Diamond-like coatings (DLC) are applied using advanced deposition techniques, primarily Physical Vapor Deposition (PVD) and Chemical Vapor Deposition (CVD). These methods involve creating a thin, durable layer of Diamond-Like Carbon (DLC) on the surface of tools or components. PVD involves evaporating a source material and allowing it to condense onto the tool, forming a mono-layer of DLC typically 0.5 to 2.5 microns thick. CVD, on the other hand, uses hydrogen and methane gases in a chamber, where tungsten wires heated to over 2,300°C break down the gases, allowing carbon atoms to recombine and form a pure diamond film on the tool surface. Both methods require precise control of temperature, pressure, and gas composition to achieve optimal results.
Key Points Explained:
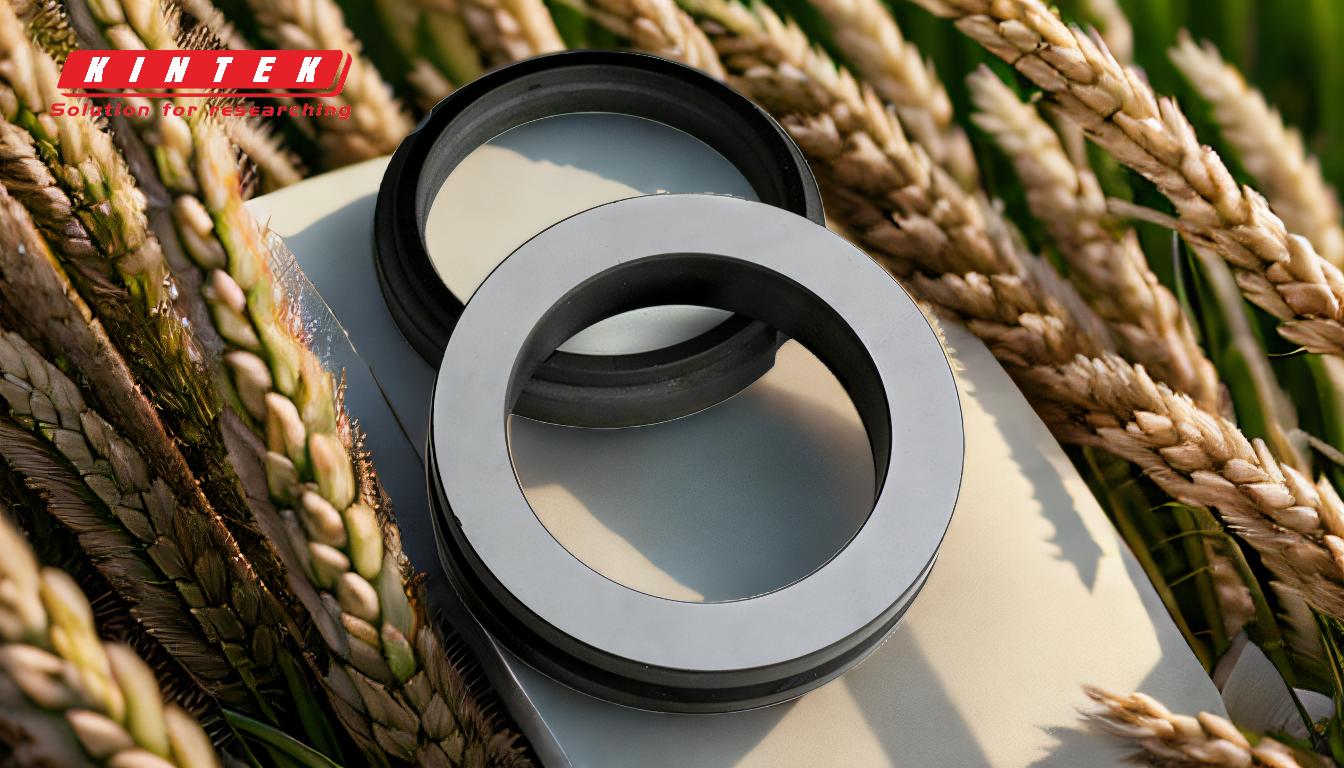
-
Overview of Diamond-Like Coatings (DLC):
- DLC coatings are thin, hard, and wear-resistant layers applied to tools or components to enhance their performance and longevity.
