A vacuum press works by creating a controlled environment where materials are subjected to pressure and, in some cases, heat, within a vacuum. This process is used to densify materials, improve their properties, or facilitate chemical reactions. The vacuum environment removes air and other gases, preventing oxidation and contamination, while the applied pressure ensures uniform compaction. There are various types of vacuum presses, ranging from simple systems using sealable bags and vacuum generators to more complex setups like vacuum hot press furnaces that combine high temperature and pressure. The process is widely used in industries such as materials science, manufacturing, and woodworking.
Key Points Explained:
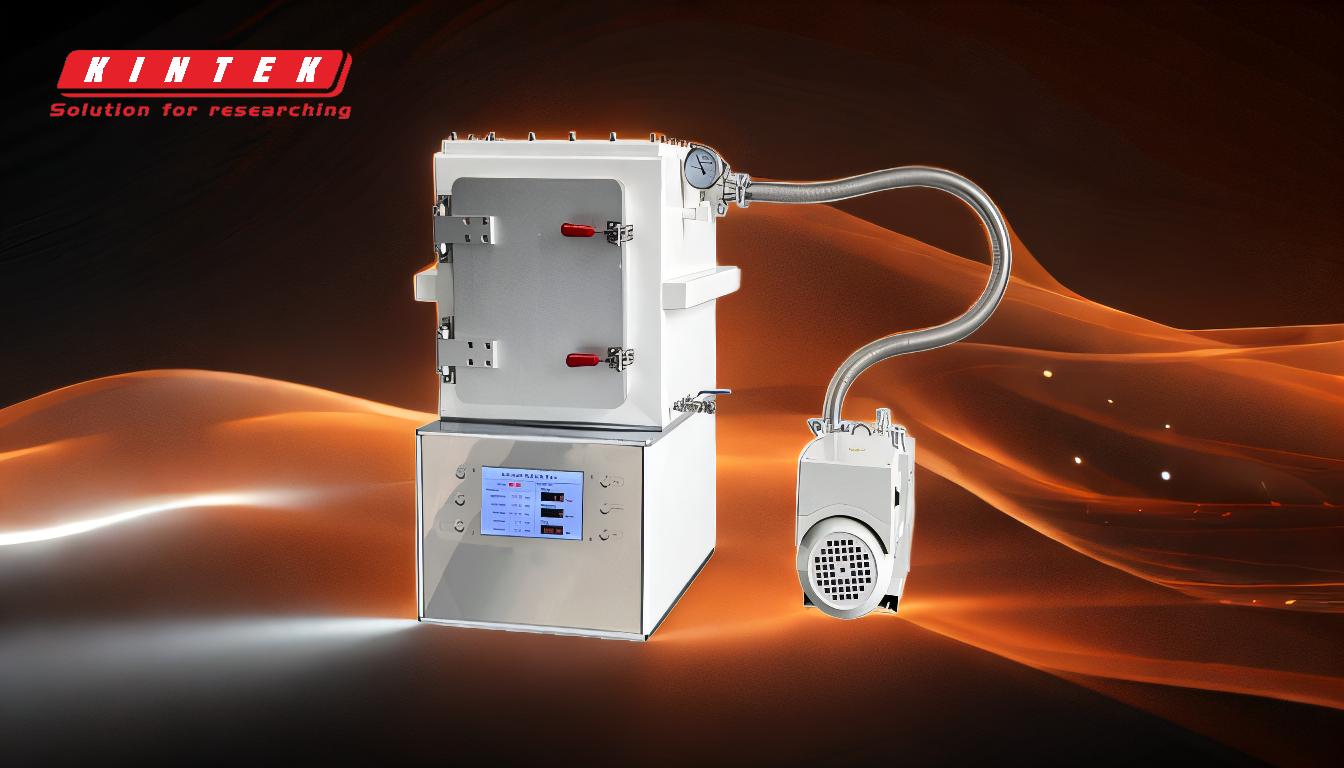
-
Basic Principle of a Vacuum Press:
- A vacuum press operates by creating a pressure differential between the inside of a sealed environment (such as a bag or chamber) and the external atmosphere.
- This is achieved by removing air and other gases from the sealed environment using a vacuum generator, which creates a low-pressure zone inside.
