Physical Vapor Deposition (PVD) coating is a sophisticated process used to apply thin, durable, and high-performance coatings to various substrates. The process involves several key steps, including substrate preparation, vaporization of the target material, transportation of the vaporized atoms, reaction with gases (if necessary), and deposition onto the substrate. The result is a highly adherent, abrasion-resistant, and corrosion-resistant film that enhances the substrate's properties. Below, we break down the PVD coating process into detailed steps and explain each phase to provide a comprehensive understanding.
Key Points Explained:
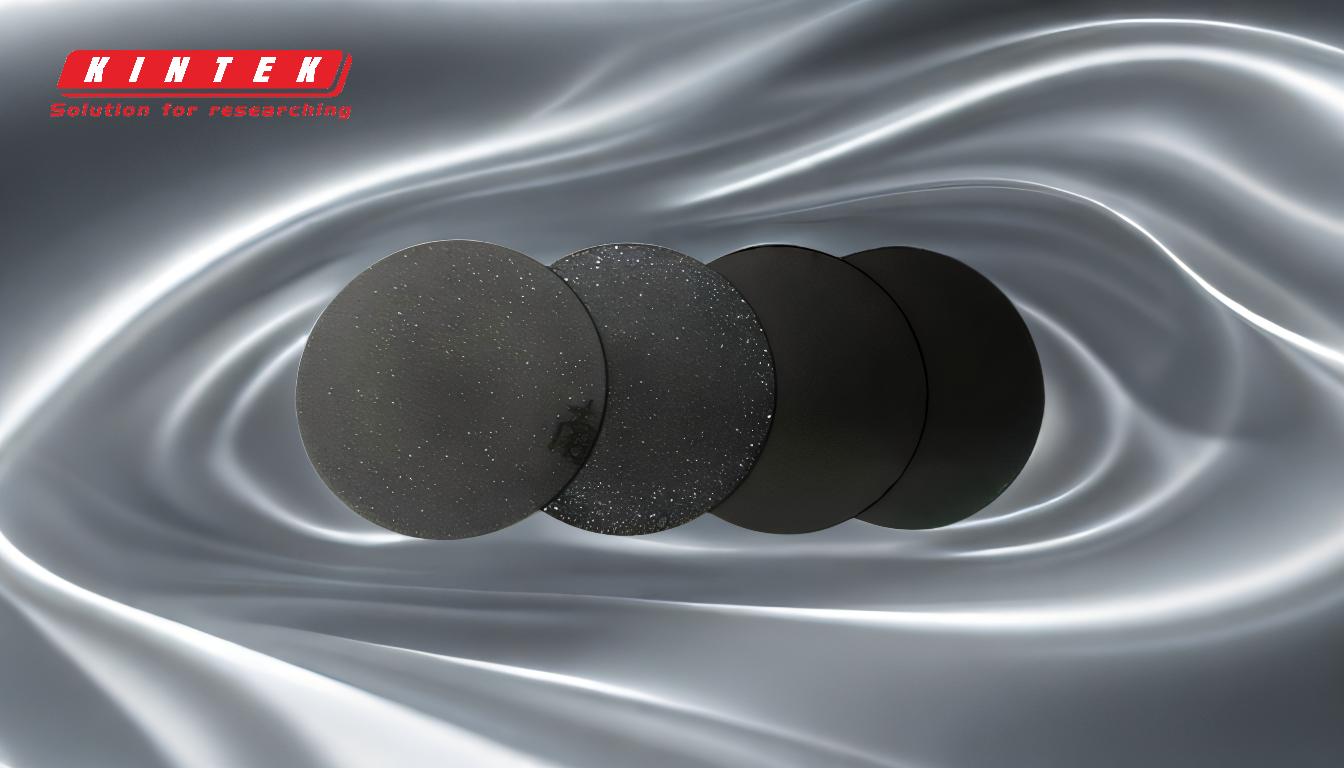
-
Substrate Preparation
- Cleaning: The substrate must be thoroughly cleaned to remove any contaminants, such as oils, dust, or oxides, that could interfere with coating adhesion. This is typically done using ultrasonic cleaning, chemical solvents, or plasma cleaning.
- Pretreatment: Pretreatment processes, such as ion bombardment or surface activation, are often used to improve the substrate's surface energy and ensure strong adhesion of the coating.
-
Vacuum Chamber Setup
- Evacuation: The substrate and target material are placed inside a vacuum chamber, which is then evacuated to create a high-vacuum environment. This removes air and other gases that could interfere with the coating process.
- Inert Gas Introduction: Inert gases like Argon are introduced to create a chemically unreactive atmosphere, which helps in maintaining the purity of the coating process.
-
Vaporization of the Target Material
- Energy Source: The target material is bombarded with a high-energy source, such as electrons, ions, or photons, to dislodge atoms from its surface. This process is known as ablation or sputtering.
- Vapor Phase: The dislodged atoms enter the vapor phase and are transported through the vacuum chamber toward the substrate.
-
Transportation of Vaporized Atoms
- Gas Flow: The vaporized atoms are transported across the chamber, often assisted by the flow of inert gases.
- Reaction with Gases (Optional): If the coating requires specific properties (e.g., hardness, color), the vaporized atoms may react with reactive gases like nitrogen, oxygen, or methane to form compounds such as nitrides, oxides, or carbides.
-
Deposition onto the Substrate
- Condensation: The vaporized atoms or compounds condense onto the substrate's surface, forming a thin, uniform film. This film bonds strongly with the substrate due to the high-energy conditions in the chamber.
- Layer Growth: The coating builds up layer by layer, typically reaching a thickness of a few microns.
-
Post-Coating Processes
- Quality Control: The coated substrate undergoes rigorous quality control checks to ensure the coating meets specifications. This includes checking for uniformity, adhesion, and surface finish.
- Finishing: Additional finishing processes, such as polishing or annealing, may be applied to enhance the coating's appearance or performance.
-
Time and Environmental Control
- Process Duration: The entire PVD coating process typically takes between 30 minutes to 2 hours, depending on the size of the substrate and the complexity of the coating.
- Temperature and Pressure Control: Precise control of temperature and pressure is maintained throughout the process to ensure optimal coating quality.
By following these steps, PVD coating creates a highly durable and functional layer that enhances the substrate's properties, making it suitable for applications in industries such as aerospace, automotive, medical devices, and consumer electronics. The process's ability to produce thin, uniform, and adherent coatings makes it a preferred choice for high-performance applications.
Summary Table:
Step | Description |
---|---|
1. Substrate Preparation | Cleaning and pretreatment to remove contaminants and improve surface energy for better adhesion. |
2. Vacuum Chamber Setup | Evacuation and introduction of inert gases to create a high-vacuum, chemically unreactive atmosphere. |
3. Vaporization | Target material is bombarded with energy to dislodge atoms, creating a vapor phase. |
4. Transportation | Vaporized atoms are transported, optionally reacting with gases to form compounds. |
5. Deposition | Atoms condense onto the substrate, forming a thin, uniform, and adherent film. |
6. Post-Coating Processes | Quality control checks and finishing processes to enhance coating performance. |
7. Time & Environmental Control | Precise control of temperature, pressure, and process duration for optimal results. |
Discover how PVD coating can improve your product's performance—contact us today for expert guidance!