Yes, you generally need different crucibles for different metals due to varying melting points, chemical reactivity, and thermal shock resistance requirements. The choice of crucible material depends on the specific metal or alloy being melted, the furnace type, and operational conditions. For instance, platinum or platinum alloys are suitable for high-temperature and chemically inert applications, while silicon carbide crucibles are preferred for copper-based alloys due to their thermal shock resistance. Matching the crucible's properties to the metal's characteristics ensures efficient melting, prevents contamination, and extends the crucible's lifespan.
Key Points Explained:
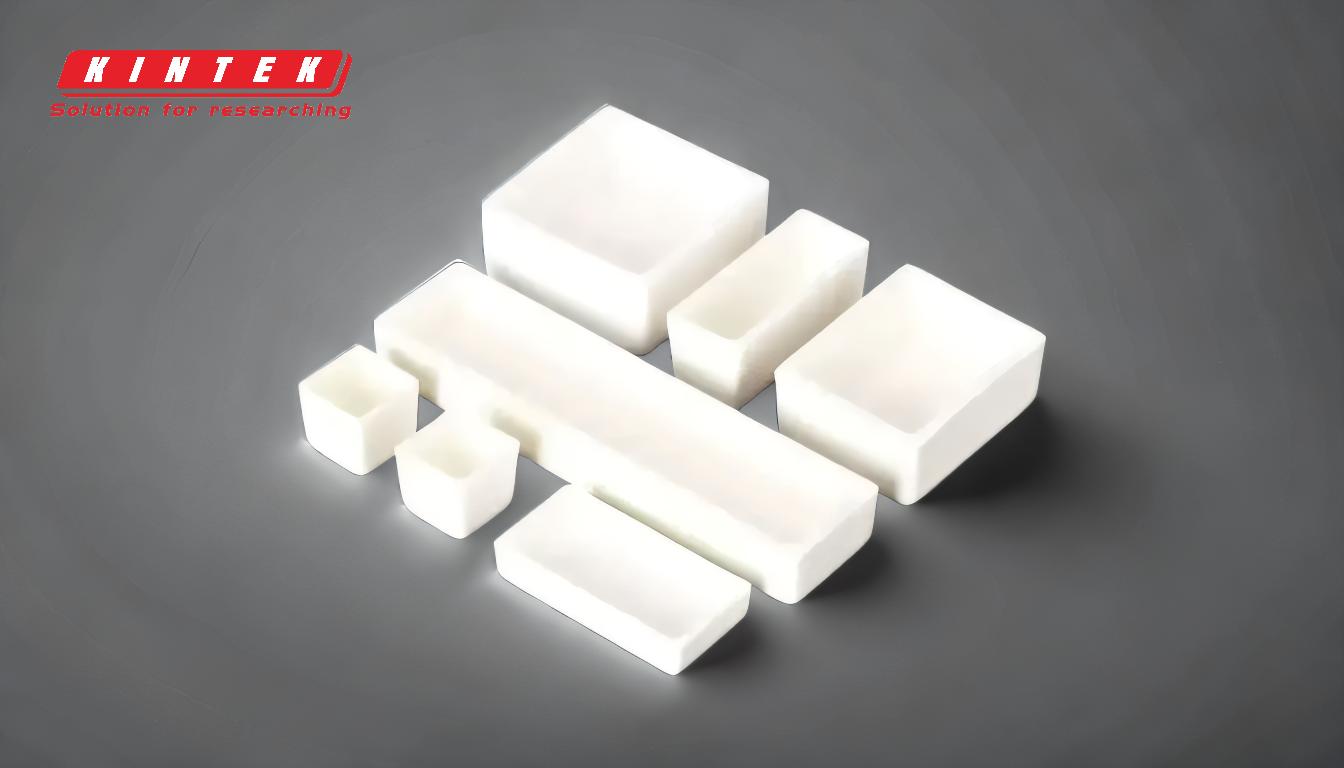
-
Crucible Material Selection Based on Metal Type:
- The material of the crucible must align with the metal or alloy being melted. For example:
- Platinum, platinum-rhodium, and platinum-gold alloys are ideal for high-temperature applications and chemically inert environments, making them suitable for precious metals and high-purity melts.
