RF magnetron sputtering is a specialized technique used to deposit thin films, particularly for non-conductive materials, by utilizing radio frequency (RF) power and magnetic fields. This method is highly effective for insulating materials because it prevents charge build-up on the target surface, ensuring efficient ionization and deposition. The process involves creating a plasma in a vacuum chamber, where high-energy ions bombard the target material, causing its atoms to be ejected and deposited onto a substrate. Magnetic fields confine the plasma near the target, increasing ionization efficiency and deposition rates. RF magnetron sputtering is widely used in industries requiring precise and uniform thin films for optical, electrical, and other applications.
Key Points Explained:
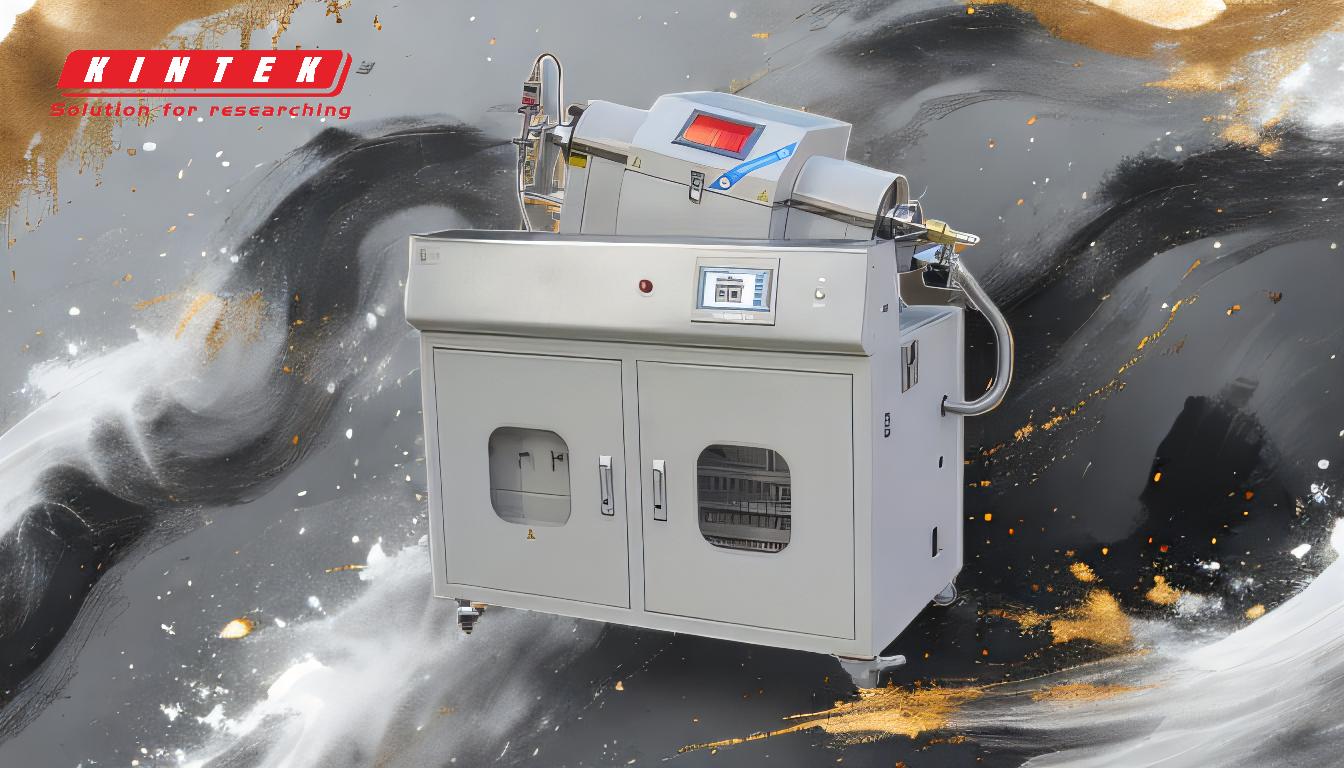
-
Mechanism of RF Magnetron Sputtering:
- RF magnetron sputtering uses radio frequency power (typically 13.56 MHz) to generate an alternating electrical potential. This alternation prevents charge accumulation on the target surface, which is crucial for sputtering non-conductive materials. During the positive cycle, electrons neutralize the target, while during the negative cycle, ion bombardment continues, ensuring a steady sputtering process.
-
Role of Magnetic Fields:
- Magnetic fields are employed to confine secondary electrons near the target material. This confinement increases the ionization of the sputtering gas (usually argon), leading to a higher density of ions available for bombardment. As a result, the deposition rate on the substrate is significantly enhanced.
-
Ion Bombardment and Sputtering:
- High-energy ions of argon gas collide with the target material's surface, transferring energy to the atoms. If the energy exceeds the binding energy of the target atoms, they are ejected from the surface. These sputtered atoms then travel through the vacuum chamber and deposit onto the substrate, forming a thin film.
-
Advantages for Non-Conductive Materials:
- RF magnetron sputtering is particularly advantageous for insulating materials. Without magnetism, non-conductive targets can become positively charged, hindering the sputtering process. The alternating RF potential and magnetic fields prevent this charge build-up, ensuring efficient and continuous deposition.
-
Applications and Uniformity:
- This technique is widely used in industries requiring precise and uniform thin films, such as optics, electronics, and coatings. The low-pressure environment and controlled sputtering process result in highly uniform films with consistent thickness, making it ideal for applications demanding high precision.
-
Comparison with DC Sputtering:
- Unlike DC sputtering, which is primarily used for conductive materials, RF magnetron sputtering can handle both conductive and non-conductive targets. The RF approach overcomes the limitations of DC sputtering by preventing charge accumulation and enabling the deposition of insulating materials.
-
Process Efficiency:
- The combination of RF power and magnetic confinement significantly improves the efficiency of the sputtering process. The increased ionization and higher deposition rates make RF magnetron sputtering a preferred method for producing high-quality thin films in industrial and research settings.
By leveraging the principles of RF power and magnetic confinement, RF magnetron sputtering provides a robust and versatile solution for thin film deposition, particularly for challenging materials like insulators. Its ability to prevent charge build-up and enhance deposition rates makes it indispensable in advanced manufacturing and research applications.
Summary Table:
Key Aspect | Description |
---|---|
Mechanism | Uses RF power (13.56 MHz) to prevent charge build-up on non-conductive targets. |
Magnetic Fields | Confines plasma near the target, enhancing ionization and deposition rates. |
Ion Bombardment | High-energy ions eject target atoms, forming a thin film on the substrate. |
Advantages for Insulators | Prevents charge accumulation, enabling efficient deposition of non-conductive materials. |
Applications | Used in optics, electronics, and coatings for precise, uniform thin films. |
Efficiency | Combines RF power and magnetic fields for high deposition rates and quality. |
Discover how RF magnetron sputtering can elevate your thin film processes—contact our experts today!