Pressure has a significant impact on porosity, particularly in porous materials like rocks or manufactured materials such as ceramics or foams. When external pressure is applied, the material undergoes compression, leading to a reduction in pore spaces. This relationship is critical in fields such as geophysics, material science, and engineering, where understanding how pressure affects porosity can influence material selection, design, and performance. The provided reference highlights the inverse relationship between compressional wave velocity and porosity, emphasizing that increased pressure reduces porosity, which in turn increases wave velocity. Below, we explore this relationship in detail.
Key Points Explained:
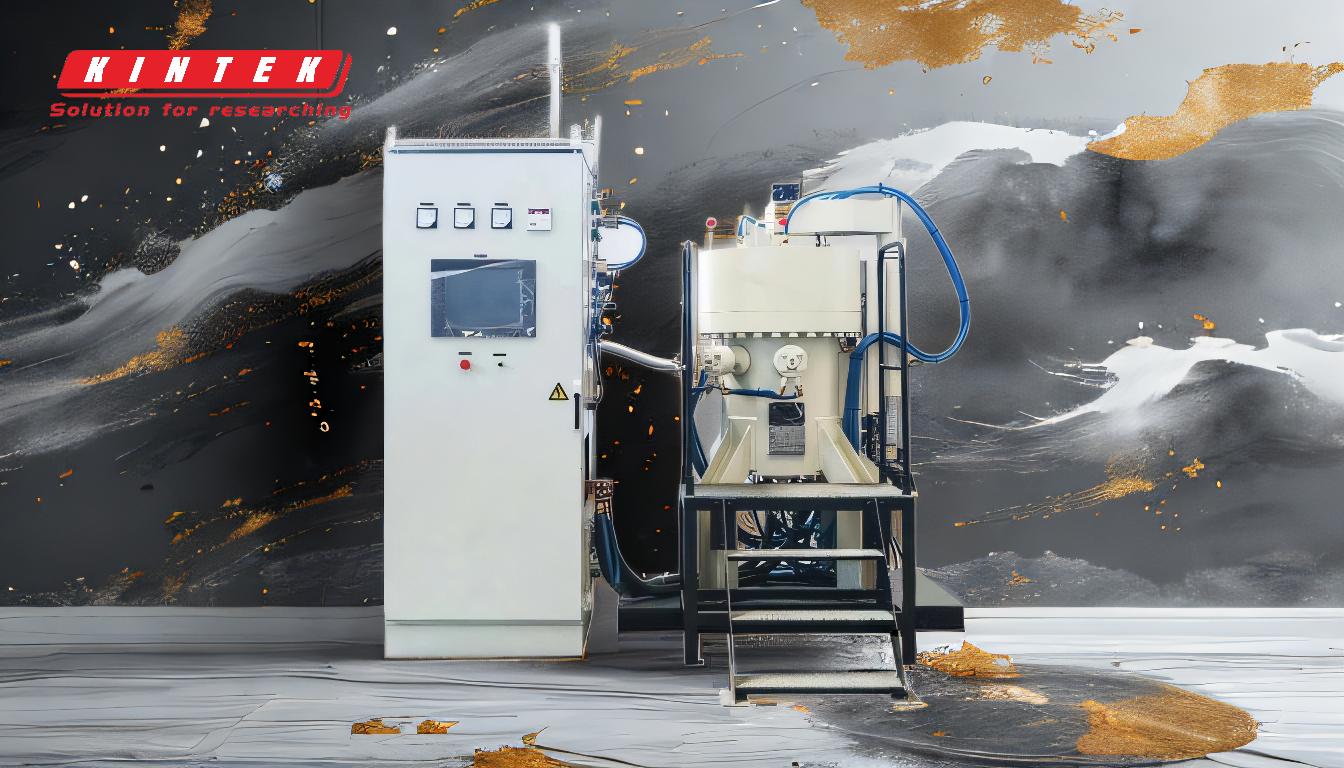
-
Definition of Porosity and Pressure
- Porosity refers to the fraction of void spaces (pores) within a material relative to its total volume. It is a critical property in determining the material's ability to store fluids or gases.
- Pressure is the force applied per unit area. In the context of porosity, pressure can be external (e.g., overburden pressure in rocks) or internal (e.g., fluid pressure within pores).
