Tempering is a heat treatment process that follows hardening and plays a critical role in balancing the mechanical properties of materials, particularly steel. By reheating the material to specific temperatures, tempering transforms the brittle martensite structure formed during hardening into softer and more ductile structures like troostite or sorbite. This process regulates the hardness, toughness, and wear resistance of the material, making it more suitable for practical applications. The temperature range during tempering determines the final properties: lower temperatures (300–750°F) result in higher hardness and wear resistance, while higher temperatures (750–1290°F) enhance toughness and ductility at the expense of hardness. Understanding these effects is crucial for selecting the appropriate tempering conditions to achieve desired material performance.
Key Points Explained:
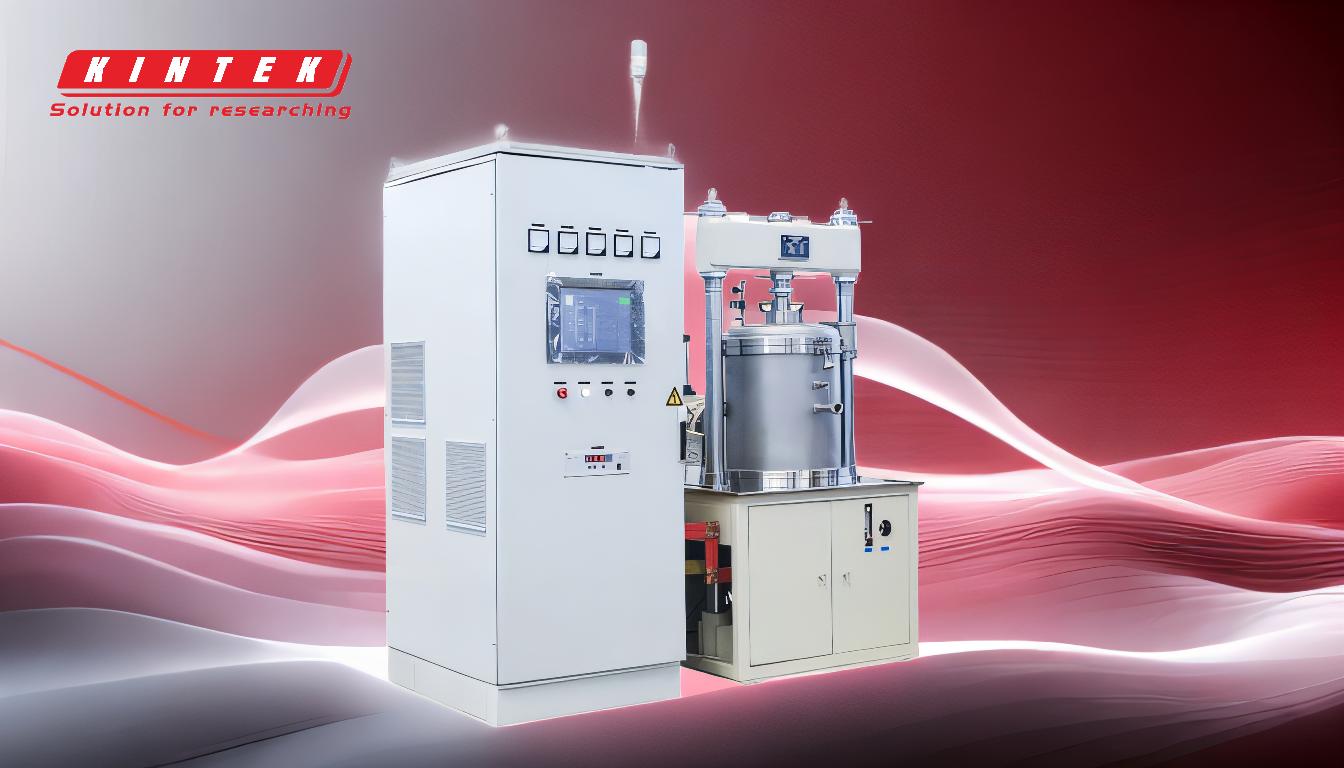
-
Purpose of Tempering:
- Tempering is a heat treatment process applied after hardening to improve the material's mechanical properties.
- It balances hardness, toughness, and wear resistance, making the material more suitable for real-world applications.
-
Structural Changes During Tempering:
- Hardening forms martensite, a hard but brittle structure.
- Tempering transforms martensite into softer and tougher structures:
- Troostite: Formed at 300–750°F, offering a balance of hardness and toughness.
- Sorbite: Formed at 750–1290°F, providing greater ductility but reduced strength compared to troostite.
-
Effect of Temperature on Hardness:
-
Lower Temperatures (300–750°F):
- Retain higher hardness and wear resistance.
- Ideal for applications requiring durability and resistance to abrasion.
-
Higher Temperatures (750–1290°F):
- Reduce hardness but significantly increase toughness and ductility.
- Suitable for components subjected to impact or stress.
-
Lower Temperatures (300–750°F):
-
Trade-offs Between Hardness and Toughness:
- Tempering allows engineers to tailor material properties by adjusting the temperature.
- Higher hardness is often accompanied by reduced toughness, and vice versa. The choice depends on the application's requirements.
-
Practical Implications for Material Selection:
- Understanding tempering effects helps in selecting the right heat treatment process for specific applications.
- For example, tools requiring high wear resistance (e.g., cutting tools) are tempered at lower temperatures, while structural components needing impact resistance (e.g., gears) are tempered at higher temperatures.
-
Importance of Tempering in Material Science:
- Tempering is essential for optimizing the performance of hardened materials.
- It ensures that materials are not excessively brittle, reducing the risk of failure under stress.
By carefully controlling the tempering process, manufacturers can achieve the desired balance of hardness, toughness, and ductility, ensuring that materials meet the specific demands of their intended applications.
Summary Table:
Aspect | Details |
---|---|
Purpose | Balances hardness, toughness, and wear resistance post-hardening. |
Temperature Ranges | - 300–750°F: Higher hardness, wear resistance. |
- 750–1290°F: Increased toughness, ductility, reduced hardness. | |
Structural Changes | Transforms brittle martensite into softer troostite or sorbite structures. |
Applications | - Low Temp: Cutting tools, wear-resistant parts. |
- High Temp: Gears, structural components requiring impact resistance. | |
Key Benefit | Tailors material properties to meet specific application demands. |
Optimize your material properties with the right tempering process—contact our experts today for tailored solutions!