Introduction
Table of Contents
Isostatic pressing is a fascinating manufacturing process that has significant implications in various industries. It involves applying equal pressure from all directions to a material, resulting in improved strength and uniformity. This process is widely used in manufacturing, automotive, electronics, semiconductor, medical, aerospace and defense, energy and power, and research and development sectors. Isostatic pressing plays a crucial role in the aerospace and defense industry, where it is used to produce bulletproof materials and gun parts. With the rapidly growing aerospace and defense industry and increased investment in HIP technology, the isostatic pressing market is poised for substantial growth.
Overview of Isostatic Pressing
Isostatic pressing is a powder metallurgy (PM) procedure that evenly presses a powder compact in all directions to provide the greatest possible uniformity of density and microstructure without the geometrical restrictions of uniaxial pressing.
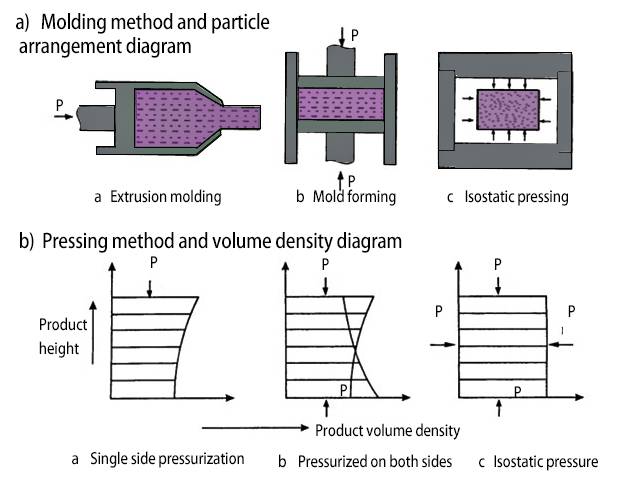
Definition of isostatic pressing
Isostatic pressing refers to a powder metallurgy (PM) procedure that evenly presses a powder compact in all directions to provide the greatest possible uniformity of density and microstructure without the geometrical restrictions of uniaxial pressing.
Main types: Hot Isostatic Pressing (HIP) and Cold Isostatic Pressing (CIP)
The main types in isostatic pressing are HIP and CIP. Hot isostatic pressing is a process of compressing materials under high temperatures and pressure. Hot isostatic pressing improves the mechanical properties of castings by eliminating internal microporosity.
Description of process types: wet bag pressing and dry bag pressing
Isostatic pressing can be done using two different process types: wet bag pressing and dry bag pressing. In wet bag pressing, a separate elastomeric mold is loaded outside of the press and then submerged in the pressure vessel. After pressurization and compaction, the mold is removed from the vessel, and the process is repeated. On the other hand, dry bag pressing creates a mold that is integrated into the pressure vessel. The powder is added to the mold, the mold is sealed, pressure is applied, and then the part is ejected.
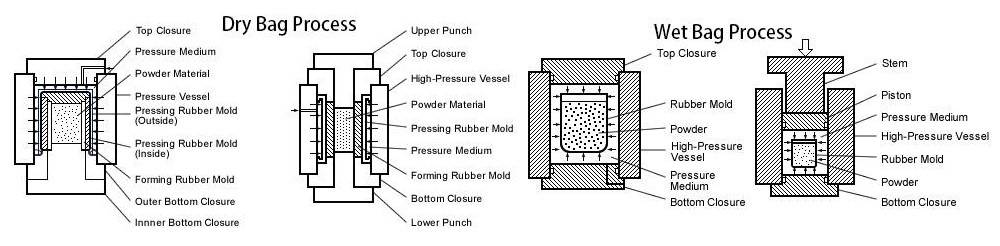
Discussion on capacities: small-sized hip, medium-sized hip, and large-sized hip
Isostatic pressing can be done in different capacities, including small-sized HIP, medium-sized HIP, and large-sized HIP. These different capacities allow for the production of components of various sizes and shapes. Depending on the specific requirements of the project, the appropriate capacity can be chosen.
