A vacuum heater, often used in vacuum furnaces, operates by creating a vacuum environment to eliminate air and gases, preventing oxidation and contamination. The heating element inside the chamber heats the product under controlled conditions, with temperature regulation systems ensuring precise heating and holding times. The vacuum is maintained using a pumping system, and heat transfer occurs through phase changes of a medium like water, which absorbs heat, evaporates, and condenses in a continuous cycle. This setup ensures efficient, contamination-free heating, making it ideal for sensitive materials and processes.
Key Points Explained:
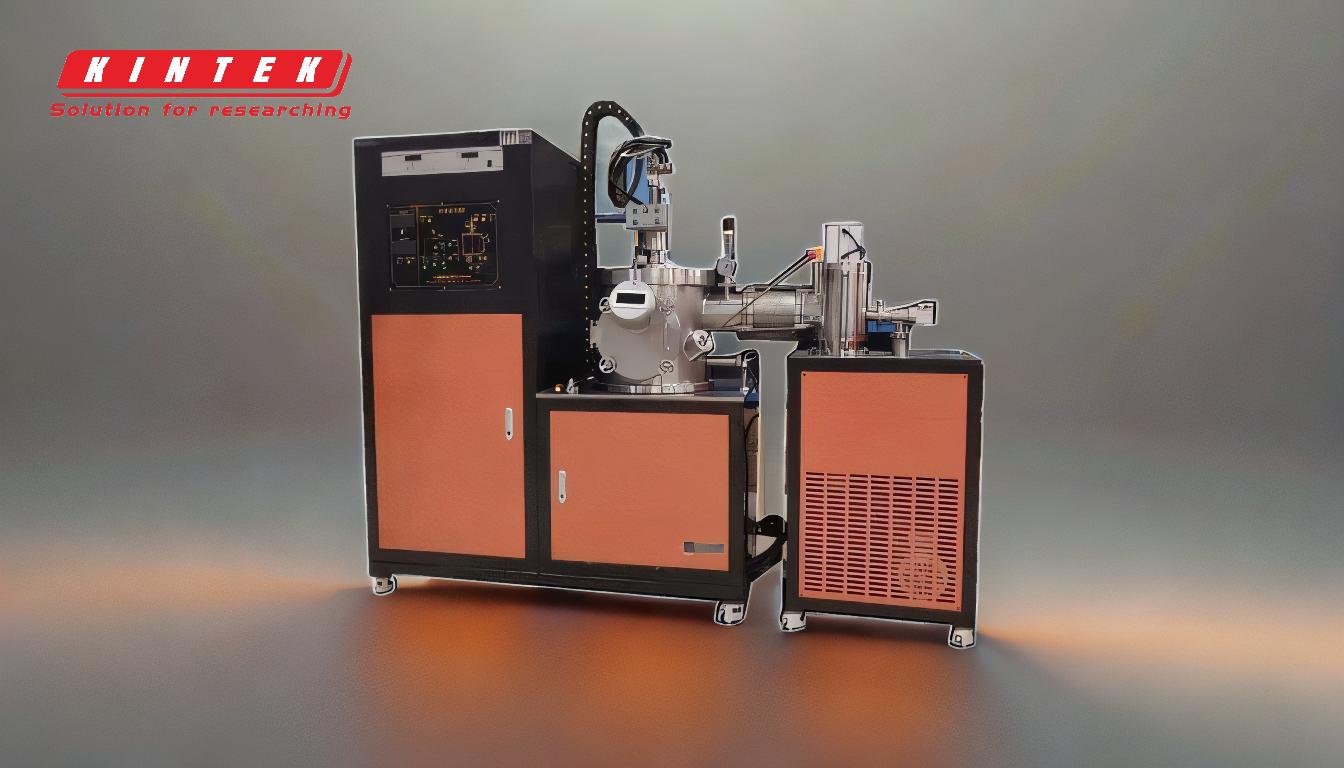
-
Vacuum Environment Creation:
- A vacuum furnace removes air and gases from the chamber using a vacuum system. This creates a controlled environment free from oxidation and contamination, which is crucial for processes involving sensitive materials.
- The absence of air also minimizes heat loss through convection, ensuring more efficient and uniform heating.
-
Heating Mechanism:
- Inside the vacuum chamber, a heating element (such as a heater, heating tape, or silicone surface heater) is used to heat the product.
- The heating element can reach high temperatures, with some systems capable of handling up to 593°C (1,100°F), depending on the application.
- The temperature control system regulates the heating speed and holding time, ensuring precise thermal treatment.
-
Heat Transfer Process:
- In some vacuum furnaces, heat transfer occurs through the phase change of a medium like water. The water absorbs heat from the combustion process, evaporates, and then condenses, releasing heat to the product.
- This phase change process is continuous, with the condensate flowing back to absorb more heat, ensuring consistent and efficient heat transfer.
-
Insulation and Safety:
- Insulation is applied to the heating elements to maintain a touch-safe temperature on the outer surfaces, typically around 48-60°C (120-140°F).
- This ensures safety for operators while maintaining high internal temperatures required for processing.
-
Applications and Benefits:
- Vacuum heaters are used in various industries, including metallurgy, electronics, and materials science, where contamination-free and precise heating is essential.
- The vacuum environment prevents oxidation, reduces contamination, and ensures uniform heating, making it ideal for processes like annealing, brazing, and sintering.
By combining these elements, a vacuum heater provides a controlled, efficient, and contamination-free environment for heating and treating materials, making it a critical tool in many industrial and scientific applications.
Summary Table:
Key Feature | Description |
---|---|
Vacuum Environment Creation | Removes air and gases to prevent oxidation and contamination, ensuring uniform heating. |
Heating Mechanism | Uses heating elements to reach high temperatures (up to 593°C) with precise control. |
Heat Transfer Process | Employs phase change of water for efficient and continuous heat transfer. |
Insulation and Safety | Maintains touch-safe outer surfaces (48-60°C) while achieving high internal temps. |
Applications and Benefits | Ideal for annealing, brazing, and sintering in industries like metallurgy and electronics. |
Discover how a vacuum heater can enhance your processes—contact us today for expert guidance!