Yes, a furnace can indeed have multiple zones, and this capability is particularly valuable in various industrial and scientific applications. Multi-zone furnaces are designed to allow precise control over temperature in different sections or zones within the furnace. This is achieved through individually temperature-controlled zones, which enable distinct thermal conditions for different materials or sections within a sample. Such furnaces are essential in fields like materials science, semiconductor manufacturing, and the synthesis of complex ceramic structures and nano-sized materials.
Key Points Explained:
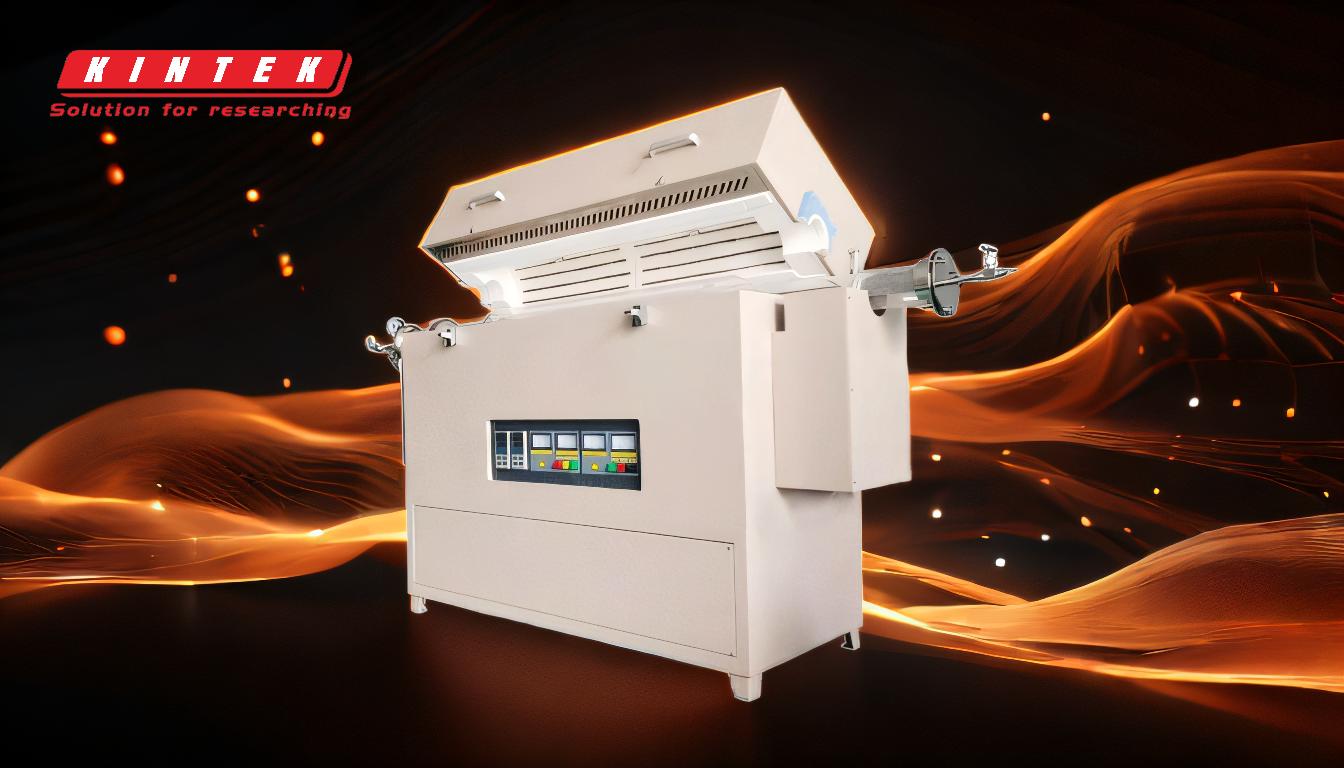
-
Definition of Multi-Zone Furnaces:
- Multi-zone furnaces are specialized heating systems that can have multiple independently controlled temperature zones.
- Each zone can be set to a different temperature, allowing for precise thermal management within the furnace.
-
Control Mechanisms:
- Temperature control in each zone is managed through advanced control systems, often involving zone boards and temperature sensors.
- These systems open and close dampers or adjust heating elements to maintain the desired temperature in each zone.
-
Applications:
- Materials Science: Different zones can be used to create varying thermal environments necessary for the synthesis and testing of new materials.
- Semiconductor Manufacturing: Precise temperature control is crucial for the fabrication of semiconductor devices, where different processes require different thermal conditions.
- Ceramic and Nano-Material Synthesis: The ability to create distinct thermal zones is essential for the development of complex ceramic structures and nano-sized materials.
-
Advantages:
- Precision: Multi-zone furnaces offer unparalleled precision in temperature control, which is critical for processes that require exact thermal conditions.
- Flexibility: They provide the flexibility to handle multiple materials or processes simultaneously, each under optimal thermal conditions.
- Efficiency: By allowing different zones to operate at different temperatures, these furnaces can be more energy-efficient compared to single-zone furnaces that might require heating the entire chamber to the highest needed temperature.
-
Types of Multi-Zone Furnaces:
- HVAC Systems: Standard HVAC systems can have up to four zones, while mini-split systems can have up to eight zones.
- Industrial Furnaces: These can be customized to have multiple zones depending on the specific requirements of the industrial process.
-
Technical Considerations:
- Zone Boards and Sensors: These are critical components that ensure accurate temperature control by monitoring and adjusting the thermal conditions in each zone.
- Dampers and Heating Elements: These components are adjusted based on sensor feedback to maintain the desired temperature in each zone.
In summary, multi-zone furnaces are highly sophisticated systems that offer precise and flexible temperature control across different zones. They are indispensable in fields that require exact thermal management, such as materials science, semiconductor manufacturing, and advanced material synthesis. The ability to independently control multiple zones within a single furnace provides significant advantages in terms of precision, flexibility, and efficiency.
Summary Table:
Aspect | Details |
---|---|
Definition | Furnaces with multiple independently controlled temperature zones. |
Control Mechanisms | Zone boards, temperature sensors, dampers, and heating elements. |
Applications | Materials science, semiconductor manufacturing, ceramic and nano-materials. |
Advantages | Precision, flexibility, and energy efficiency. |
Types | HVAC systems (up to 8 zones) and customizable industrial furnaces. |
Technical Components | Zone boards, sensors, dampers, and heating elements. |
Unlock the potential of multi-zone furnaces for your lab—contact us today to learn more!