- Silicon carbide is preferred for copper-based alloys due to its high thermal shock resistance and durability in fuel-fired furnaces.
- Graphite and quartz are commonly used for specific metals, depending on their melting points and chemical compatibility.
- The material of the crucible must align with the metal or alloy being melted. For example:
-
Factors Influencing Crucible Choice:
- Melting Temperature: The crucible must withstand the metal's melting point without degrading. For example, platinum crucibles can handle extremely high temperatures, while graphite crucibles are suitable for lower-melting-point metals.
- Chemical Reactivity: The crucible material should not react with the metal being melted. For instance, silicon carbide is chemically stable with copper-based alloys, preventing contamination.
- Thermal Shock Resistance: Metals that undergo rapid temperature changes require crucibles with high thermal shock resistance, such as roller-formed silicon carbide.
-
Furnace Type and Operational Requirements:
-
Induction Furnaces: The crucible's electrical resistivity must match the furnace's operating frequency. For example:
- Lower frequency furnaces may require crucibles with high silicon carbide content.
- Higher frequency furnaces may need crucibles with high clay content.
- Fuel-Fired Furnaces: Crucibles must withstand direct flame exposure and thermal cycling, making silicon carbide a common choice.
-
Induction Furnaces: The crucible's electrical resistivity must match the furnace's operating frequency. For example:
-
Operational Considerations:
- Capacity and Dimensions: The crucible size should match the furnace and the volume of metal being melted.
- Charging and Emptying Methods: The crucible design should facilitate easy loading and pouring of molten metal.
- Fluxes and Additives: If fluxes or refining agents are used, the crucible material must resist chemical attack from these substances.
- Avoiding Cross-Contamination: For applications requiring high purity, dedicated crucibles for specific metals may be necessary.
-
Examples of Metal-Specific Crucible Choices:
- Copper-Based Alloys: Roller-formed silicon carbide crucibles are ideal due to their thermal shock resistance and chemical stability.
- Precious Metals (Gold, Silver, Platinum): Platinum or platinum-alloy crucibles are preferred for their high melting points and inertness.
- Aluminum and Magnesium Alloys: Graphite crucibles are often used because they resist reaction with these metals and provide good thermal conductivity.
- Iron and Steel: Clay-bonded graphite or silicon carbide crucibles are suitable for their high-temperature resistance and durability.
-
Importance of Matching Crucible Properties to Metal Characteristics:
- Using the wrong crucible material can lead to:
- Contamination of the melt.
- Premature crucible failure due to chemical attack or thermal stress.
- Inefficient melting processes, increasing energy consumption and costs.
- Proper selection ensures:
- Longer crucible lifespan.
- Consistent melt quality.
- Safe and efficient operation.
- Using the wrong crucible material can lead to:
In conclusion, selecting the right crucible for a specific metal involves careful consideration of material properties, operational conditions, and the metal's characteristics. This ensures optimal performance, prevents contamination, and maximizes the crucible's durability.
Summary Table:
Key Factor | Details |
---|---|
Crucible Material | Must align with metal type (e.g., platinum for high temps, silicon carbide for copper). |
Melting Temperature | Crucible must withstand metal's melting point without degrading. |
Chemical Reactivity | Material should not react with the metal to prevent contamination. |
Thermal Shock Resistance | Essential for metals undergoing rapid temperature changes. |
Furnace Type | Crucible properties must match furnace requirements (e.g., induction or fuel-fired). |
Operational Considerations | Includes capacity, charging methods, and resistance to fluxes/additives. |
Metal-Specific Examples | Copper: silicon carbide; Precious metals: platinum; Aluminum: graphite. |
Need help selecting the right crucible for your metal? Contact our experts today for personalized advice!