Specifying an injection molding machine involves a detailed understanding of the product requirements, material properties, production volume, and machine capabilities. The process requires evaluating factors such as clamping force, shot size, injection pressure, and machine size to ensure compatibility with the intended application. Additionally, considerations like energy efficiency, automation options, and maintenance requirements play a crucial role in selecting the right machine. This step-by-step approach ensures that the chosen machine meets both technical and operational needs while optimizing cost and performance.
Key Points Explained:
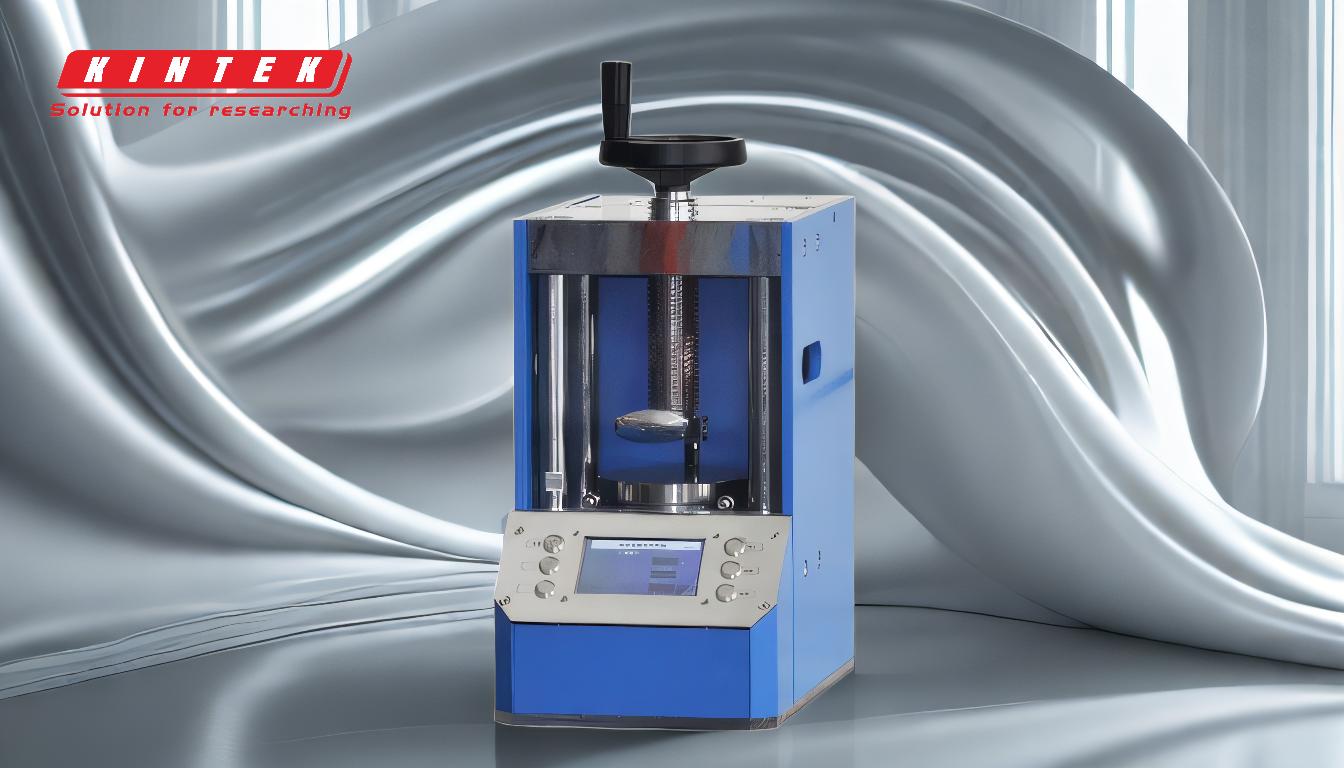
-
Understand Product Requirements:
- Part Design: Analyze the size, shape, and complexity of the part to be molded. This includes wall thickness, undercuts, and surface finish requirements.
- Material Selection: Determine the type of material (e.g., thermoplastics, thermosets) and its properties (e.g., viscosity, melting point) to ensure compatibility with the machine.
- Tolerances and Quality Standards: Define the precision and quality requirements for the final product.
-
Determine Clamping Force:
- Clamping force is the force required to keep the mold closed during injection. It is influenced by the projected area of the part and the injection pressure.
- Use the formula: Clamping Force = Projected Area × Injection Pressure.
- Select a machine with sufficient clamping force to prevent mold flash and ensure part integrity.
-
Calculate Shot Size:
- Shot size refers to the maximum volume of material the machine can inject in one cycle.
- Ensure the machine’s shot size is at least 20-30% larger than the part volume to account for material shrinkage and variations.
-
Evaluate Injection Pressure and Speed:
- Injection pressure is critical for filling the mold cavity, especially for complex geometries or high-viscosity materials.
- Injection speed affects the flow of material and the surface finish of the part.
- Match the machine’s pressure and speed capabilities with the material and part requirements.
-
Consider Machine Size and Platen Dimensions:
- The machine must accommodate the mold size and provide adequate space for mold installation and removal.
- Check the platen dimensions, tie-bar spacing, and mold height to ensure compatibility.
-
Assess Production Volume and Cycle Time:
- Determine the required production rate and cycle time to meet production goals.
- High-volume production may require machines with faster cycle times and automation features.
-
Energy Efficiency and Operational Costs:
- Evaluate the machine’s energy consumption and operational efficiency to minimize long-term costs.
- Look for features like servo-driven hydraulics or all-electric machines for improved energy efficiency.
-
Automation and Integration:
- Consider the need for automation, such as robotic part removal, conveyors, or in-mold labeling.
- Ensure the machine supports integration with auxiliary equipment and control systems.
-
Maintenance and Support:
- Assess the machine’s maintenance requirements and availability of spare parts.
- Choose a supplier with reliable technical support and service options.
-
Budget and ROI Considerations:
- Balance the initial investment with the expected return on investment (ROI) based on production efficiency and part quality.
- Consider long-term operational savings and potential for future scalability.
By systematically addressing these factors, you can specify an injection molding machine that aligns with your production needs, material requirements, and budget constraints, ensuring optimal performance and reliability.
Summary Table:
Key Factor | Description |
---|---|
Product Requirements | Analyze part design, material properties, and quality standards. |
Clamping Force | Calculate using Projected Area × Injection Pressure to prevent mold flash. |
Shot Size | Ensure it’s 20-30% larger than part volume to account for shrinkage. |
Injection Pressure & Speed | Match with material and part requirements for proper mold filling. |
Machine Size | Check platen dimensions and tie-bar spacing for mold compatibility. |
Production Volume | Assess cycle time and automation needs for high-volume production. |
Energy Efficiency | Opt for servo-driven hydraulics or all-electric machines to reduce costs. |
Automation | Consider robotic part removal and integration with auxiliary equipment. |
Maintenance | Evaluate maintenance requirements and supplier support options. |
Budget & ROI | Balance initial investment with long-term operational savings and scalability. |
Ready to find the perfect injection molding machine for your needs? Contact our experts today for personalized guidance!