Introduction
Table of Contents
Hot Isostatic Pressing (HIP) is a powerful manufacturing process that plays a crucial role in enhancing the density of ceramic materials and reducing porosity in metals. It is widely utilized in various industries, including aerospace, powder metallurgy, and component manufacturing. HIP allows for the compression of metal powders to create homogenous annealed microstructure products with minimal impurities. Moreover, it facilitates through-processing, from alloy design to component manufacture. Understanding the concept and applications of HIP is essential for businesses looking to improve the quality and strength of their materials.
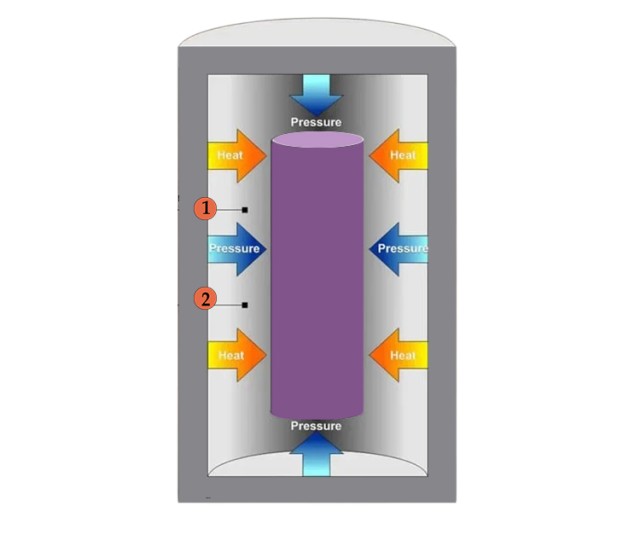
The Concept of Hot Isostatic Pressing
The role of Hot Isostatic Pressing (HIP) in reducing porosity of metals and enhancing density of ceramic materials
Hot Isostatic Pressing (HIP) is a manufacturing process used to reduce the porosity of metals and increase the density of many ceramic materials. It is widely utilized in powder metallurgy to compress metal powder at high temperatures and pressures, resulting in a compact solid with minimal or no impurities.
The primary application of HIP is in through-processing, from alloy design to component manufacture. It plays a crucial role in the production of aerospace components, among other industries. The HIP equipment typically features a 150mm diameter x 300mm long hot zone, making it suitable for scaling up samples.
Hot isostatic pressing is a versatile technology that can be applied to various materials, including metals, ceramics, polymers, and composites. By subjecting the material to elevated temperature and isostatic gas pressure, HIP eliminates porosity and increases density. This process improves the mechanical properties and workability of the materials.
In addition to reducing porosity in castings and consolidating powders, hot isostatic pressing is also used for diffusion bonding and pressure-assisted brazing. It is an integral part of the sintering process in powder metallurgy and is employed in the fabrication of metal matrix composites.
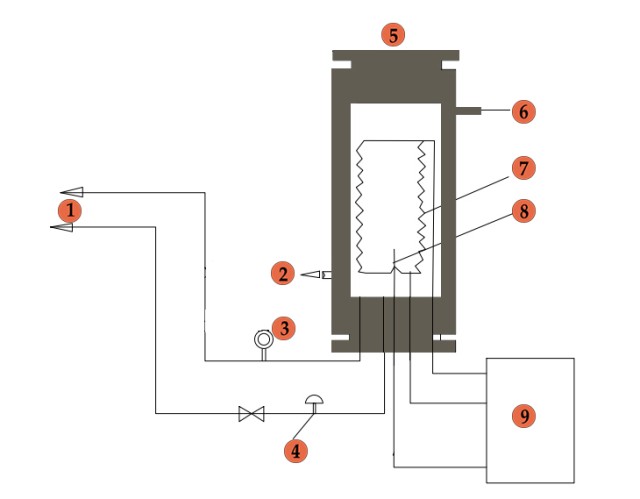
The hot isostatic pressing equipment consists of a high-pressure vessel, heating furnace, compressor, vacuum pump, storage tank, cooling system, and computer control system. The high-pressure vessel is the key component of the equipment, providing equal pressure from all directions to the parts being processed.
In the heat treatment industry, hot isostatic pressing, hydrogen combustion technology, and additive manufacturing technology are considered the most promising processes. The North American Heat Treatment Association ranked these three technologies as the top contenders in 2021.
Hot Isostatic Pressing (HIP) is a fundamental manufacturing technique used to increase the density of materials by reducing or eliminating porosity. By subjecting the materials to equal pressure from all sides, HIP creates fully dense materials with improved mechanical properties and workability. It is widely employed to enhance or create materials with different mechanical properties by improving density, composition, and dynamic strength.
In summary, Hot Isostatic Pressing (HIP) is a crucial process in reducing porosity in metals and increasing the density of ceramic materials. It plays a vital role in through-processing, allowing for the production of high-quality components with improved mechanical properties. The HIP equipment and technology are versatile, with applications in various industries, including aerospace.
Uses and Applications of Hot Isostatic Pressing
Utilization of HIP in powder metallurgy to compress metal powder
Hot Isostatic Pressing (HIP) is a process used in powder metallurgy to compress metal powder. By subjecting the metal powder to high temperatures and pressures, HIP allows for the creation of a compact solid with a homogenous annealed microstructure. This process helps to minimize impurities in the materials, resulting in high-quality metal products.