In summary, isostatic pressing is a powder metallurgy process that provides uniform density and microstructure. It can be done using either hot isostatic pressing (HIP) or cold isostatic pressing (CIP). The process can be further categorized into wet bag pressing and dry bag pressing. Different capacities, such as small-sized HIP, medium-sized HIP, and large-sized HIP, are available to accommodate various project requirements.
Applications of Isostatic Pressing in Various Industries
Use in manufacturing, automotive, electronics and semiconductor, medical, aerospace and defense, energy and power, research and development sectors
Isostatic pressing, also known as cold isostatic pressing (CIP), is a manufacturing process that applies equal pressure from all directions to compact materials. This unique technique has found applications in various industries due to its numerous advantages.
One of the key advantages of isostatic pressing is the ability to achieve high and uniform density in compacted materials. Unlike other compaction methods, isostatic pressing does not require the use of lubricants, resulting in a more efficient and cost-effective process.
The manufacturing industry has widely adopted isostatic pressing for the production of complex-shaped parts. This process removes many of the constraints that limit the geometry of parts compacted unidirectionally in rigid dies. As a result, manufacturers can create intricate components with precise tolerances.
In the automotive industry, isostatic pressing is used to produce parts with low-penetrability material, which is essential for 3D printed components. This process also enables the increase in the density of metals, leading to improved mechanical properties of automotive parts.
The electronics and semiconductor industry also benefits from isostatic pressing. This technique allows for the production of ceramic products such as balls, tubes, fuse tubes, lighting tubes, and spark plug insulators. These components play a crucial role in the manufacturing of electronic devices and semiconductor equipment.
The medical sector utilizes isostatic pressing for the fabrication of pharmaceuticals, explosives, chemicals, and nuclear fuel ferrites. The uniform pressure applied during the process ensures consistent and reliable results in these critical applications.
The energy and power industry has also recognized the advantages of isostatic pressing. This technique is particularly suitable for difficult-to-compact and expensive materials such as superalloys, titanium, tool steels, stainless steel, and beryllium. It allows for highly efficient material utilization and contributes to the development of advanced energy systems.
Lastly, the research and development sector extensively employs isostatic pressing for various purposes. This versatile technique is suitable for a wide range of materials, including ceramics, metals, composites, plastics, and carbon. Its ability to apply uniform pressure to products of any shape or size makes it an invaluable tool in the innovation process.