- The pressure differential compresses the materials placed inside, ensuring uniform densification or shaping.
-
Types of Vacuum Presses:
-
Simple Vacuum Press:
- Uses a sealable bag and a vacuum generator (e.g., a vacuum pump).
- Materials are placed inside the bag, which is then sealed and evacuated to create a vacuum.
- Commonly used in woodworking, laminating, and composite material fabrication.
-
Vacuum Hot Press:
- Combines vacuum technology with heat and pressure.
- Materials are placed in a vacuum chamber, and heat and pressure are applied simultaneously.
- Used for sintering, phase transformation, and solid-phase reactions in materials science.
-
Vacuum Hot Press Furnace:
- A more advanced system that integrates high-temperature heating with vacuum and pressure.
- Ideal for processes requiring precise control over temperature, pressure, and atmosphere, such as in the production of advanced ceramics or metal alloys.
-
Simple Vacuum Press:
-
Key Components of a Vacuum Press:
-
Vacuum Chamber or Bag:
- The sealed environment where materials are placed.
- Must be airtight to maintain the vacuum.
-
Vacuum Generator:
- A device (e.g., vacuum pump) that removes air and gases from the chamber or bag.
-
Heating System (for hot press):
- Provides the necessary heat for processes like sintering or curing.
-
Pressure Mechanism:
- Applies uniform pressure to the materials, often through hydraulic or mechanical systems.
-
Control Systems:
- Regulate temperature, pressure, and vacuum levels to ensure precision and repeatability.
-
Vacuum Chamber or Bag:
-
Applications of Vacuum Presses:
-
Material Densification:
- Used to compact powders or porous materials into solid forms with improved mechanical properties.
-
Composite Manufacturing:
- Ensures proper bonding and elimination of air pockets in composite materials.
-
Woodworking:
- Used for laminating veneers or bending wood without cracking.
-
Advanced Materials Processing:
- Essential for producing high-performance materials like ceramics, metals, and polymers with specific properties.
-
Material Densification:
-
Advantages of Using a Vacuum Press:
-
Oxidation Prevention:
- The vacuum environment eliminates oxygen, preventing oxidation and contamination of materials.
-
Uniform Pressure Distribution:
- Ensures even compaction or bonding, leading to consistent material properties.
-
Enhanced Material Properties:
- Processes like sintering and phase transformation improve density, strength, and durability.
-
Versatility:
- Can be adapted for a wide range of materials and applications.
-
Oxidation Prevention:
-
Operational Steps in a Vacuum Press:
-
Preparation:
- Place materials inside the vacuum chamber or bag.
-
Sealing:
- Ensure the chamber or bag is airtight to maintain the vacuum.
-
Evacuation:
- Activate the vacuum generator to remove air and gases.
-
Application of Pressure and Heat (if applicable):
- Apply pressure and, in the case of a hot press, heat to the materials.
-
Cooling and Release:
- Allow the materials to cool (if heated) before releasing the vacuum and removing the finished product.
-
Preparation:
-
Considerations for Equipment Selection:
-
Material Requirements:
- Choose a vacuum press that meets the specific temperature, pressure, and vacuum needs of the materials being processed.
-
Size and Capacity:
- Ensure the chamber or bag is large enough to accommodate the materials.
-
Control Precision:
- For advanced applications, opt for systems with precise control over process parameters.
-
Maintenance and Durability:
- Select equipment designed for long-term use and ease of maintenance.
-
Material Requirements:
By understanding these key points, a purchaser can make informed decisions about the type of vacuum press needed for their specific application, ensuring optimal performance and results.
Summary Table:
Aspect | Details |
---|---|
Basic Principle | Creates a pressure differential to compress materials uniformly. |
Types | Simple Vacuum Press, Vacuum Hot Press, Vacuum Hot Press Furnace. |
Key Components | Vacuum Chamber/Bag, Vacuum Generator, Heating System, Pressure Mechanism. |
Applications | Material densification, composite manufacturing, woodworking, advanced materials. |
Advantages | Prevents oxidation, ensures uniform pressure, enhances material properties. |
Operational Steps | Preparation, sealing, evacuation, pressure/heat application, cooling. |
Selection Considerations | Material requirements, size/capacity, control precision, maintenance. |
Discover the right vacuum press for your needs—contact our experts today!