times lighter and does not require additional heavy equipment.
- Faster loading and unloading: CIP allows for faster loading and unloading of samples, increasing efficiency in the laboratory.
- Reduced maintenance: CIP uses a static O-ring, which has a longer lifespan compared to dynamic O-rings used in traditional presses.
- More space and portability: Benchtop CIP takes up less space in the lab and can be easily moved between labs if needed.
- Easy operation: CIP is easy to operate, making it accessible to lab technicians.
Examples of specific use-cases for CIP
- Higher density before sintering: CIP can be used to achieve a higher density in materials before the sintering process.
- Preventing pellet disintegration: If your pellet keeps falling apart before sintering, CIP can help in maintaining its integrity.
- Pressing long/thin items: CIP is particularly useful for pressing long and thin items, such as a 5 mm diameter ceramic rod that is 100 mm long.
- Pressing irregular shapes: CIP can handle pressing irregular shapes, such as donuts or shapes with changing dimensions along their length.
An example use-case for CIP is when you want to press something long and thin, like a 5 mm diameter ceramic rod that is 100 mm long and will be sintered. Using a standard uniaxial die would not provide good compaction along the length, and the resulting product would be unstable. Additionally, the die sleeve would have to be unreasonably long. Benchtop CIP solves these issues by providing better compaction and stability for long and thin items.
Applications of the CIP process
CIP has various applications in the laboratory, including:
- Near-net-shape processing: CIP is used as a near-net-shape process to minimize waste and reduce costs, especially for expensive materials.
- Shaping difficult-to-machine materials: CIP is a viable option for shaping materials that are difficult to machine, making powder-processing a more suitable approach.
- Complex geometries: CIP allows for the production of complex shapes with relatively inexpensive and reusable flexible tools.
- Achieving uniformity and homogeneity: CIP is advantageous for applications that require a uniform microstructure to achieve specific mechanical performance.
- Multi-materials or graded structures: CIP is used when traditional joining techniques are not suitable, offering a solid-state joining process.
While CIP was initially used for simple shapes and preforms, recent advancements have expanded its applications in high-value sectors. Automotive, aerospace, power generation, and defense industries are utilizing CIP for various components, such as connecting rods, regeneratively cooled thrust chambers, reactor parts, and missile warhead casings.
In summary, CIP offers numerous benefits in the laboratory, including cost reduction, faster processes, and the ability to handle complex shapes. Its applications range from near-net-shape processing to achieving uniformity and joining multi-materials. With recent advancements, CIP is becoming increasingly popular for high-performance metal components in various industries.
Cold Isostatic Pressing Wetbags and Molds
Explanation of 'wetbag' pressing
Cold isostatic pressing (CIP) is a common method used for compacting raw powders into solid masses. One technique within CIP is known as wetbag pressing. In this process, the powder is filled into flexible molds made of rubber or elastomers. The mold is then sealed tightly and submerged in water (or sometimes other liquids) within a pressure vessel. Isostatic pressure is applied to the external surface of the mold, compressing the powder into a solid mass.
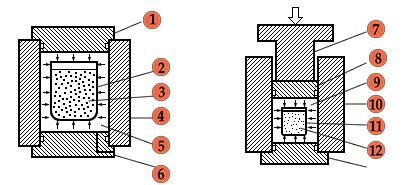
The wetbag technique allows for the pressing of tungsten ingots weighing up to 1 ton and the compaction of more complex components. It is not as common as other types of cold isostatic pressing, but there are over 3000 wet bag presses used worldwide. These wet bags come in various sizes, ranging from as small as 50mm to as big as 2000mm in diameter.
The wetbag process is relatively slow, taking anywhere from 5 to 30 minutes to process the material. However, advancements in high-volume pumps and loading mechanisms have helped to speed up the process.
Options for bags and molds for CIP
When it comes to wetbag pressing in cold isostatic pressing, there are a variety of options for the bags and molds that can be used. Thin flexible materials such as latex balloons or lab gloves can be utilized for simpler applications. These materials can withstand high pressures and are not highly strained or elongated under the pressure.