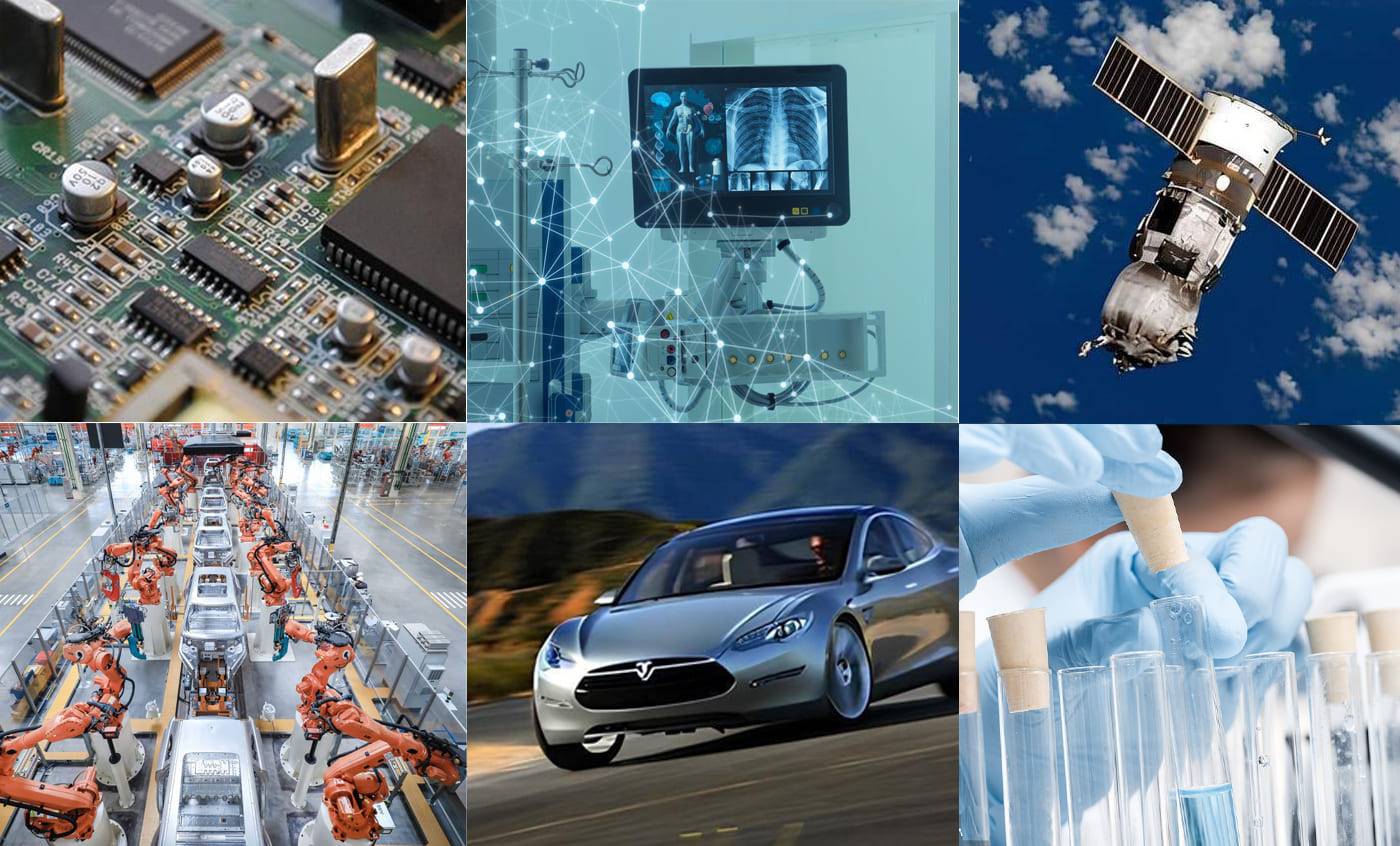
Specific application in aerospace and defense industry
The aerospace and defense industry is a major beneficiary of isostatic pressing technology. This industry involves the design, manufacturing, and development of advanced space systems, aircraft, and defense capabilities. Isostatic pressing plays a crucial role in the production of aerospace castings, jet aircraft engine components, and turbine blades.
In the defense sector, isostatic pressing is used for the production of bulletproof materials and gun parts. The uniform pressure applied during the process ensures the highest level of performance and reliability in these critical applications. Isostatic pressing enables the creation of intricate and durable gun parts, contributing to the overall effectiveness of defense systems.
The rapidly growing aerospace and defense industry is expected to drive the growth of the isostatic pressing market. The demand for advanced infrastructure in this sector, as predicted by the India Brand Equity Foundation, will reach $70 billion by 2030. This significant growth will further promote the adoption of isostatic pressing technology.
In conclusion, isostatic pressing finds applications across various industries, including manufacturing, automotive, electronics and semiconductor, medical, aerospace and defense, energy and power, and research and development. This unique technique offers numerous advantages such as high and uniform density, flexibility in part geometry, and efficient material utilization. The aerospace and defense industry, in particular, benefits from isostatic pressing in the production of critical components and bulletproof materials. With the continuous growth of these industries, the demand for isostatic pressing is expected to rise in the coming years.
Growth Factors of the Isostatic Pressing Market
Contribution of the rapidly growing aerospace and defense industry
The isostatic pressing market is experiencing significant growth due to the rapidly expanding aerospace and defense industry. This industry is involved in the design, manufacturing, and development of advanced space systems, aircraft, and defense capabilities. Isostatic pressing plays a crucial role in the aerospace industry for manufacturing aerospace castings, jet aircraft engine components, and turbine blades. It is also utilized in the defense industry for the production of bulletproof materials and gun parts. The growing aerospace and defense sector is expected to drive the growth of the isostatic pressing market. According to the India Brand Equity Foundation, the aerospace and defense sector is projected to reach $70 billion by 2030, further promoting the growth of the isostatic pressing market.