-
Pressure-Compaction Relationship
- When pressure is applied to a porous material, the material compacts. This compaction reduces the volume of pore spaces, leading to a decrease in porosity.
- The extent of porosity reduction depends on the material's compressibility. For example, soft or highly porous materials (e.g., foams) experience more significant porosity reduction under pressure compared to rigid materials (e.g., dense ceramics).
-
Inverse Relationship Between Porosity and Compressional Wave Velocity
- Compressional wave velocity is a measure of how quickly pressure waves travel through a material. It is influenced by the material's density and elastic properties.
- As porosity decreases under pressure, the material becomes denser and more rigid. This increases the speed at which compressional waves travel through the material.
- The reference explicitly states that compressional wave velocity is inversely proportional to porosity, meaning that as porosity decreases, wave velocity increases.
-
Practical Implications of Pressure-Porosity Relationship
- In geophysics, understanding how pressure affects porosity helps in interpreting seismic data. For example, in oil and gas exploration, changes in porosity due to overburden pressure can influence reservoir properties.
- In material science, controlling porosity under pressure is essential for designing materials with specific mechanical and thermal properties. For instance, in ceramic manufacturing, adjusting pressure during sintering can optimize porosity for applications like filtration or insulation.
- In engineering, the pressure-porosity relationship is critical for designing structures that can withstand compressive forces without losing functionality (e.g., porous pavements or lightweight composites).
-
Factors Influencing the Pressure-Porosity Relationship
- Material Composition: Different materials have varying responses to pressure. For example, clays are more compressible than sandstones.
- Pore Geometry: The shape and connectivity of pores affect how easily they collapse under pressure.
- Fluid Presence: Fluids within pores can resist compression, altering the pressure-porosity relationship. For instance, water-saturated materials may exhibit less porosity reduction under pressure compared to dry materials.
-
Mathematical Modeling of Pressure and Porosity
- The relationship between pressure and porosity can be described using mathematical models, such as the effective stress principle. This principle states that the effective stress (σ') acting on a porous material is the difference between the total stress (σ) and the pore pressure (P):
[ \sigma' = \sigma - P ] - As effective stress increases (due to higher external pressure or lower pore pressure), porosity decreases. This relationship is often represented empirically using equations like the Terzaghi equation or Kozeny-Carman equation, which relate porosity to pressure and material properties.
- The relationship between pressure and porosity can be described using mathematical models, such as the effective stress principle. This principle states that the effective stress (σ') acting on a porous material is the difference between the total stress (σ) and the pore pressure (P):
-
Experimental Observations
- Laboratory experiments, such as triaxial compression tests, are commonly used to study the pressure-porosity relationship. These tests involve applying controlled pressure to a sample and measuring changes in porosity and wave velocity.
- Field studies, such as seismic surveys, also provide insights into how pressure affects porosity in natural settings. For example, seismic data from deep reservoirs often show increased wave velocities due to reduced porosity under high overburden pressure.
-
Applications in Material Selection and Design
- For equipment and consumable purchasers, understanding the pressure-porosity relationship is crucial for selecting materials that meet specific performance criteria. For example:
- In filtration systems, materials with stable porosity under pressure are preferred to ensure consistent performance.
- In thermal insulation, materials with low compressibility (i.e., minimal porosity reduction under pressure) are chosen to maintain insulation properties.
- In structural applications, materials with predictable porosity changes under pressure are selected to ensure durability and safety.
- For equipment and consumable purchasers, understanding the pressure-porosity relationship is crucial for selecting materials that meet specific performance criteria. For example:
By understanding how pressure affects porosity, purchasers and engineers can make informed decisions about material selection and design, ensuring optimal performance under varying pressure conditions. This knowledge is particularly valuable in industries where materials are subjected to significant compressive forces, such as construction, energy, and manufacturing.
Summary Table:
Key Aspect | Description |
---|---|
Porosity Definition | Fraction of void spaces in a material relative to its total volume. |
Pressure Definition | Force applied per unit area, influencing material compaction. |
Pressure-Porosity Relationship | Increased pressure reduces porosity, making materials denser and more rigid. |
Wave Velocity | Compressional wave velocity increases as porosity decreases under pressure. |
Applications | Critical in geophysics, material science, and engineering for material design. |
Need help selecting materials with optimal porosity under pressure? Contact our experts today!