- These coatings are amorphous, meaning they lack a crystalline structure, but they exhibit properties similar to diamond, such as high hardness and low friction.
-
Primary Coating Methods:
-
Physical Vapor Deposition (PVD):
- PVD is a widely used method for applying DLC coatings.
- The process involves evaporating a source material (often carbon-based) in a vacuum chamber.
- The evaporated material then condenses onto the surface of the tool, forming a thin, uniform layer of DLC.
- The coating thickness typically ranges from 0.5 to 2.5 microns.
- PVD is known for its ability to produce high-quality, adherent coatings with excellent wear resistance.
-
Chemical Vapor Deposition (CVD):
- CVD is another common method for applying DLC coatings.
- In this process, the tool is placed in a chamber filled with hydrogen and methane gases.
- Tungsten wires heated to over 2,300°C provide the energy needed to break down the gas molecules.
- The activated carbon atoms then recombine on the tool's surface, forming a pure diamond film.
- CVD is particularly effective for creating thicker, more durable coatings.
-
Physical Vapor Deposition (PVD):
-
Process Steps for Applying DLC Coatings:
-
Preparation:
- The tool or component to be coated must be thoroughly cleaned and prepared to ensure proper adhesion of the coating.
- This often involves removing any surface contaminants, such as oils or oxides, through chemical or mechanical means.
-
Loading into the Chamber:
- The prepared tools are loaded into the deposition chamber.
- In PVD, the chamber is evacuated to create a vacuum, while in CVD, the chamber is filled with the appropriate gases.
-
Deposition:
- For PVD, the source material is evaporated, and the vapor condenses onto the tool's surface.
- For CVD, the gases are activated, and the carbon atoms deposit onto the tool.
-
Cooling and Finishing:
- After deposition, the coated tools are allowed to cool slowly to prevent thermal stress.
- The final coating is inspected for quality, thickness, and adhesion.
-
Preparation:
-
Key Parameters and Considerations:
-
Temperature:
- Both PVD and CVD processes require high temperatures, typically ranging from 750°C to over 2,300°C, depending on the method.
- Proper temperature control is crucial to ensure the quality and adhesion of the coating.
-
Gas Composition:
- In CVD, the composition of the hydrogen and methane gases must be carefully controlled to achieve the desired carbon deposition.
-
Coating Thickness:
- The thickness of the DLC coating is a critical factor in determining its performance.
- Thicker coatings may offer better wear resistance but could also be more prone to cracking or delamination.
-
Adhesion:
- Ensuring strong adhesion between the coating and the substrate is essential for the coating's durability.
- This often involves pre-treatment of the substrate or the use of intermediate layers.
-
Temperature:
-
Applications of DLC Coatings:
- DLC coatings are used in a wide range of industries, including automotive, aerospace, medical devices, and cutting tools.
- They are particularly valued for their ability to reduce friction, resist wear, and extend the life of components subjected to harsh conditions.
-
Advantages and Limitations:
-
Advantages:
- High hardness and wear resistance.
- Low friction coefficient, reducing energy consumption and improving efficiency.
- Excellent corrosion resistance.
- Ability to coat complex geometries.
-
Limitations:
- High cost of equipment and process.
- Limited thickness due to potential for internal stress and cracking.
- Requires precise control of process parameters.
-
Advantages:
-
Future Trends:
- Ongoing research is focused on improving the adhesion, thickness, and uniformity of DLC coatings.
- Advances in nanotechnology and hybrid coating methods are expected to further enhance the performance and applicability of DLC coatings in various industries.
By understanding these key points, equipment and consumable purchasers can make informed decisions about the application of diamond-like coatings, ensuring they select the most appropriate method and parameters for their specific needs.
Summary Table:
Aspect | Details |
---|---|
Primary Methods | PVD (Physical Vapor Deposition), CVD (Chemical Vapor Deposition) |
Coating Thickness | 0.5 to 2.5 microns (PVD), thicker for CVD |
Key Parameters | Temperature (750°C to 2,300°C), gas composition, adhesion, coating thickness |
Applications | Automotive, aerospace, medical devices, cutting tools |
Advantages | High hardness, low friction, corrosion resistance, complex geometries |
Limitations | High cost, limited thickness, precise parameter control required |
Optimize your tools with advanced DLC coatings—contact our experts today for tailored solutions!