Projected growth of the aerospace and defense sector
The aerospace and defense sector is expected to witness significant growth in the coming years. This growth is driven by the increasing demand for advanced infrastructure in the industry. According to the India Brand Equity Foundation, the aerospace and defense sector is projected to reach $70 billion by 2030. With the demand for advanced space systems, aircraft, and defense capabilities, the need for isostatic pressing technology will also increase. Isostatic pressing is essential for the manufacturing of various components in the aerospace and defense sector, such as aerospace castings, engine components, and bulletproof materials.
Isostatic Pressing Market Size and Projections
The global isostatic pressing market was valued at $5.81 billion in 2019 and is projected to reach $7.97 billion by 2027, with a CAGR of 6.0% from 2020 to 2027. The market is segmented based on offering, type, HIP capacity, CIP process type, application, and region. The systems segment dominated the market in 2019, but the services segment is projected to be one of the most lucrative segments. The hot isostatic pressing (HIP) segment accounted for the majority of the market share in 2019, while the cold isostatic pressing (CIP) segment is expected to gain significant market share in the forecast period. North America dominated the market in terms of revenue in 2019 and is expected to continue this trend.
Overall, the growth factors of the isostatic pressing market include the contribution of the rapidly growing aerospace and defense industry, the projected growth of the aerospace and defense sector, and increased investment in HIP technology. These factors, along with the market projections, indicate a positive outlook for the isostatic pressing market in the coming years.
The global isostatic pressing market size was valued at $5.81 billion in 2019 and is projected to reach $7.97 billion by 2027, registering a CAGR of 6.0% from 2020 to 2027.
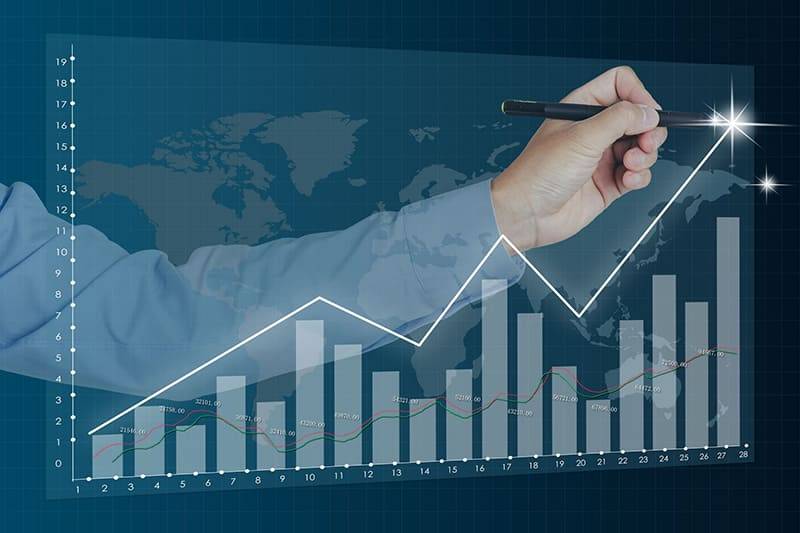
Segmentation of the Global Isostatic Pressing Market
By Type
The global isostatic pressing market is segmented into two types: Hot Isostatic Pressing (HIP) and Cold Isostatic Pressing (CIP). In 2019, the hot isostatic pressing segment dominated the market in terms of revenue. However, the cold isostatic pressing segment is projected to witness significant market share during the forecast period.
By Offering
The offering segment of the isostatic pressing market is divided into services and systems. The systems segment dominated the market, in terms of revenue in 2019, and is expected to maintain the same trend in the forecast period. The services segment is also projected to be one of the most lucrative segments.
By Process Type
Isostatic pressing can be done using two process types: wet bag pressing and dry bag pressing. The dry bag pressing segment accounted for a major share in the global isostatic pressing market in 2019. However, the wet bag pressing segment is expected to witness the highest compound annual growth rate (CAGR) during the forecast period.
By Capacity
The isostatic pressing market is divided based on capacity into three categories: small-sized HIP, medium-sized HIP, and large-sized HIP. In 2019, the large-sized HIP segment had the highest market share and is expected to maintain the same trend in the forecast period.
By End-User Industry
The end-user industries for isostatic pressing include manufacturing, automotive, electronics and semiconductor, medical, aerospace and defense, energy and power, research and development, and other end-users.