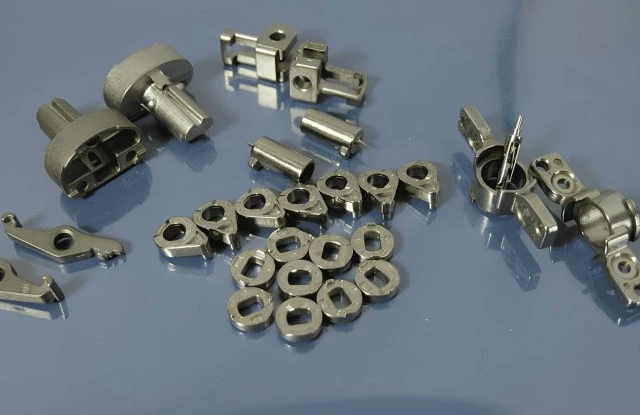
For more complex shapes or larger quantity production, custom latex molds can be used. These molds provide the necessary shape to the object being pressed. They are designed to withstand the high pressures and maintain the desired shape during the pressing process.
The choice of bag or mold will depend on the specific requirements of the pressing operation. Factors such as the shape of the object, the quantity of production, and the desired outcome will all play a role in determining the appropriate bag or mold to use.
In summary, wetbag pressing is a technique within cold isostatic pressing where powder is filled into flexible molds, sealed tightly, and submerged in a pressure fluid. Isostatic pressure is then applied to compress the powder into a solid mass. Various options for bags and molds, ranging from simple latex balloons to custom latex molds, are available to accommodate different pressing needs.
Standard Operating Procedure for the Benchtop Cold Isostatic Press
Preparation before starting CIP
Before you start operating the Benchtop Cold Isostatic Press (CIP), it is important to ensure that the equipment is in proper working order. Verify that the o-ring is in good condition and that the CIP is clean and free from any debris. Additionally, make sure you have some paper towels on hand to wipe up any oil spills and create a clean workspace.
Step-by-step procedure for operating a Benchtop CIP
-
Prepare the parts that you want to press. It is essential that all parts are clean and dry before proceeding.
-
Place the parts in a rubber bag and remove any excess air using a vacuum pump. Once the bag is sealed, carefully put it into the oil-filled chamber of the CIP.
-
Check the oil level in the chamber and ensure it is at the correct level. Close the CIP to begin the pressing cycle.
-
Gradually pressurize the CIP up to the desired pressure, which can be as high as 40,000 psi.
-
Hold the CIP at the desired pressure for a period of time, typically between 30 seconds to 5 minutes. It is normal to see a slight decrease in pressure as the sample reduces in size. However, if there is a significant drop in pressure, stop the process and check the o-ring and the assembly before restarting.
-
Once the pressing cycle is complete, release the pressure by opening the valve on the pump. Allow the pressure to reach zero before opening the CIP and retrieving the samples.
-
Remove the parts from the oil and dry off any excess oil. Be careful to keep the oil away from the samples. Inspect the parts for any defects or irregularities.
-
Afterward, wipe down the Cold Isostatic Press and check the condition of the o-ring. Store the equipment properly, ensuring it is ready for the next use.
Post-operation procedures and checks
After each use of the Benchtop Cold Isostatic Press, it is important to conduct post-operation procedures and checks. These include inspecting the parts for any defects or irregularities, ensuring that the CIP is clean and free from any oil spills, and checking the condition of the o-ring. Proper maintenance and storage of the equipment will help ensure its longevity and optimal performance.
Cold Isostatic Pressing (CIP) is a process that applies extremely high pressures using technologies such as cold isostatic pressing or similar methods. It is commonly used for sterilizing products or cold compacting powders. Cold isostatic pressing is performed at room temperature using a mold made from elastomer materials like urethane, rubber, or polyvinyl chloride. The fluid used in this process is usually oil or water, and the pressure ranges from 60,000 lbs/in2 (400 MPa) to 150,000 lbs/in2 (1000 MPa). However, it is important to note that this process may have a low geometric accuracy due to the flexible mold used. The powder is first compacted uniformly through cold isostatic pressing, and then conventionally sintered to produce the desired part.
If you are interested in this product you can browse our company website: https://kindle-tech.com/product-categories/isostatic-press, we understand that every customer's needs are unique. Therefore, we offer a flexible customisation service to meet your specific requirements. Whether it is the specification, functionality or design of the equipment, we are able to personalise it to suit your needs. Our dedicated team will work closely with you to ensure that the customised solution will perfectly meet your experimental needs.
CONTACT US FOR A FREE CONSULTATION
KINTEK LAB SOLUTION's products and services have been recognized by customers around the world. Our staff will be happy to assist with any inquiry you might have. Contact us for a free consultation and talk to a product specialist to find the most suitable solution for your application needs!