PVD (Physical Vapor Deposition) coatings are renowned for their durability, resistance to corrosion, and scratch resistance. While they are highly durable and resistant to fading, their longevity and appearance depend on factors such as the substrate material, environmental conditions, and the specific application. PVD coatings are harder and more resistant to wear compared to traditional finishes, making them less likely to fade over time. However, extreme conditions or improper handling can still affect their appearance. Overall, PVD coatings are among the most durable and fade-resistant coatings available.
Key Points Explained:
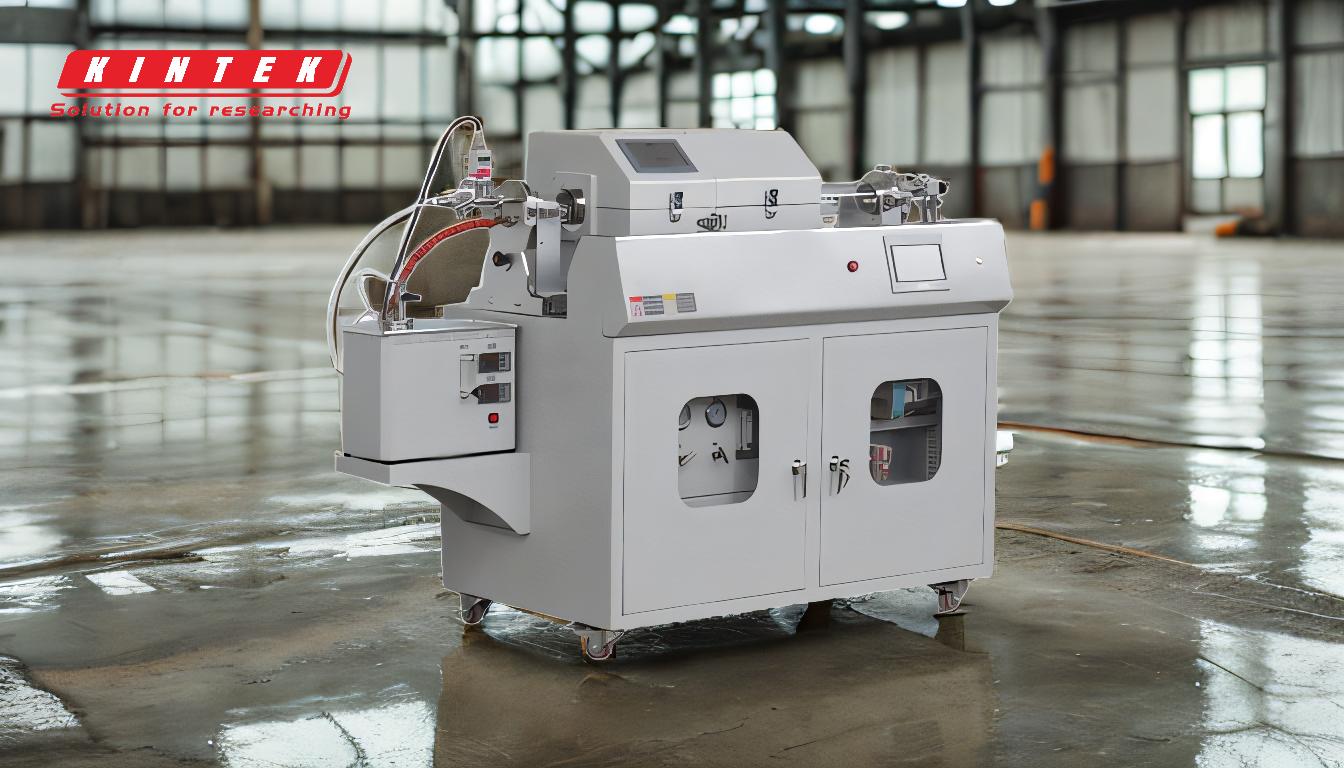
-
Durability of PVD Coatings:
- PVD coatings are considered super-hard and are among the most durable coatings available today.
- They are highly resistant to corrosion, scratching, and oxidation, which contributes to their long-lasting appearance.
- The vacuum environment during the PVD process ensures a strong bond with the substrate, preventing contamination and degradation.
-
Resistance to Fading:
- PVD coatings are less likely to fade compared to traditional finishes due to their hardness and resistance to environmental factors like moisture and oxygen.
- Their thinness (0.5 to 5 microns) and strong adhesion to the substrate make them difficult to remove or degrade, preserving their appearance over time.
-
Factors Influencing Fading:
- While PVD coatings are highly durable, extreme conditions such as high temperatures, abrasive environments, or improper handling can potentially affect their appearance.
- The substrate material and the specific type of PVD coating used also play a role in determining how well the coating resists fading.
-
Comparison to Traditional Finishes:
- PVD coatings outperform traditional finishes in terms of durability and resistance to fading.
- They are more resistant to wear, corrosion, and environmental degradation, ensuring a longer-lasting finish.
-
Applications and Longevity:
- PVD coatings are ideal for demanding applications where durability and appearance retention are critical.
- Their robust properties make them suitable for industries such as automotive, aerospace, and consumer electronics, where long-term performance is essential.
In conclusion, PVD coatings are highly resistant to fading due to their hardness, durability, and resistance to environmental factors. While they are not entirely immune to wear under extreme conditions, they are among the most fade-resistant coatings available, making them a superior choice for long-lasting finishes.
Summary Table:
Key Aspect | Details |
---|---|
Durability | Super-hard, resistant to corrosion, scratching, and oxidation. Strong bond with substrate. |
Resistance to Fading | Less likely to fade due to hardness, thinness (0.5-5 microns), and strong adhesion. |
Factors Influencing Fading | Extreme conditions, substrate material, and type of PVD coating can affect appearance. |
Comparison to Traditional Finishes | More resistant to wear, corrosion, and environmental degradation. |
Applications | Ideal for automotive, aerospace, and consumer electronics due to long-lasting performance. |
Want to learn more about PVD coatings and their benefits? Contact us today for expert advice!