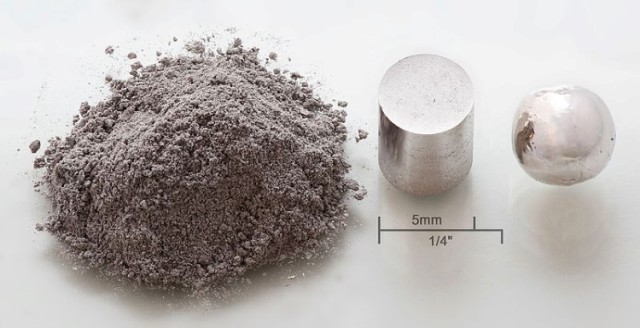
Creation of homogenous annealed microstructure products with minimal impurities
HIP is particularly significant in the creation of homogenous annealed microstructure products. Through a combination of deformation, creep, and diffusion, HIP effectively reduces porosity and increases the density of metals. This results in products with minimal impurities, ensuring superior quality and performance.
Significance in through-processing from alloy design to component manufacture
Hot Isostatic Pressing plays a crucial role in the through-processing of materials, from alloy design to component manufacture. It is an essential step in the manufacturing process of various industries, including aerospace. The HIP equipment's specifications, such as its 150mm diameter x 300mm long hot zone, make it suitable for scaling up samples and producing components for different applications.
Application in the manufacturing of aerospace components
Hot Isostatic Pressing is widely used in the manufacturing of aerospace components. The process helps to eliminate porosity and enhance the density of materials used in aerospace applications. By ensuring a homogenous annealed microstructure and minimal impurities, HIP contributes to the production of high-quality and reliable aerospace components.
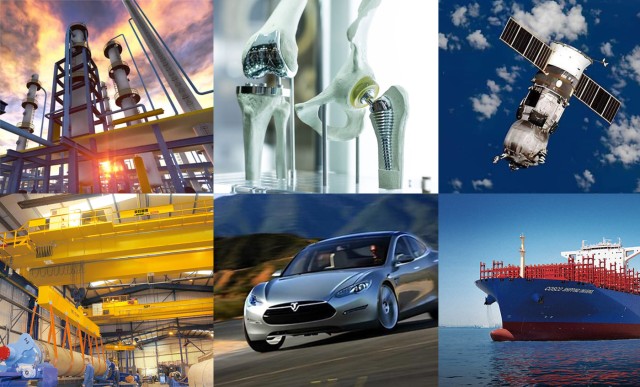
Hot Isostatic Pressing technology has various applications across industries such as automotive, energy, medical, and electronics. It is used to improve the mechanical properties and workability of materials by eliminating porosity and increasing density. The advancements in technology and equipment have led to more efficient and effective HIP processes, with higher pressures and enhanced material density.
The hot isostatic pressing process finds applications in industries such as automotive, aerospace, military, heavy equipment, industrial machinery, marine, oil and gas, and medical. It is used for compacting powders, shaping materials, material bonding, and more. The process is versatile and can be used for a wide range of parts and components in various applications.
Hot isostatic pressing equipment comes in different sizes, depending on the application. It can be used to create small parts in laboratory settings or large industrial parts. The equipment is controlled by computers, which program and regulate the temperature, pressure, and duration of the process. This ensures precise and consistent results.
Hot Isostatic Pressing (HIP) has been used for decades to consolidate metal powders and metal matrix composites. It is also utilized to eliminate porosity in sintered parts, produce metal-clad parts through diffusion bonding, and eliminate defects in castings. In recent years, HIP has become increasingly important in assuring and improving the quality of critical components produced through powder-based Additive Manufacturing.
Overall, Hot Isostatic Pressing is a versatile and essential process in various industries. It allows for the production of high-quality, dense, and reliable components with minimal impurities. Whether in powder metallurgy, aerospace manufacturing, or Additive Manufacturing, HIP plays a significant role in improving the quality and performance of materials and components.
Conclusion
Hot Isostatic Pressing (HIP) is a versatile and effective technique for reducing porosity in metals and enhancing the density of ceramic materials. It finds extensive use in various industries, including powder metallurgy, aerospace, and component manufacturing. HIP allows for the compression of metal powders, creation of homogenous annealed microstructure products, and seamless through-processing from alloy design to component manufacture. The specifications of HIP equipment, such as working pressure, control systems, thermocouple usage, vessel interior length, use of a graphite furnace, heating and cooling rates, and maximum sample size, play a crucial role in achieving desired results. With its numerous applications and specifications, HIP proves to be an essential process in material engineering and manufacturing.
If you are interested in our products, please visit our company website:https://kindle-tech.com/product-categories/isostatic-press, where innovation has always been a priority. Our R&D team consists of experienced engineers and scientists who closely follow industry trends and are constantly pushing the boundaries of what is possible. Our laboratory equipment incorporates the latest technology to ensure that you can obtain accurate and repeatable results during your experiments. From high-precision instruments to intelligent control systems, our products will provide you with unlimited possibilities for your experimental work.
CONTACT US FOR A FREE CONSULTATION
KINTEK LAB SOLUTION's products and services have been recognized by customers around the world. Our staff will be happy to assist with any inquiry you might have. Contact us for a free consultation and talk to a product specialist to find the most suitable solution for your application needs!