Ball mill capacity is a critical factor in determining the efficiency and productivity of a milling operation. It refers to the maximum amount of material that a ball mill can process within a given time frame, typically measured in tons per hour (tph) or cubic meters per hour (m³/h). Calculating ball mill capacity involves understanding the mill's dimensions, operational parameters, and the properties of the material being processed. Key factors include the mill's diameter, length, rotational speed, filling ratio, and the grindability of the material. By considering these variables, one can estimate the mill's throughput and optimize its performance for specific applications.
Key Points Explained:
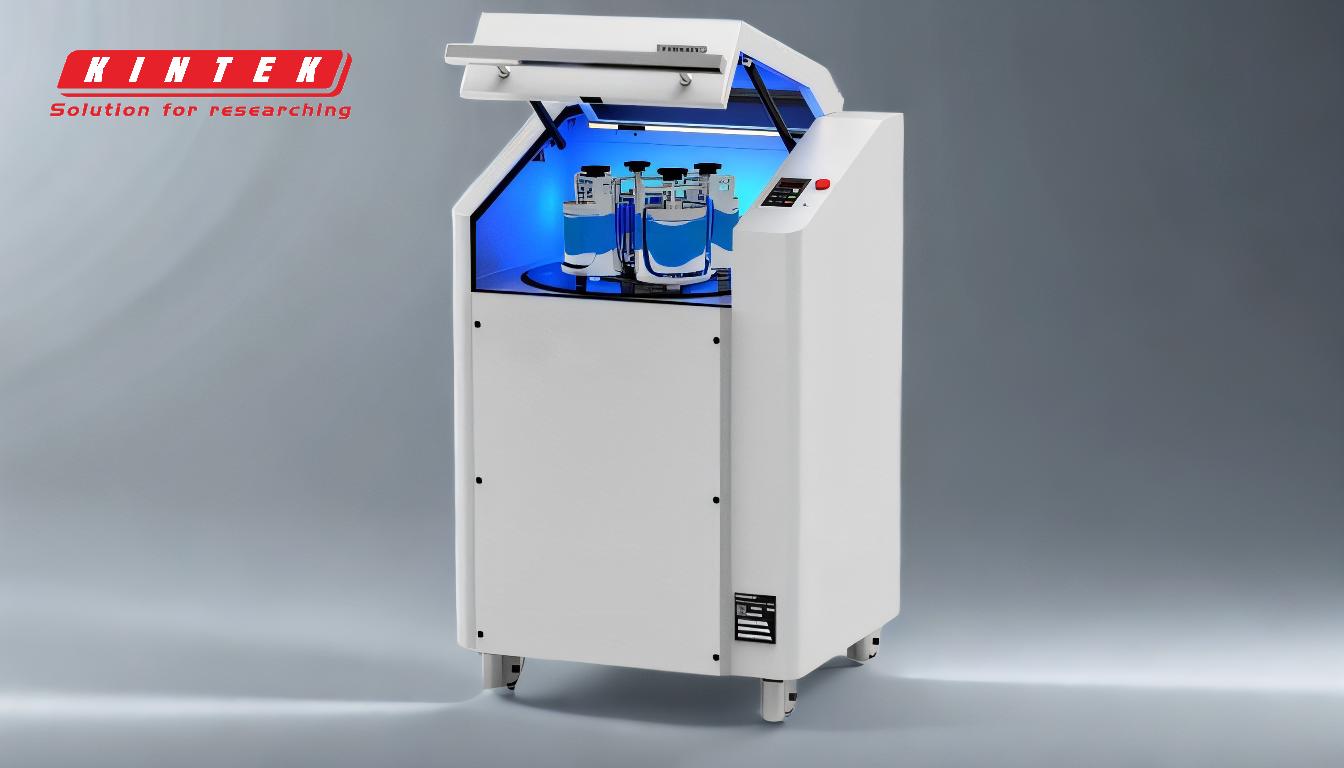
-
Understanding Ball Mill Capacity:
- Ball mill capacity refers to the maximum amount of material that can be processed by the mill in a given time.
- It is influenced by several factors, including the mill's physical dimensions, operational parameters, and the characteristics of the material being ground.
-
Key Factors Affecting Ball Mill Capacity:
- Mill Dimensions: The diameter and length of the mill directly impact its capacity. Larger mills can hold more material and thus have higher capacities.
- Rotational Speed: The speed at which the mill rotates affects the grinding efficiency. Optimal speed ensures that the grinding media (balls) cascade and impact the material effectively.
- Filling Ratio: This is the percentage of the mill volume filled with grinding media. A higher filling ratio can increase capacity but may also affect grinding efficiency.
- Material Properties: The grindability, density, and moisture content of the material being processed play a significant role in determining capacity. Harder materials may require more energy and time to grind, reducing capacity.
-
Calculation Methods:
-
Empirical Formulas: There are several empirical formulas used to estimate ball mill capacity. One common formula is:
[
Q = \frac{V \cdot n \cdot \eta \cdot \rho}{1000}
]
Where:
- ( Q ) = Mill capacity (tph)
- ( V ) = Mill volume (m³)
- ( n ) = Mill speed (rpm)
- ( \eta ) = Filling ratio (%)
- ( \rho ) = Material density (t/m³)
- Power-Based Calculations: Another approach is to use the mill's power consumption to estimate capacity. The Bond Work Index is often used in these calculations to account for the energy required to grind a specific material.
-
Empirical Formulas: There are several empirical formulas used to estimate ball mill capacity. One common formula is:
[
Q = \frac{V \cdot n \cdot \eta \cdot \rho}{1000}
]
Where:
-
Practical Considerations:
- Operational Efficiency: Factors such as liner wear, ball size distribution, and feed size can affect the actual capacity of the mill. Regular maintenance and optimization of these factors can help maintain or increase capacity.
- Material Feed Rate: The rate at which material is fed into the mill must be balanced with the mill's capacity to avoid overloading or underloading, both of which can reduce efficiency.
- Environmental Factors: Ambient temperature, humidity, and altitude can also influence mill performance and capacity, especially in open-circuit grinding systems.
-
Optimization Strategies:
- Grinding Media Optimization: Selecting the right size and type of grinding media can improve grinding efficiency and increase capacity.
- Mill Liners: Using appropriate mill liners can reduce wear and tear, leading to more consistent performance and higher capacity.
- Process Control: Implementing advanced process control systems can help maintain optimal operating conditions, ensuring that the mill operates at or near its maximum capacity.
-
Case Studies and Examples:
- Example 1: A cement plant increased its ball mill capacity by 15% by optimizing the ball size distribution and adjusting the mill speed.
- Example 2: A mining operation improved its mill capacity by 10% by switching to more durable mill liners and reducing the feed size of the material.
By understanding and applying these principles, operators can accurately calculate and optimize ball mill capacity, leading to improved efficiency and productivity in their milling operations.
Summary Table:
Key Factor | Impact on Capacity |
---|---|
Mill Dimensions | Larger diameter/length increases capacity. |
Rotational Speed | Optimal speed improves grinding efficiency. |
Filling Ratio | Higher ratio increases capacity but may affect efficiency. |
Material Properties | Harder materials reduce capacity due to higher energy requirements. |
Operational Efficiency | Maintenance and feed rate optimization can maintain or increase capacity. |
Grinding Media Optimization | Proper selection improves efficiency and capacity. |
Need help optimizing your ball mill capacity? Contact our experts today for tailored solutions!