Yes, the type of solder you use matters significantly, as it directly impacts the quality, durability, and performance of your soldering work. Solder is a fusible metal alloy used to create a permanent bond between metal workpieces. The choice of solder depends on factors such as the materials being joined, the application (e.g., electronics, plumbing, or jewelry), and the desired properties of the joint (e.g., strength, conductivity, or corrosion resistance). Key considerations include the solder's composition (lead-based vs. lead-free), flux type, melting point, and compatibility with the materials being soldered. Using the wrong solder can lead to weak joints, poor electrical conductivity, or even damage to the components being soldered.
Key Points Explained:
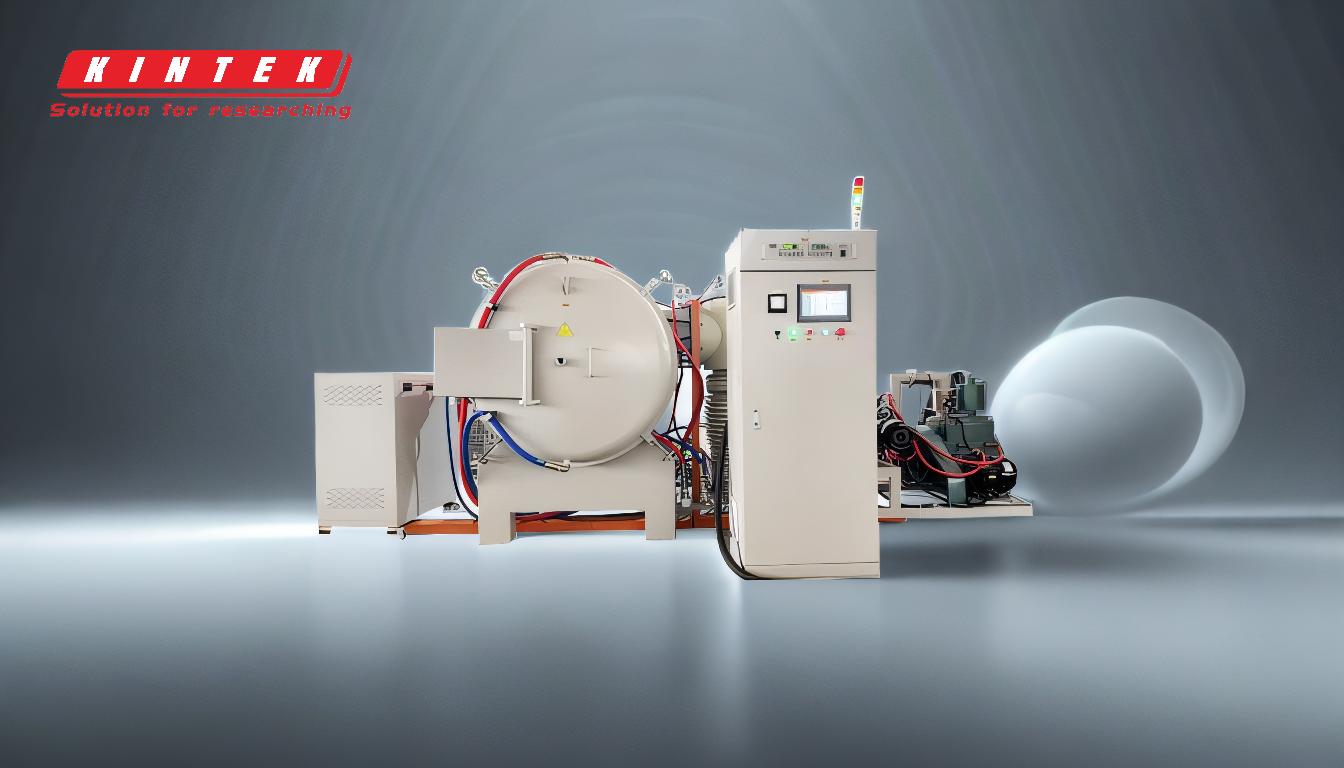
-
Solder Composition:
- Lead-Based Solder: Traditionally, lead-based solders (e.g., 60/40 tin-lead) have been widely used due to their low melting point, ease of use, and reliable joints. However, due to health and environmental concerns, their use has been restricted in many applications, particularly in electronics.
- Lead-Free Solder: Lead-free solders (e.g., tin-silver-copper alloys) are now the standard in many industries, especially electronics, due to RoHS (Restriction of Hazardous Substances) compliance. They have higher melting points and can be more challenging to work with but are safer and more environmentally friendly.
-
Flux Type:
- Rosin Flux: Commonly used in electronics, rosin flux helps remove oxidation and improves wetting, ensuring a strong bond. It is non-corrosive and leaves minimal residue.
- Water-Soluble Flux: More aggressive than rosin flux, it is used for applications requiring thorough cleaning. However, it can be corrosive if not cleaned properly.
- No-Clean Flux: Designed to leave minimal residue, no-clean flux is convenient for electronics but may not be suitable for high-reliability applications where residue could cause issues.
-
Melting Point:
- The melting point of the solder must be appropriate for the materials being joined and the application. For example, electronics typically require lower melting points to avoid damaging sensitive components, while plumbing may require higher melting points for stronger joints.
-
Material Compatibility:
- Solder must be compatible with the materials being joined. For instance, copper pipes require a different solder than circuit boards. Using incompatible solder can result in poor adhesion or even damage to the materials.
-
Application-Specific Requirements:
- Electronics: Requires precise, low-temperature solders with good electrical conductivity. Lead-free solders are often preferred due to regulatory requirements.
- Plumbing: Requires high-strength, corrosion-resistant solders, often with higher melting points.
- Jewelry: Requires solders that match the metal being worked on (e.g., silver solder for silver jewelry) and provide a clean, aesthetically pleasing joint.
-
Health and Safety Considerations:
- Lead-based solders pose health risks, particularly through inhalation of fumes or ingestion of lead particles. Proper ventilation and personal protective equipment (PPE) are essential when using such solders. Lead-free alternatives are safer but may still require precautions due to flux fumes.
-
Environmental Impact:
- Lead-free solders are more environmentally friendly and comply with regulations like RoHS. Proper disposal of solder waste, especially lead-based types, is crucial to minimize environmental harm.
In conclusion, selecting the right solder is critical for achieving reliable, durable, and high-quality soldering results. Consider the specific requirements of your project, including material compatibility, application, and regulatory compliance, to choose the most appropriate solder.
Summary Table:
Factor | Details |
---|---|
Solder Composition | Lead-based (low melting point) vs. lead-free (RoHS compliant, higher melting point). |
Flux Type | Rosin (non-corrosive), water-soluble (aggressive), no-clean (minimal residue). |
Melting Point | Varies by application (lower for electronics, higher for plumbing). |
Material Compatibility | Must match materials (e.g., copper pipes vs. circuit boards). |
Application | Electronics (low temp), plumbing (high strength), jewelry (aesthetic joints). |
Health & Safety | Lead-based solders pose health risks; lead-free is safer but requires precautions. |
Environmental Impact | Lead-free solders are eco-friendly and comply with RoHS regulations. |
Need help selecting the right solder for your project? Contact our experts today for personalized advice!