Extrusion is a manufacturing process used to create objects of a fixed cross-sectional profile by pushing material through a die. It is widely used in industries such as plastic manufacturing, food processing, and metalworking. The process involves several key steps, starting with feeding raw material (e.g., plastic pellets) into a hopper, melting it in a heating chamber, and then forcing it through a die to shape the final product. Below is a detailed explanation of how extrusion works step by step.
Key Points Explained:
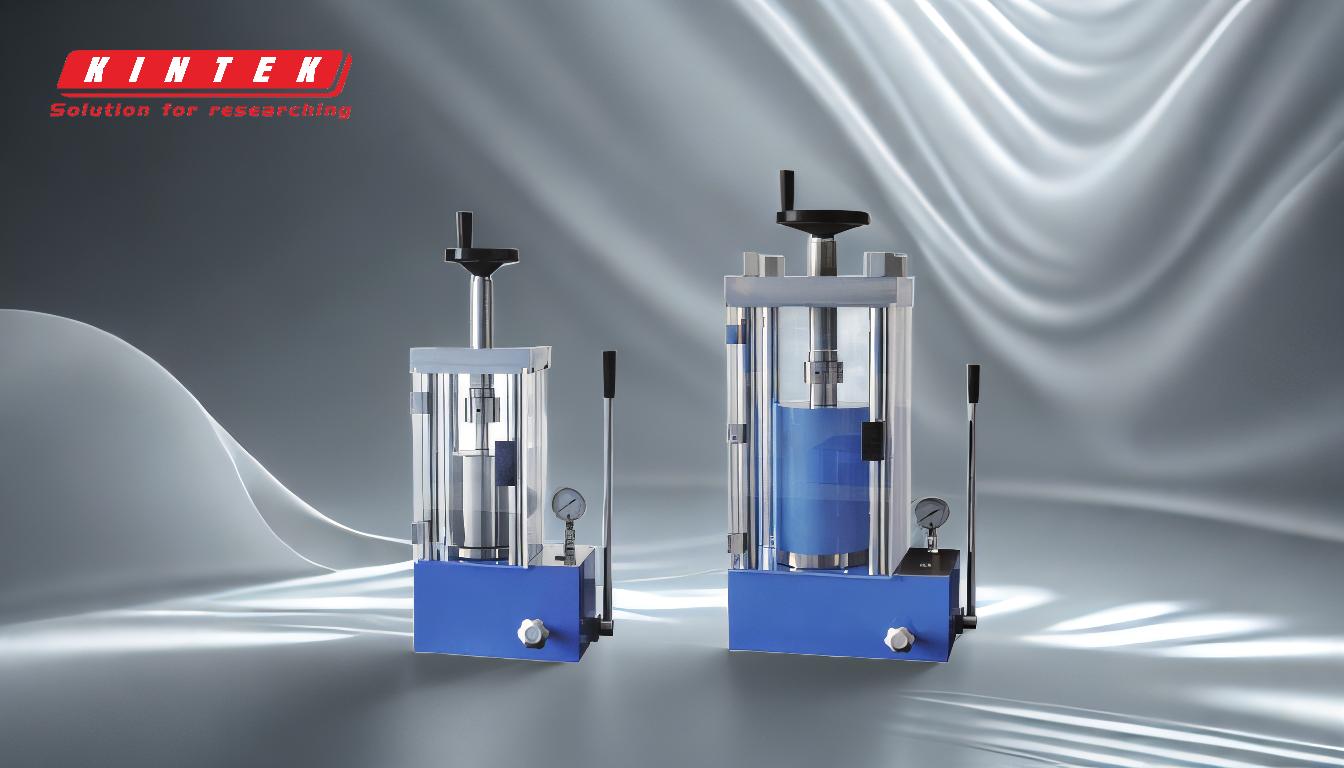
-
Feeding Raw Material into the Hopper
- The process begins with the raw material, typically in the form of pellets, granules, or powder, being fed into a hopper.
- The hopper acts as a reservoir, ensuring a consistent supply of material to the extrusion system.
- This step is critical for maintaining a steady flow of material, which is essential for producing uniform products.
-
Transporting Material to the Heating Chamber
- From the hopper, the material is transported to the heating chamber using a screw mechanism or conveyor system.
- The screw mechanism, often referred to as an extruder screw, rotates and pushes the material forward while also mixing it to ensure uniformity.
- This step ensures that the material is evenly distributed and prepared for the melting process.
-
Melting the Material in the Heating Chamber
- Once the material reaches the heating chamber, it is subjected to high temperatures, causing it to melt and transform into a molten state.
- The heating chamber is equipped with heating circulator elements and temperature controls to maintain precise melting conditions.
- The molten material must reach a specific viscosity to ensure it can flow smoothly through the die.
-
Forcing the Molten Material Through the Die
- After melting, the material is forced through a die, which is a specialized tool that shapes the molten material into the desired cross-sectional profile.
- The die determines the final shape and dimensions of the extruded product, such as pipes, sheets, or profiles.
- The pressure applied by the extruder screw ensures that the material flows evenly through the die.
-
Cooling and Solidifying the Extruded Product
- As the material exits the die, it begins to cool and solidify, retaining the shape imparted by the die.
- Cooling can be achieved through air cooling, cooling circulator baths, or other methods, depending on the material and product requirements.
- Proper cooling is essential to prevent deformation and ensure the product maintains its structural integrity.
-
Cutting or Finishing the Final Product
- Once the extruded product has cooled and solidified, it is cut to the desired length or subjected to additional finishing processes.
- Finishing processes may include surface treatment, printing, or assembly, depending on the application.
- This step ensures the final product meets the required specifications and is ready for use or further processing.
By following these steps, extrusion enables the efficient production of a wide range of products with consistent quality and precision. The process is highly adaptable, making it suitable for various materials and applications.
Summary Table:
Step | Description |
---|---|
Feeding Raw Material | Raw material (pellets, granules, powder) is fed into a hopper for consistent supply. |
Transporting Material | Material is moved to the heating chamber via a screw mechanism for uniformity. |
Melting Material | Material is melted in the heating chamber to achieve the right viscosity. |
Forcing Through Die | Molten material is pushed through a die to shape the final product. |
Cooling and Solidifying | The extruded product is cooled to retain its shape and structural integrity. |
Cutting or Finishing | Final product is cut or finished to meet specifications. |
Discover how extrusion can transform your manufacturing process—contact our experts today!