Ceramics are well-known for their ability to withstand high temperatures, making them a preferred material in applications where thermal stability is critical. Their high-temperature resistance stems from their chemical composition and bonding structure, which include ionic or covalent bonds. These bonds provide ceramics with exceptional thermal stability, allowing them to maintain structural integrity even under extreme heat. Additionally, ceramics exhibit other advantageous properties such as corrosion resistance, wear resistance, and oxidation resistance, which further enhance their suitability for high-temperature environments. Traditional ceramics, such as those used in cooking vessels, have historically demonstrated this capability, while advanced ceramics are engineered for even more demanding applications.
Key Points Explained:
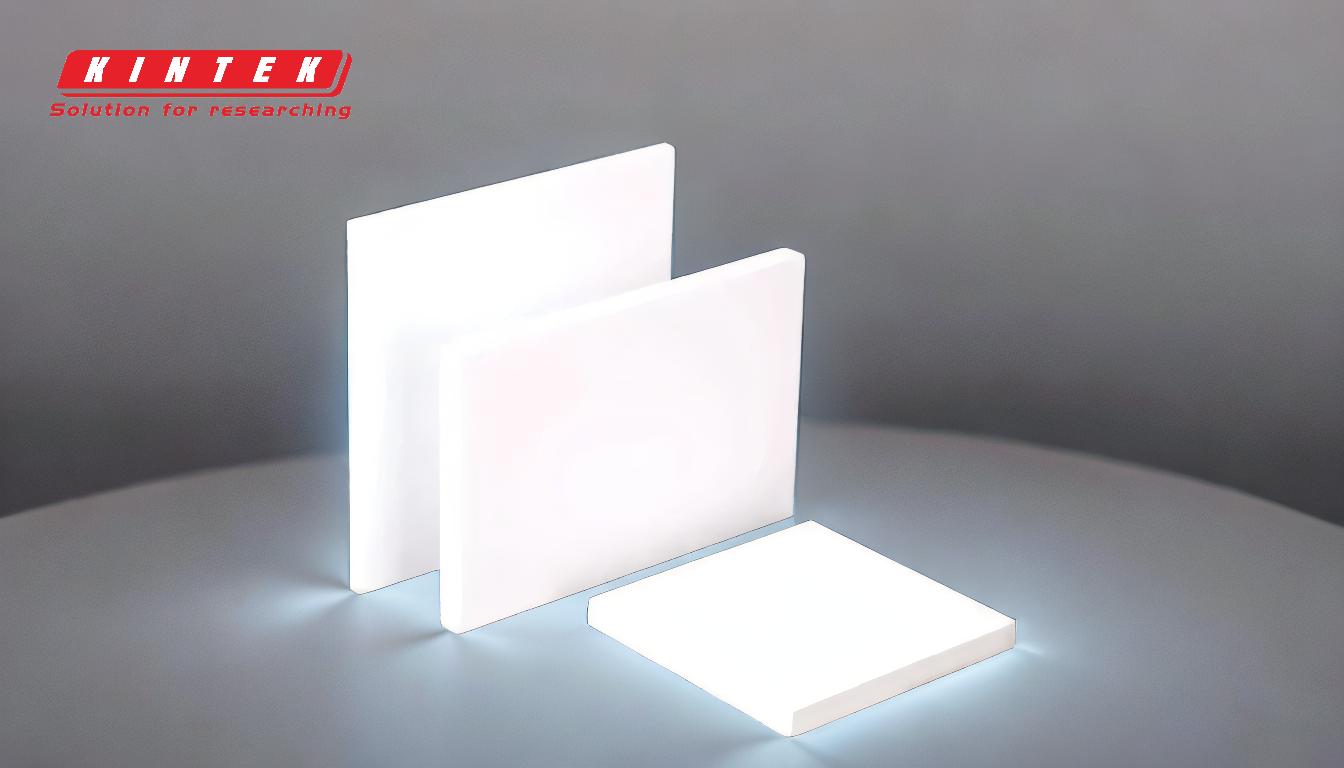
-
Chemical Composition and Bonding Structure
- Ceramics are composed of ionic or covalent bonds, which are inherently strong and stable.
- These bonds contribute to their ability to resist high temperatures without breaking down or losing structural integrity.
- Advanced ceramics, in particular, are engineered with precise compositions to enhance their thermal stability and other properties.
-
High-Temperature Resistance
- Ceramics can withstand extremely high temperatures, often exceeding those tolerated by metals or polymers.
- This makes them ideal for applications such as furnace linings, jet engine components, and thermal insulation.
- Their resistance to thermal shock (sudden temperature changes) is also a key advantage in many industrial settings.
-
Corrosion and Oxidation Resistance
- In addition to high-temperature resistance, ceramics are highly resistant to corrosion and oxidation.
- This ensures that they remain durable and functional even in harsh environments, such as those involving chemical exposure or high humidity.
- Oxidation resistance is particularly important in high-temperature applications where materials are exposed to air or other oxidizing agents.
-
Historical and Modern Applications
- Traditional ceramics, such as those used in cooking vessels and pottery, have demonstrated thermal stability for centuries.
- Modern advanced ceramics are used in cutting-edge technologies, including aerospace, energy, and medical devices, where high-temperature performance is critical.
- Examples include ceramic coatings for turbine blades and heat shields for spacecraft.
-
Comparison with Other Materials
- Compared to metals and polymers, ceramics generally have superior high-temperature resistance.
- Metals may melt or lose strength at high temperatures, while polymers can degrade or burn.
- Ceramics, however, retain their properties even under extreme heat, making them indispensable in many high-temperature applications.
-
Limitations and Considerations
- While ceramics excel in high-temperature environments, they can be brittle and prone to cracking under mechanical stress.
- Careful design and material selection are necessary to mitigate these limitations.
- Advanced manufacturing techniques, such as additive manufacturing, are being explored to improve the toughness and reliability of ceramic components.
By understanding these key points, purchasers of equipment and consumables can make informed decisions about selecting ceramics for high-temperature applications, ensuring optimal performance and durability.
Summary Table:
Property | Description |
---|---|
Chemical Composition | Ionic or covalent bonds provide exceptional thermal stability. |
High-Temperature Resistance | Withstands extreme heat, ideal for furnace linings and jet engine components. |
Corrosion Resistance | Resists chemical exposure and oxidation in harsh environments. |
Applications | Used in aerospace, energy, and medical devices for high-temperature performance. |
Limitations | Brittle under mechanical stress; requires careful design and material selection. |
Need ceramics for high-temperature applications? Contact our experts today to find the right solution!