Induction heaters, including magnetic induction heaters, can achieve a wide range of temperatures depending on their design, application, and the materials being heated. The temperature range typically spans from as low as 100°C (212°F) for processes like surface hardening or low-temperature annealing, to as high as 3000°C (5432°F) for specialized industrial applications such as melting refractory metals. For most industrial induction furnaces, temperatures commonly reach between 1800°C and 2000°C, making them suitable for melting metals like steel, iron, and other high-melting-point materials. The exact temperature depends on factors such as the power of the induction heater, the type of material being heated, and the frequency of the electromagnetic field.
Key Points Explained:
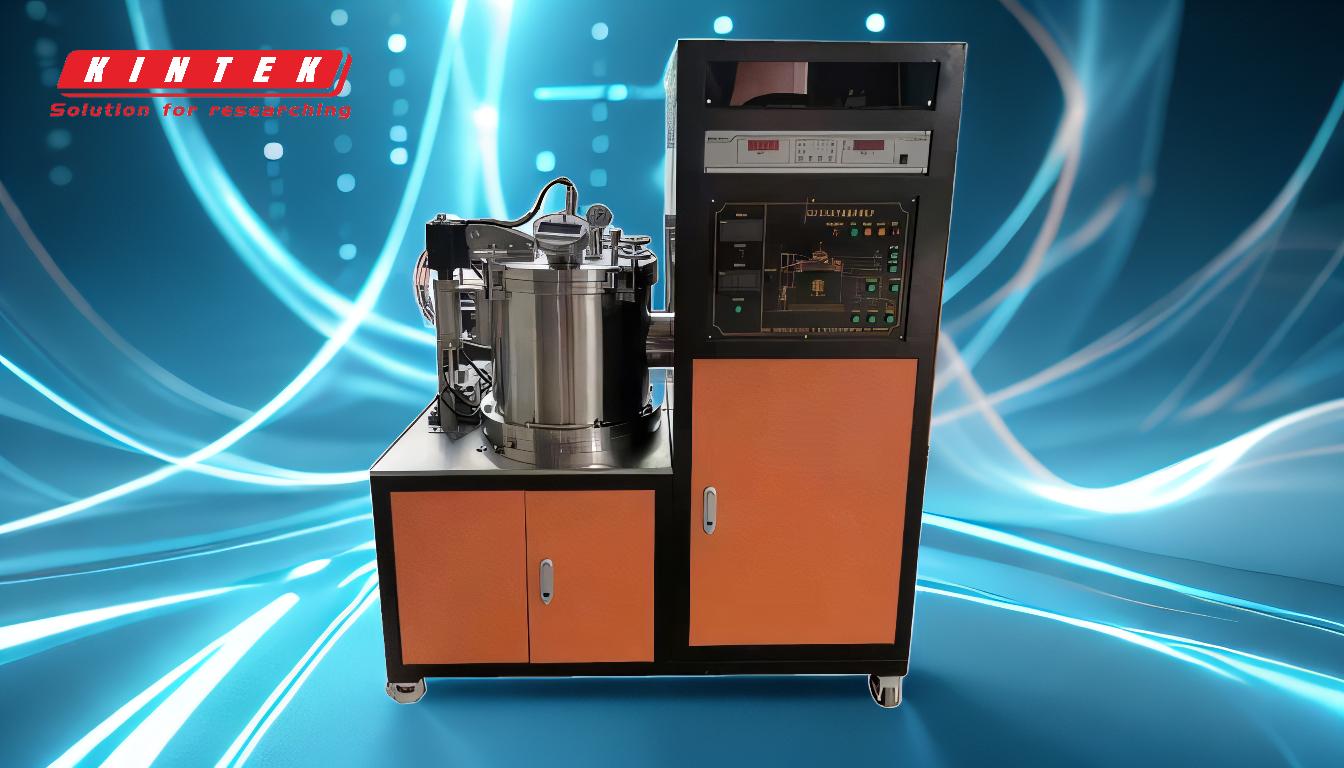
-
Temperature Range of Induction Heaters:
- Induction heaters can operate across a broad temperature spectrum, from 100°C (212°F) to 3000°C (5432°F). This versatility makes them suitable for a wide variety of applications, including low-temperature processes like annealing and high-temperature processes like metal melting.
-
Industrial Induction Furnaces:
- Industrial induction furnaces, such as medium-frequency induction furnaces, are designed to reach extremely high temperatures. These systems typically achieve temperatures of 1800°C to 2000°C, which are necessary for melting metals like steel, iron, and other high-melting-point alloys.
- The ability to reach such high temperatures is due to the efficient inductive coupling between the coil and the charge materials, as well as the high power output of these systems.
-
Factors Influencing Temperature:
- Power Output: Higher power induction heaters can generate more heat, enabling them to reach higher temperatures.
- Material Properties: The type of material being heated plays a significant role in determining the achievable temperature. Materials with higher melting points require more energy to reach their melting or processing temperatures.
- Frequency of the Electromagnetic Field: The frequency of the induction heater affects how deeply the heat penetrates the material and how efficiently the material absorbs energy. Higher frequencies are often used for surface heating, while lower frequencies are better suited for deep heating.
-
Applications Across Temperature Ranges:
- Low-Temperature Applications (100°C to 500°C): These include processes like surface hardening, annealing, and bonding, where precise temperature control is critical.
- Medium-Temperature Applications (500°C to 1500°C): Used for processes such as forging, brazing, and heat treatment of metals.
- High-Temperature Applications (1500°C to 3000°C): Primarily used for melting metals and alloys, including steel, iron, and refractory metals like tungsten and molybdenum.
-
Efficiency and Reliability:
- Induction heating technology is highly efficient, as it directly heats the material without the need for a flame or external heat source. This results in faster heating times, reduced energy consumption, and precise temperature control.
- The reliability of induction heating systems makes them suitable for a wide range of applications, from industrial manufacturing to medical treatments and domestic uses.
-
Specialized High-Temperature Induction Heaters:
- For applications requiring extremely high temperatures, such as melting refractory metals, specialized induction heaters are used. These systems are capable of reaching temperatures close to 3000°C, making them indispensable in advanced manufacturing and materials science.
In summary, the temperature a magnetic induction heater can achieve depends on its design, the material being heated, and the specific application. Industrial systems commonly reach temperatures of 1800°C to 2000°C, while specialized systems can go as high as 3000°C for advanced applications. The versatility, efficiency, and precision of induction heating make it a valuable technology across a wide range of industries.
Summary Table:
Temperature Range | Applications | Key Factors |
---|---|---|
100°C - 500°C | Surface hardening, annealing, bonding | Power output, material properties, frequency |
500°C - 1500°C | Forging, brazing, heat treatment | Power output, material properties, frequency |
1500°C - 3000°C | Melting metals, refractory metals | Power output, material properties, frequency |
Need the right induction heater for your application? Contact our experts today to find the perfect solution!