Carbon nanotubes (CNTs) have garnered significant attention due to their exceptional mechanical, electrical, and thermal properties. However, the question of whether they can be mass-produced is complex and depends on several factors, including production methods, scalability, cost, and application requirements. While significant progress has been made in scaling up CNT production, challenges such as maintaining quality, uniformity, and cost-effectiveness remain. Current methods like chemical vapor deposition (CVD) are promising but require further optimization for large-scale industrial applications. The potential for mass production exists, but it is contingent on overcoming these hurdles and aligning production capabilities with market demands.
Key Points Explained:
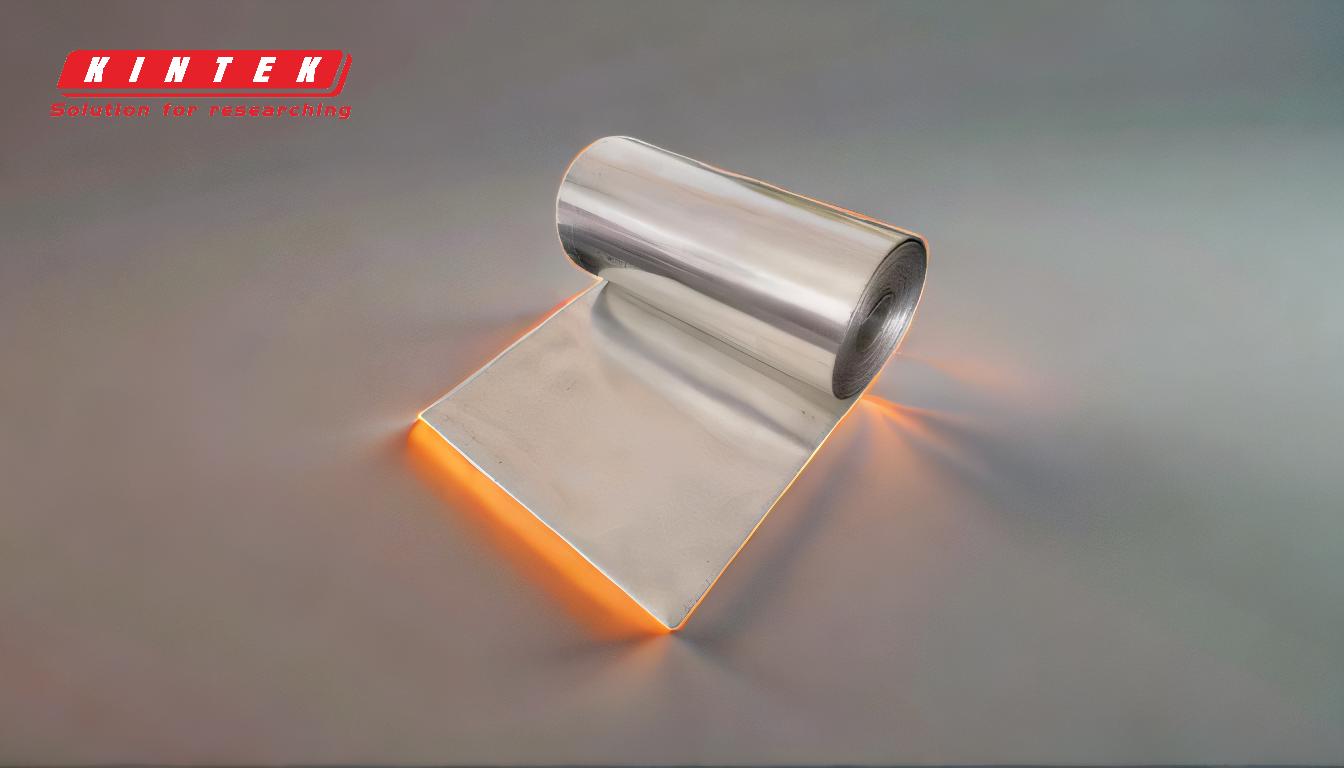
-
Current Production Methods:
- Chemical Vapor Deposition (CVD): This is the most widely used method for producing CNTs. It involves decomposing hydrocarbon gases at high temperatures in the presence of a catalyst. CVD is scalable and can produce high-quality CNTs, but it requires precise control over parameters like temperature, pressure, and catalyst composition.
- Arc Discharge and Laser Ablation: These methods produce high-quality CNTs but are less scalable and more expensive compared to CVD. They are typically used for research purposes rather than mass production.
- Other Emerging Techniques: Methods like plasma-enhanced CVD and fluidized bed reactors are being explored to improve scalability and reduce costs.
-
Scalability Challenges:
- Uniformity and Quality Control: Mass production requires consistent quality and uniformity, which is challenging due to the sensitivity of CNT growth to process conditions. Variations in temperature, catalyst activity, and gas flow can lead to defects or inconsistencies.
- Cost-Effectiveness: Scaling up production often involves significant capital investment and operational costs. Reducing the cost of raw materials, energy consumption, and catalyst usage is critical for making CNTs economically viable for mass markets.
- Environmental and Safety Concerns: CNT production involves hazardous chemicals and high-energy processes. Addressing safety and environmental regulations adds complexity to scaling up production.
-
Applications Driving Mass Production:
- Electronics and Energy Storage: CNTs are used in transistors, sensors, and batteries due to their excellent electrical conductivity and mechanical strength. The growing demand for advanced electronics and energy storage solutions is driving efforts to scale up CNT production.
- Composites and Coatings: CNTs are incorporated into polymers, metals, and ceramics to enhance their properties. Applications in aerospace, automotive, and construction industries require large quantities of CNTs, pushing the need for mass production.
- Medical and Biotechnology: CNTs are explored for drug delivery, imaging, and tissue engineering. While these applications currently require smaller quantities, advancements in production could expand their use.
-
Progress and Future Outlook:
- Industrial-Scale Facilities: Companies like Nanocyl, Arkema, and OCSiAl have established production facilities capable of producing hundreds of tons of CNTs annually. These efforts demonstrate the feasibility of mass production.
- Research and Development: Ongoing research focuses on optimizing production methods, developing new catalysts, and improving process efficiency. Breakthroughs in these areas could significantly enhance scalability.
- Market Demand: The success of mass production depends on aligning production capabilities with market needs. As new applications emerge and demand grows, the incentive to scale up production will increase.
In conclusion, while carbon nanotubes can be mass-produced to some extent, achieving large-scale, cost-effective, and high-quality production remains a work in progress. Advances in production technologies, coupled with growing market demand, are likely to drive further progress in this area.
Summary Table:
Aspect | Details |
---|---|
Production Methods | - Chemical Vapor Deposition (CVD): Scalable, high-quality, precise control. |
- Arc Discharge & Laser Ablation: High-quality, less scalable, expensive. | |
- Emerging Techniques: Plasma-enhanced CVD, fluidized bed reactors. | |
Scalability Challenges | - Uniformity & Quality Control: Sensitive to process conditions. |
- Cost-Effectiveness: High capital and operational costs. | |
- Environmental & Safety Concerns: Hazardous chemicals, high-energy processes. | |
Applications | - Electronics & Energy Storage: Transistors, sensors, batteries. |
- Composites & Coatings: Aerospace, automotive, construction industries. | |
- Medical & Biotechnology: Drug delivery, imaging, tissue engineering. | |
Future Outlook | - Industrial-scale facilities: Hundreds of tons annually. |
- Research & Development: Optimizing methods, new catalysts, efficiency. | |
- Market Demand: Aligning production with growing application needs. |
Learn how carbon nanotubes can revolutionize your industry—contact our experts today for more insights!