The sputtering method is a physical vapor deposition (PVD) technique used to deposit thin films onto substrates. It involves bombarding a target material with high-energy ions, causing atoms to be ejected from the target's surface. These ejected atoms then travel through a vacuum chamber and deposit onto a substrate, forming a thin film. The process is highly precise and is widely used in industries such as semiconductors, optics, and coatings. The key steps include ion generation, target bombardment, atom ejection, transport through a vacuum, and deposition onto the substrate. Sputtering is favored for its ability to produce uniform, high-quality films, even on heat-sensitive materials.
Key Points Explained:
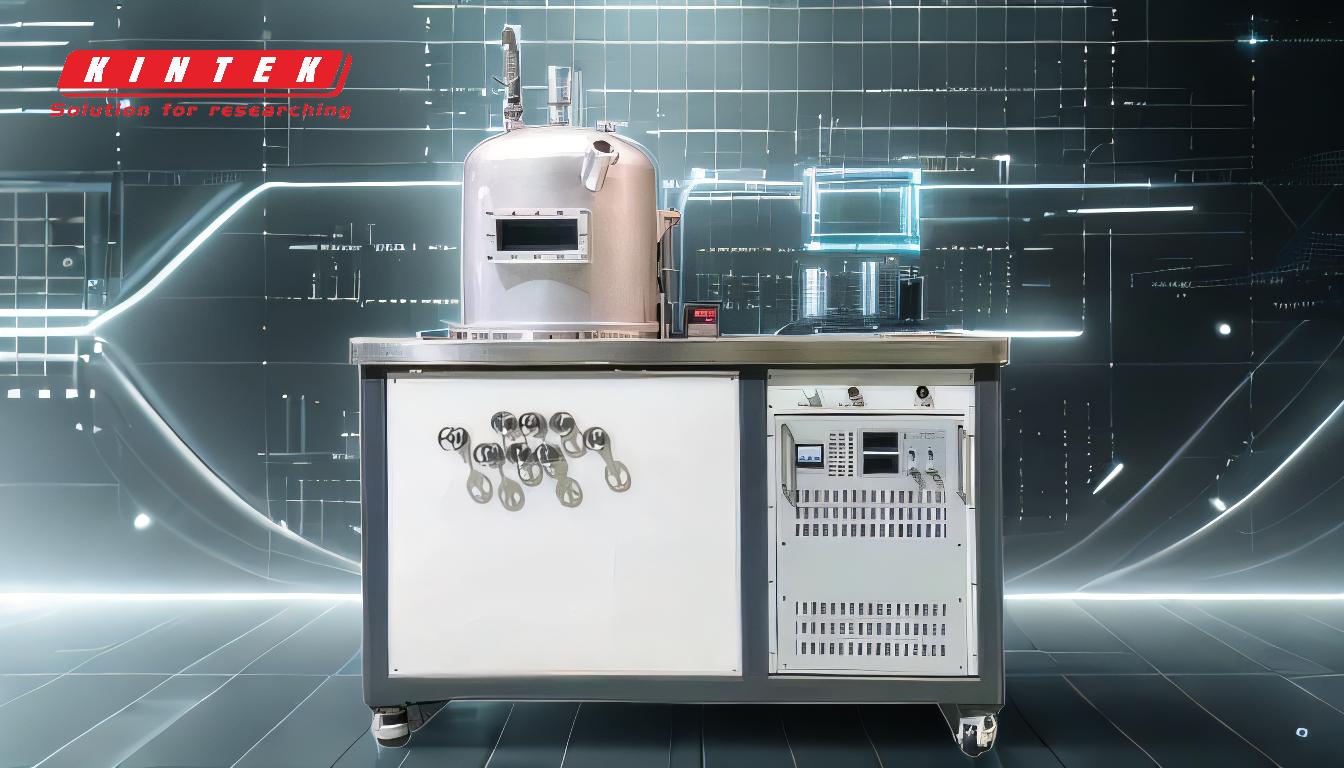
-
Ion Generation and Acceleration:
- In the sputtering process, ions are generated by ionizing a sputtering gas, typically an inert gas like argon or xenon. This ionization occurs in a plasma created within a vacuum chamber.
- A voltage is applied between the target (cathode) and the substrate (anode), accelerating the positively charged ions toward the target material.
-
Target Bombardment:
- The accelerated ions strike the target material with high kinetic energy. This energy transfer causes atoms or molecules near the surface of the target to gain enough energy to escape from the surface.
- The process of atoms being ejected from the target material is known as "sputtering."
-
Atom Ejection and Transport:
- The ejected atoms or molecules from the target material form a vapor stream. These particles travel through the vacuum chamber toward the substrate.
- The vacuum environment is crucial as it prevents interactions with air or other unwanted gases, ensuring the purity and quality of the deposited film.
-
Deposition onto Substrate:
- The sputtered atoms condense onto the substrate, forming a thin film. The substrate is typically mounted opposite the target within the vacuum chamber.
- The low temperature of the sputtered particles allows even heat-sensitive substrates, such as plastics, to be coated without damage.
-
Advantages of Sputtering:
- Precision and Uniformity: Sputtering produces highly uniform and precise thin films, making it ideal for applications requiring high accuracy, such as semiconductor manufacturing.
- Versatility: It can deposit a wide range of materials, including metals, alloys, and ceramics, onto various substrates.
- Low Temperature: The process can be performed at relatively low temperatures, enabling the coating of heat-sensitive materials.
-
Applications of Sputtering:
- Semiconductors: Used for depositing thin films in integrated circuits and other electronic components.
- Optics: Applied in the production of anti-reflective coatings, mirrors, and optical filters.
- Coatings: Utilized for wear-resistant, corrosion-resistant, and decorative coatings on various materials.
By understanding these key points, one can appreciate the efficiency and versatility of the sputtering method in producing high-quality thin films for a wide range of applications.
Summary Table:
Key Steps | Description |
---|---|
Ion Generation | Ions are generated by ionizing inert gases like argon in a plasma. |
Target Bombardment | High-energy ions strike the target, ejecting atoms from its surface. |
Atom Ejection | Ejected atoms form a vapor stream and travel through a vacuum chamber. |
Deposition | Atoms condense onto the substrate, forming a thin film. |
Advantages | Precision, uniformity, versatility, and low-temperature processing. |
Applications | Semiconductors, optics, wear-resistant coatings, and more. |
Discover how sputtering can enhance your thin film processes—contact our experts today!