Hardening is a heat treatment process that significantly enhances the mechanical properties of metals, including strength, toughness, and wear resistance. Vacuum hardening, in particular, offers additional benefits by minimizing surface contamination and distortion, leading to more precise and consistent outcomes. This process is widely used in industries where high-performance metal components are required, as it improves durability and extends the lifespan of the treated materials.
Key Points Explained:
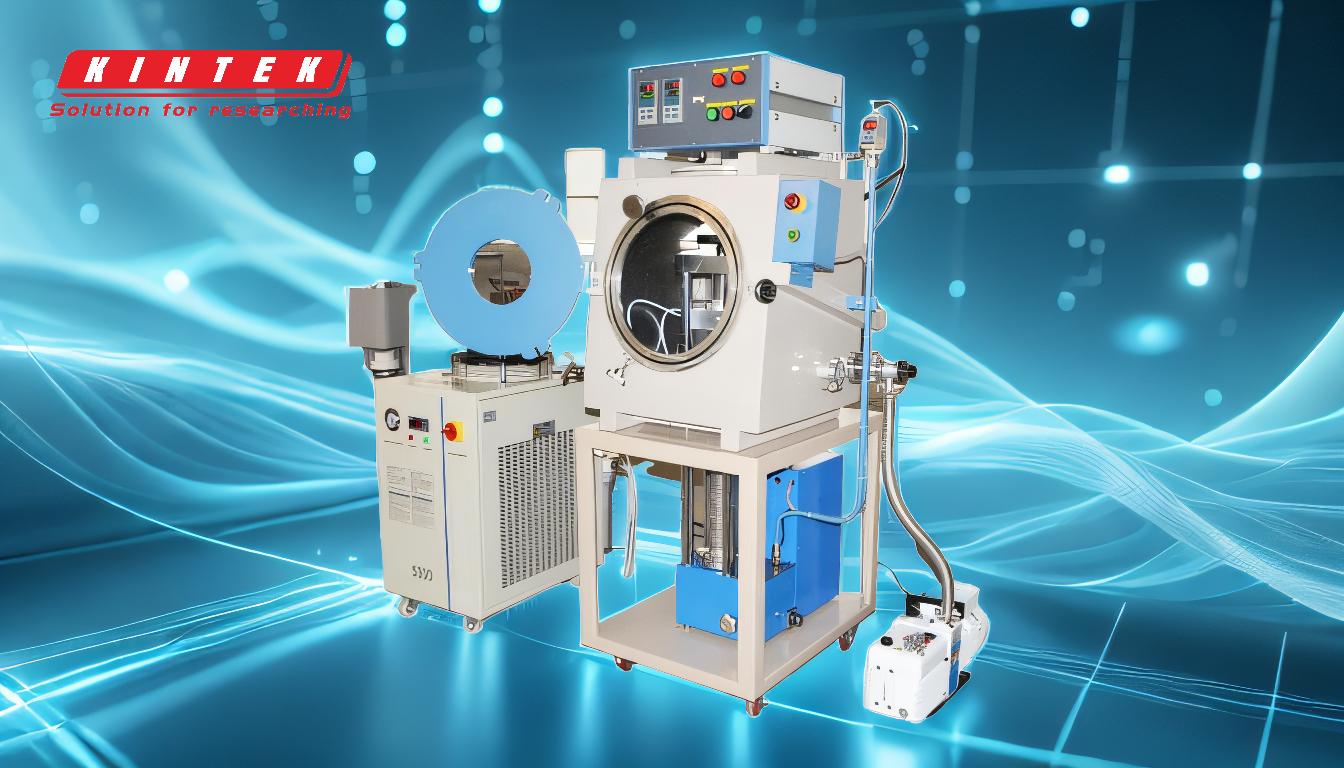
-
What is Hardening?
- Hardening is a heat treatment process that involves heating metal to a specific temperature and then rapidly cooling it, typically through quenching. This process alters the microstructure of the metal, increasing its hardness and strength. The rapid cooling locks the metal's atoms into a more rigid structure, making it less susceptible to deformation under stress.
-
How Does Hardening Increase Strength?
- Hardening increases strength by transforming the metal's microstructure. When heated, the metal's atoms become more mobile, allowing them to rearrange into a denser, more uniform structure. Rapid cooling (quenching) locks this structure in place, creating a harder and stronger material. This is particularly effective in steels, where the formation of martensite—a hard, brittle microstructure—significantly enhances strength.
-
Benefits of Vacuum Hardening
- Vacuum hardening is a specialized form of hardening that takes place in a vacuum or controlled atmosphere. This method offers several advantages:
- Minimized Surface Contamination: The absence of oxygen and other reactive gases prevents oxidation and scaling, resulting in a cleaner surface.
- Reduced Distortion: The controlled environment ensures uniform heating and cooling, reducing the risk of warping or distortion.
- Improved Mechanical Properties: Vacuum hardening enhances strength, toughness, and wear resistance, making it ideal for high-performance applications.
- Vacuum hardening is a specialized form of hardening that takes place in a vacuum or controlled atmosphere. This method offers several advantages:
-
Applications of Hardened Metals
- Hardened metals are used in a wide range of industries, including:
- Automotive: Components such as gears, shafts, and bearings require high strength and wear resistance.
- Aerospace: Critical parts like turbine blades and landing gear must withstand extreme conditions.
- Tool Manufacturing: Cutting tools, dies, and molds benefit from increased hardness and durability.
- Hardened metals are used in a wide range of industries, including:
-
Factors Influencing Hardening Effectiveness
- The effectiveness of hardening depends on several factors:
- Material Composition: Different alloys respond differently to hardening. For example, carbon steels are more amenable to hardening than stainless steels.
- Quenching Medium: The choice of quenching medium (oil, water, or air) affects the cooling rate and, consequently, the hardness and strength of the metal.
- Temperature Control: Precise control of heating and cooling temperatures is crucial to achieving the desired mechanical properties.
- The effectiveness of hardening depends on several factors:
-
Limitations of Hardening
- While hardening increases strength, it can also make metals more brittle. This trade-off between hardness and toughness must be carefully managed, especially in applications where impact resistance is critical. Additional processes, such as tempering, are often used to reduce brittleness while maintaining strength.
In summary, hardening is a highly effective method for increasing the strength of metals, particularly through processes like vacuum hardening that offer additional benefits. By understanding the underlying principles and factors influencing the process, manufacturers can optimize the mechanical properties of metal components for a wide range of applications.
Summary Table:
Aspect | Details |
---|---|
What is Hardening? | Heat treatment process involving heating and rapid cooling (quenching). |
Strength Increase | Transforms microstructure, creating a harder and stronger material. |
Vacuum Hardening | Minimizes contamination, reduces distortion, and improves mechanical properties. |
Applications | Automotive, aerospace, tool manufacturing. |
Key Factors | Material composition, quenching medium, temperature control. |
Limitations | Increased brittleness; tempered to balance hardness and toughness. |
Optimize your metal components with advanced hardening techniques—contact our experts today!