Evaporation deposition is a physical vapor deposition (PVD) technique used to create thin films by evaporating a material in a vacuum environment and allowing it to condense on a substrate. This process involves heating the source material until it vaporizes, forming a vapor cloud that travels through the vacuum chamber and deposits onto the substrate surface. The method is widely used in industries such as microelectronics, optics, and coatings due to its ability to produce high-purity, uniform films. The process is controlled by parameters like temperature, vacuum pressure, and deposition rate, ensuring precise film thickness and quality.
Key Points Explained:
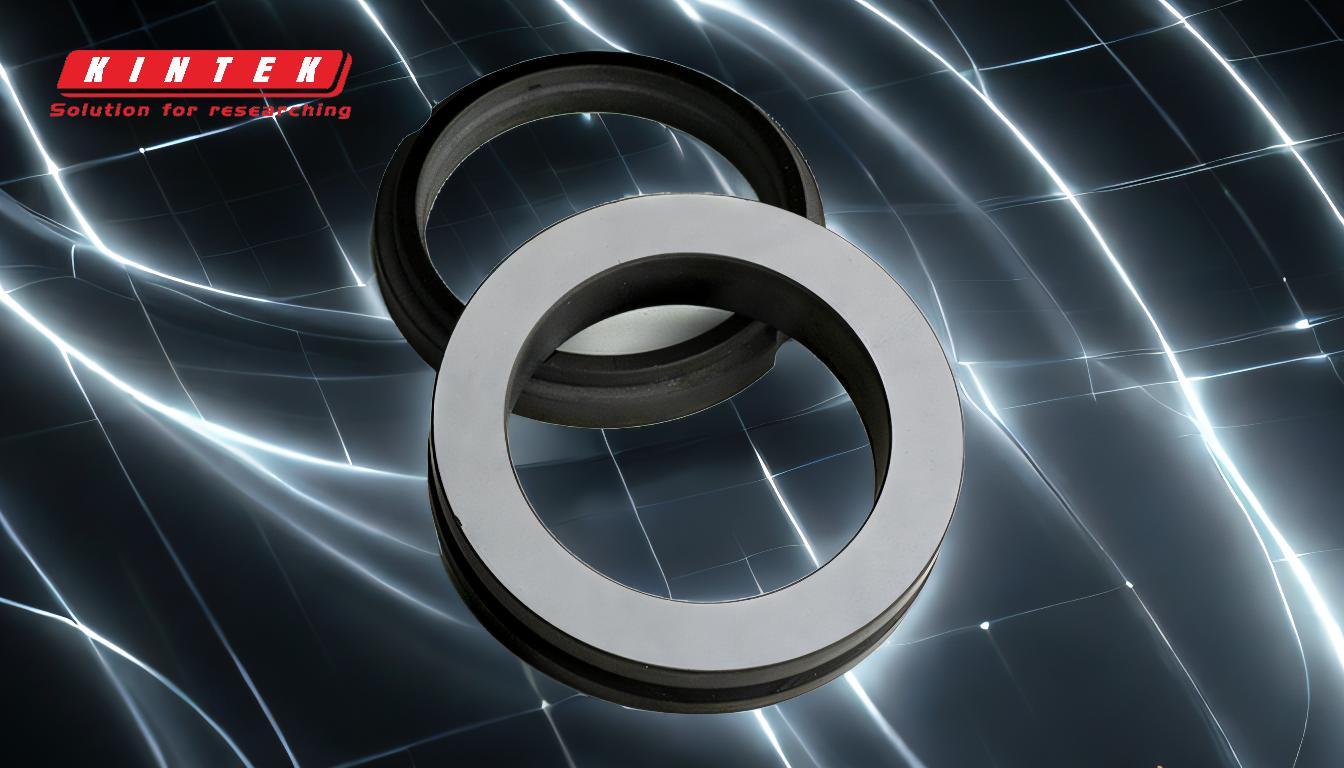
-
Basic Principle of Evaporation Deposition:
- Evaporation deposition works on the principle of heating a solid material until it transitions into a vapor phase. This vapor then travels through a vacuum and condenses on a cooler substrate, forming a thin film.
- The vacuum environment is crucial as it minimizes contamination and allows the vapor to travel unimpeded to the substrate.
-
Components of the Evaporation Deposition System:
- Vacuum Chamber: A sealed environment where the process occurs, maintaining low pressure to ensure minimal interference from air molecules.
- Evaporation Source: The material to be deposited is heated using methods like resistive heating, electron beam heating, or induction heating.
- Substrate Holder: Holds the substrate in place and often rotates or moves to ensure uniform deposition.
- Vacuum Pump: Maintains the low-pressure environment necessary for the process.
-
Types of Evaporation Techniques:
- Resistive Heating: The source material is heated by passing an electric current through a resistive element. This method is simple but limited to materials with lower melting points.
- Electron Beam Evaporation: A focused beam of high-energy electrons heats the source material, allowing for the evaporation of high-melting-point materials.
- Induction Heating: Uses electromagnetic induction to heat the source material, suitable for conductive materials.
-
Advantages of Evaporation Deposition:
- High Purity: The vacuum environment reduces contamination, resulting in high-purity films.
- Uniformity: Precise control over deposition parameters ensures uniform film thickness.
- Versatility: Can deposit a wide range of materials, including metals, alloys, and compounds.
- Scalability: Suitable for both small-scale research and large-scale industrial production.
-
Applications of Evaporation Deposition:
- Microelectronics: Used to deposit thin films for semiconductors, integrated circuits, and sensors.
- Optics: Creates anti-reflective coatings, mirrors, and optical filters.
- Coatings: Produces protective and decorative coatings on various substrates.
- Solar Cells: Deposits thin films for photovoltaic applications.
-
Challenges and Limitations:
- Material Limitations: Some materials may decompose or react before evaporating.
- Line-of-Sight Deposition: The process is directional, making it difficult to coat complex geometries uniformly.
- High Equipment Cost: The need for vacuum systems and specialized heating methods increases initial investment.
-
Future Trends and Innovations:
- Hybrid Techniques: Combining evaporation deposition with other PVD methods to enhance film properties.
- Advanced Substrate Manipulation: Developing new substrate holders and motion systems to improve coating uniformity on complex shapes.
- Green Technologies: Exploring eco-friendly materials and energy-efficient heating methods to reduce environmental impact.
In summary, evaporation deposition is a versatile and precise method for creating thin films, offering high purity and uniformity. While it has some limitations, ongoing advancements continue to expand its applications and improve its efficiency.
Summary Table:
Aspect | Details |
---|---|
Basic Principle | Heating a solid material to vapor phase, condensing it on a substrate. |
Key Components | Vacuum chamber, evaporation source, substrate holder, vacuum pump. |
Types of Techniques | Resistive heating, electron beam evaporation, induction heating. |
Advantages | High purity, uniformity, versatility, scalability. |
Applications | Microelectronics, optics, coatings, solar cells. |
Challenges | Material limitations, line-of-sight deposition, high equipment cost. |
Future Trends | Hybrid techniques, advanced substrate manipulation, green technologies. |
Discover how evaporation deposition can enhance your thin film processes—contact our experts today!