Chemical Vapor Deposition (CVD) is a versatile and widely used technique for depositing thin films and coatings onto substrates. It involves the chemical reaction of gaseous precursors to form a solid material on a substrate surface. The process is divided into several stages, including gas diffusion, adsorption, chemical reaction, and desorption of by-products. CVD can be categorized into various types, such as low-pressure CVD, atmospheric pressure CVD, and plasma-based methods like microwave plasma chemical vapor deposition. Each method has its unique characteristics and applications, making CVD a crucial process in industries ranging from electronics to materials science.
Key Points Explained:
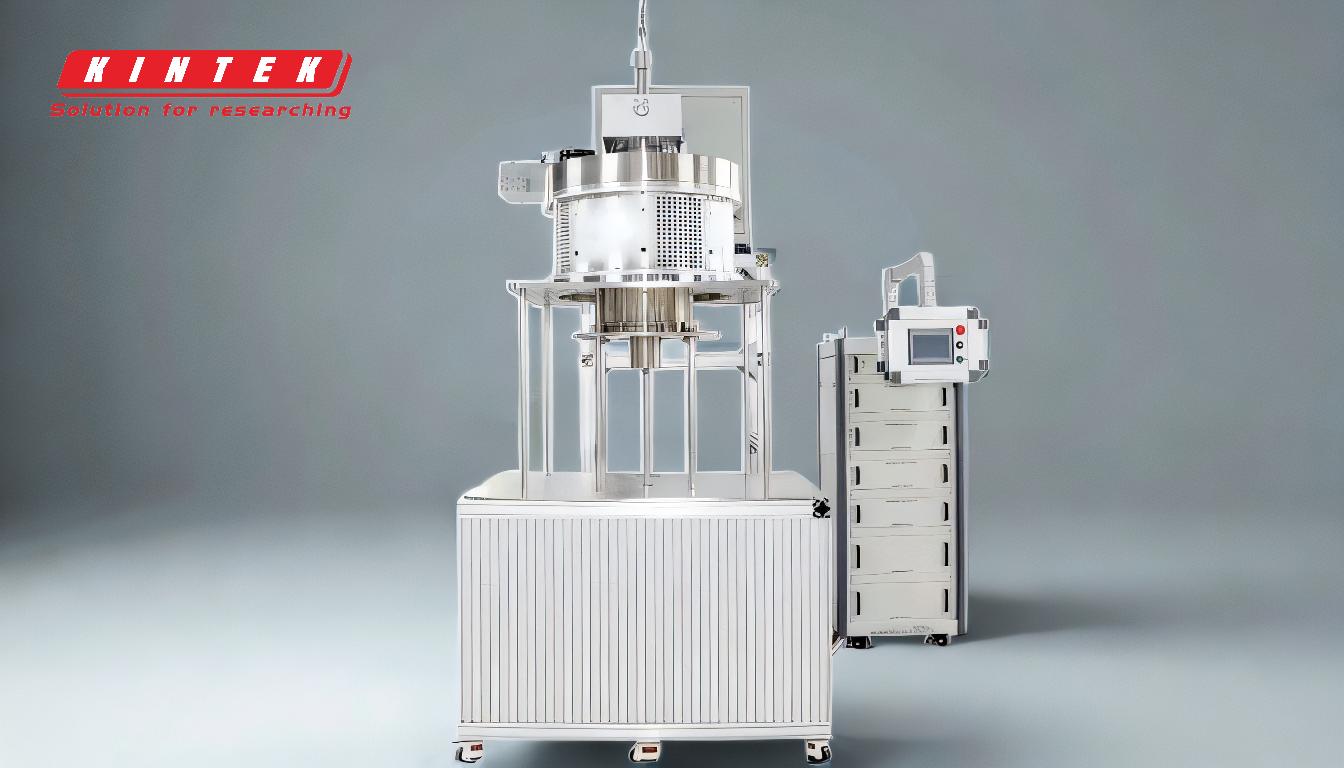
-
Basic Mechanism of CVD:
- Gas Diffusion: The reaction gases diffuse onto the substrate surface. This is the first step where the precursor gases come into contact with the substrate.
- Adsorption: The gases adsorb onto the substrate surface. This step ensures that the precursor molecules are in close proximity to the substrate for the subsequent chemical reactions.
- Chemical Reaction: The adsorbed gases undergo chemical reactions on the substrate surface, leading to the formation of a solid deposit. This is the core step where the desired material is formed.
- Desorption: The by-products of the reaction are desorbed from the surface and transported away. This step ensures that the reaction site is cleared for further deposition.
-
Types of CVD:
- Low Pressure CVD (LPCVD): Operates at reduced pressures, which enhances the uniformity and quality of the deposited film. The reaction rate is limited by the surface reaction kinetics.
- Atmospheric Pressure CVD (APCVD): Conducted at atmospheric pressure, where the reaction rate is limited by mass transfer. This method is often used for high-throughput applications.
- Plasma-Based CVD: Utilizes plasma to enhance the chemical reactions. Examples include microwave plasma chemical vapor deposition, where microwaves generate plasma to facilitate the deposition process.
-
Microwave Plasma CVD:
- Process Overview: In this method, precursor gases like CH4 and H2 are introduced into a vacuum chamber. High-voltage microwaves ionize these gases, creating a plasma. The plasma interacts with the substrate, leading to the deposition of the desired material, such as diamond.
- Advantages: Enhanced reaction rates, better control over film properties, and the ability to deposit high-quality materials like diamond at relatively low temperatures.
-
Applications of CVD:
- Electronics: CVD is extensively used in the semiconductor industry for depositing thin films of silicon, silicon dioxide, and other materials essential for integrated circuits.
- Optics: Used for coating lenses and mirrors with anti-reflective or protective layers.
- Materials Science: CVD is employed to create advanced materials like graphene, carbon nanotubes, and diamond films, which have unique properties beneficial for various applications.
-
Advantages and Challenges:
- Advantages: High purity and uniformity of deposited films, ability to deposit a wide range of materials, and compatibility with complex geometries.
- Challenges: High equipment and operational costs, need for precise control over process parameters, and potential safety hazards due to the use of toxic and flammable gases.
In summary, Chemical Vapor Deposition is a sophisticated and highly controlled process that plays a critical role in modern technology and materials science. Understanding its mechanisms, types, and applications is essential for leveraging its full potential in various industries.
Summary Table:
Aspect | Details |
---|---|
Process Stages | Gas Diffusion, Adsorption, Chemical Reaction, Desorption |
Types of CVD | Low Pressure CVD (LPCVD), Atmospheric Pressure CVD (APCVD), Plasma-Based CVD |
Applications | Electronics, Optics, Materials Science |
Advantages | High purity, uniform films, versatile material deposition |
Challenges | High costs, precise control needed, safety risks |
Ready to explore how CVD can revolutionize your processes? Contact our experts today!