Market Size and Growth
The global isostatic pressing market size was valued at $5.81 billion in 2019 and is projected to reach $7.97 billion by 2027, registering a CAGR of 6.0% from 2020 to 2027. The precision machine manufacturing segment was adversely impacted by the COVID-19 pandemic.
Isostatic pressing is a process that uses fluid or gas pressure to modify materials by uniformly pressuring them in all directions to achieve maximum uniformity of density. This process can be conducted at high temperatures or at room temperature.
By application, the market is segmented into automotive, aerospace and defense, medical, precision machine manufacturing, energy and power, and others. The aerospace and defense segment accounted for the major share in the global isostatic pressing market in 2019, but the automotive segment is expected to witness the highest CAGR during the forecast period.
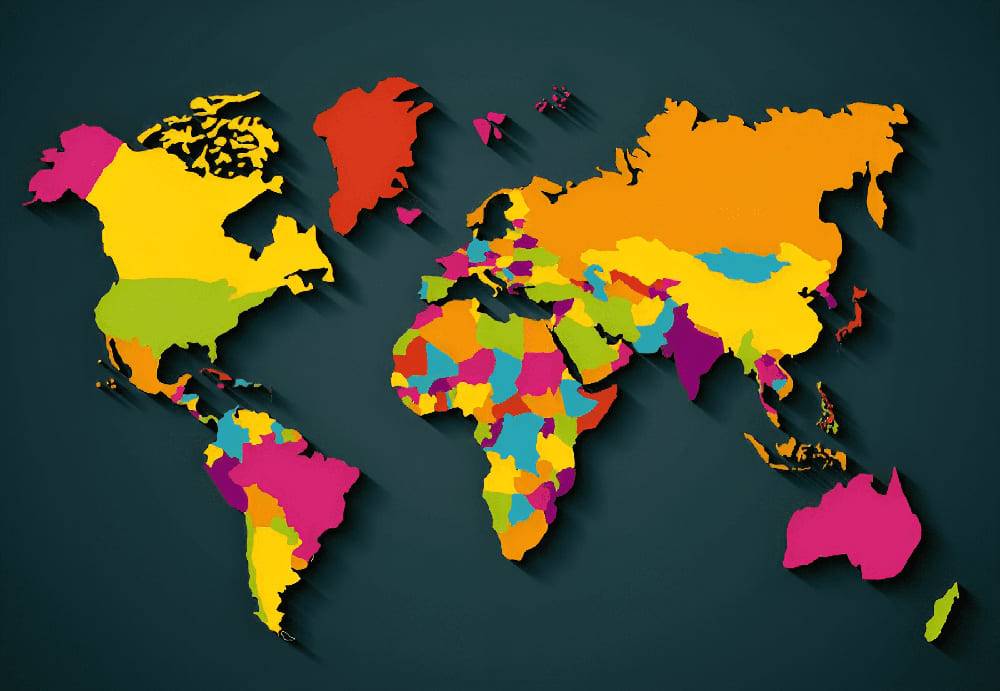
Regional Analysis The isostatic pressing market trends are analyzed across North America, Europe, Asia-Pacific, and LAMEA. North America dominated the market in terms of revenue in 2019 and is expected to maintain the same trend during the forecast period.
Conclusion
In conclusion, isostatic pressing plays a crucial role in various industries, including manufacturing, automotive, electronics, medical, aerospace and defense, energy, and research and development. Its applications range from the production of bulletproof materials to gun parts in the defense industry. The market for isostatic pressing is expected to grow significantly, driven by the rapid growth of the aerospace and defense sector and increased investment in HIP technology. Isostatic pressing is undoubtedly a technology with immense implications for numerous industries.
If you are interested in this product you can browse our company website:https://kindle-tech.com/product-categories/isostatic-press, we always insist on the principle of quality first. During the production process, we strictly control every step of the process, using high quality materials and advanced production technology to ensure the stability and durability of our products. to ensure that their performance meets the highest standards. We believe that only by providing customers with excellent quality can we win their trust and long-term cooperation.
CONTACT US FOR A FREE CONSULTATION
KINTEK LAB SOLUTION's products and services have been recognized by customers around the world. Our staff will be happy to assist with any inquiry you might have. Contact us for a free consultation and talk to a product specialist to find the most suitable solution for your application needs!