Physical vapor deposition (PVD) is a process used to deposit thin films of material onto a substrate. Unlike chemical vapor deposition (CVD), which relies on chemical reactions to form the film, PVD is a physical process that involves the transfer of material at an atomic or molecular level. The key mechanisms in PVD include sputtering, evaporation, and condensation. Sputtering, for instance, involves bombarding a target material with high-energy particles, causing atoms to be ejected and deposited onto a substrate. This process is widely used in industries such as semiconductors, optics, and coatings due to its ability to produce high-quality, uniform films with precise control over thickness and composition.
Key Points Explained:
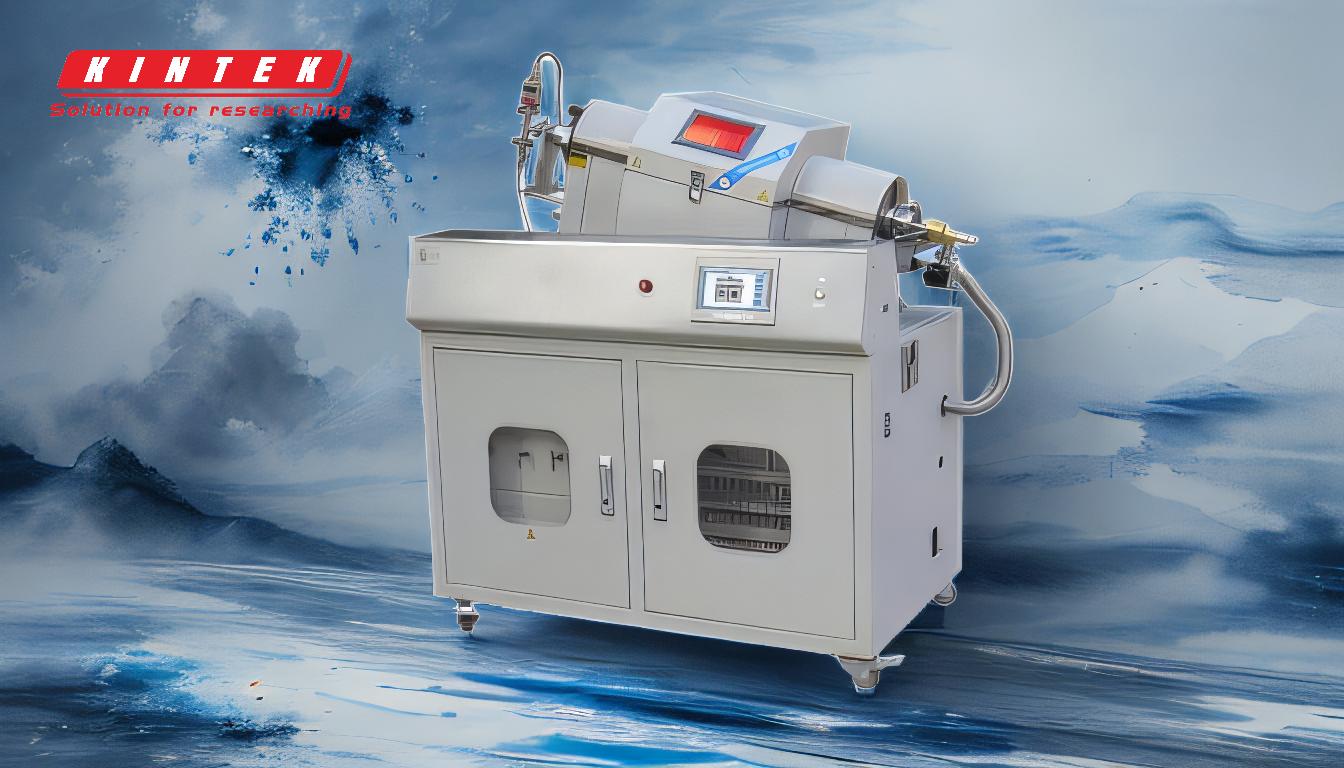
-
Definition and Overview of Physical Vapor Deposition (PVD):
- PVD is a vacuum-based process that deposits thin films of material onto a substrate through physical means, such as sputtering or evaporation.
- Unlike chemical vapor deposition (CVD), PVD does not rely on chemical reactions but instead uses physical processes to transfer material from a source to a substrate.
-
Key Mechanisms in PVD:
- Sputtering: This is one of the primary mechanisms in PVD. It involves bombarding a target material with high-energy particles (usually ions of an inert gas like argon). When these particles strike the target, they dislodge atoms from its surface, which then travel through the vacuum and deposit onto the substrate.
- Evaporation: In this process, the target material is heated to a high temperature, causing it to evaporate. The vaporized material then condenses on the cooler substrate, forming a thin film.
- Condensation: After the material is ejected from the target (via sputtering or evaporation), it travels through the vacuum chamber and condenses on the substrate, forming a thin, uniform layer.
-
Steps Involved in the PVD Process:
- Preparation of the Substrate: The substrate is cleaned and prepared to ensure proper adhesion of the deposited film.
- Creation of a Vacuum: The process takes place in a vacuum chamber to prevent contamination and ensure that the ejected material can travel freely to the substrate.
- Ejection of Material: Depending on the PVD technique used (sputtering or evaporation), the target material is either bombarded with high-energy particles or heated until it evaporates.
- Deposition of Material: The ejected material travels through the vacuum and deposits onto the substrate, forming a thin film.
- Film Growth and Nucleation: The deposited atoms or molecules nucleate and grow into a continuous film on the substrate.
-
Applications of PVD:
- Semiconductors: PVD is used to deposit thin films of metals and dielectrics in the fabrication of semiconductor devices.
- Optics: PVD is employed to create reflective and anti-reflective coatings on lenses and mirrors.
- Coatings: PVD is widely used to apply hard, wear-resistant coatings on tools and components in industries such as automotive and aerospace.
-
Advantages of PVD:
- High-Quality Films: PVD produces films with excellent adhesion, uniformity, and purity.
- Precision Control: The process allows for precise control over film thickness and composition.
- Versatility: PVD can be used with a wide range of materials, including metals, ceramics, and composites.
-
Comparison with Chemical Vapor Deposition (CVD):
- Process Differences: While PVD relies on physical processes like sputtering and evaporation, CVD involves chemical reactions to deposit material onto the substrate.
- Temperature Requirements: PVD typically operates at lower temperatures compared to CVD, making it suitable for substrates that are sensitive to high temperatures.
- Film Properties: PVD films tend to have better adhesion and lower stress compared to CVD films, but CVD can produce films with more complex compositions and structures.
In summary, physical vapor deposition is a versatile and precise method for depositing thin films onto substrates. It operates through physical processes like sputtering and evaporation, making it distinct from chemical vapor deposition. PVD is widely used in various industries due to its ability to produce high-quality, uniform films with excellent control over thickness and composition.
Summary Table:
Key Aspect | Details |
---|---|
Definition | A vacuum-based process for depositing thin films using physical mechanisms. |
Key Mechanisms | Sputtering, evaporation, and condensation. |
Steps | Substrate preparation, vacuum creation, material ejection, deposition. |
Applications | Semiconductors, optics, coatings (e.g., automotive, aerospace). |
Advantages | High-quality films, precise control, versatility. |
Comparison with CVD | Lower temperatures, better adhesion, simpler processes. |
Discover how PVD can enhance your applications—contact our experts today!