The annealing process is a heat treatment technique used to alter the physical and sometimes chemical properties of metals, primarily to reduce hardness, increase ductility, and eliminate internal stresses. It involves heating the metal to a specific temperature (above its recrystallization temperature), holding it at that temperature for a set duration, and then allowing it to cool slowly. This process enables the metal's crystalline structure to reorganize, repairing defects and resulting in a more ductile and workable material. The three key stages of annealing are recovery, recrystallization, and grain growth, each contributing to the metal's improved properties.
Key Points Explained:
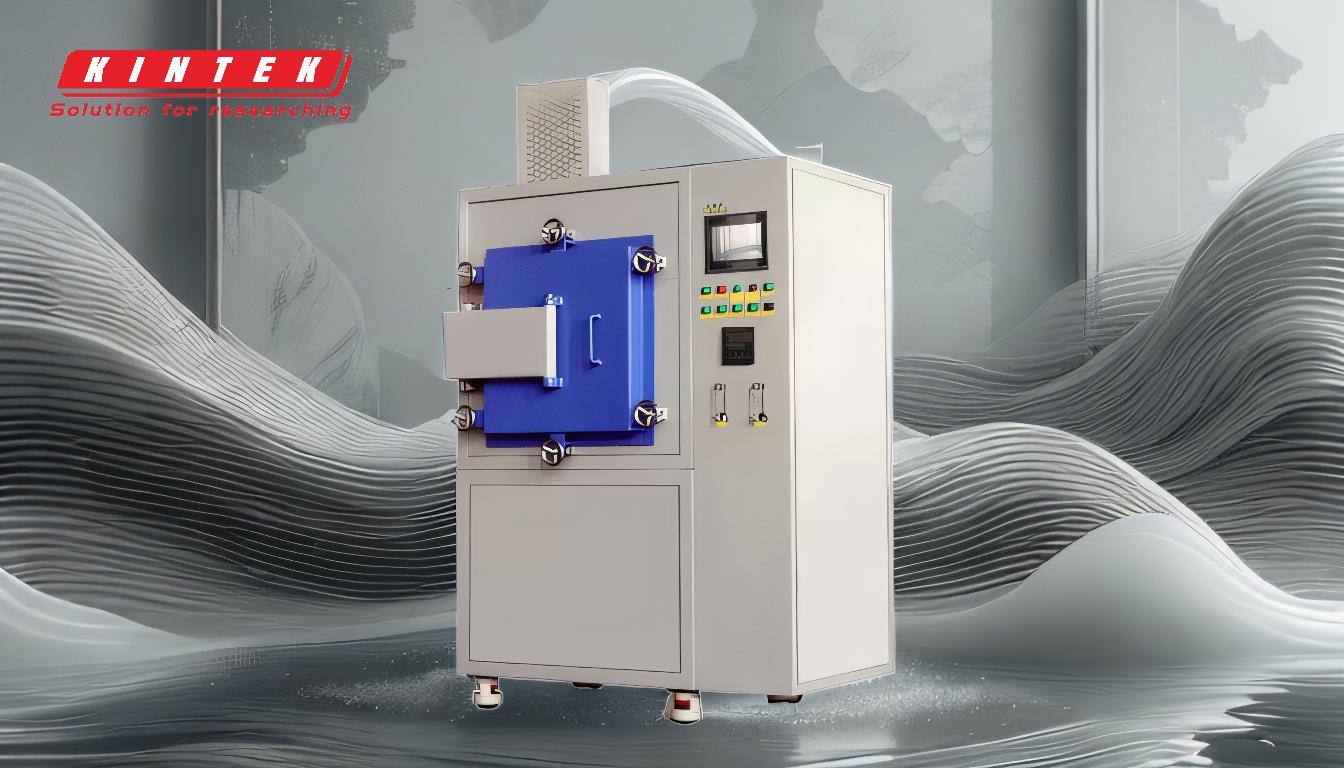
-
Purpose of Annealing:
- Annealing is primarily used to:
- Reduce hardness and increase ductility, making the metal easier to shape and less prone to cracking.
- Eliminate internal stresses caused by prior manufacturing processes like cold working or welding.
- Improve the metal's workability and electrical conductivity by refining its crystalline structure.
- Annealing is primarily used to:
-
Stages of the Annealing Process:
- The annealing process occurs in three distinct stages:
-
Recovery:
- In this initial stage, the metal is heated to a temperature below its recrystallization point.
- Internal stresses are relieved as dislocations in the crystal structure begin to move and realign.
- No significant changes in the microstructure occur, but the metal becomes less brittle.
-
Recrystallization:
- The metal is heated above its recrystallization temperature, causing new, strain-free grains to form.
- This stage eliminates most of the defects in the crystalline structure, resulting in a softer and more ductile material.
-
Grain Growth:
- If the metal is held at the recrystallization temperature for too long, the newly formed grains begin to grow larger.
- While this can reduce hardness further, excessive grain growth may negatively impact the metal's mechanical properties.
-
Recovery:
- The annealing process occurs in three distinct stages:
-
Heating and Cooling Process:
-
Heating:
- The metal is heated to a temperature above its recrystallization point but below its melting point.
- The exact temperature depends on the type of metal and its specific alloy composition.
-
Holding:
- The metal is maintained at this temperature for a specific duration to ensure uniform heating and complete recrystallization.
-
Cooling:
- The metal is cooled slowly, often in a furnace or by burying it in an insulating material like sand or ash.
- Slow cooling prevents the reintroduction of internal stresses and allows the crystalline structure to stabilize.
-
Heating:
-
Benefits of Annealing:
- Improved Ductility: The metal becomes easier to shape and form without cracking.
- Reduced Hardness: This makes the material more suitable for machining and other fabrication processes.
- Stress Relief: Internal stresses from prior processing are eliminated, reducing the risk of failure during use.
- Enhanced Electrical Conductivity: For metals like copper and aluminum, annealing improves their ability to conduct electricity.
-
Applications of Annealing:
- Annealing is widely used in industries such as:
- Metalworking: To prepare metals for further processing like rolling, forging, or drawing.
- Electronics: To improve the conductivity of wires and other components.
- Automotive: To enhance the durability and workability of engine parts and structural components.
- Annealing is widely used in industries such as:
-
Factors Influencing Annealing:
- Material Type: Different metals and alloys require specific annealing temperatures and cooling rates.
- Initial Condition: The hardness and stress levels of the metal before annealing affect the process parameters.
- Cooling Rate: Slow cooling is essential to achieve the desired properties, as rapid cooling can reintroduce stresses.
By carefully controlling the heating, holding, and cooling stages, the annealing process transforms metals into more usable and durable forms, making it a critical step in many manufacturing and fabrication processes.
Summary Table:
Aspect | Details |
---|---|
Purpose | Reduce hardness, increase ductility, eliminate internal stresses. |
Stages | Recovery, Recrystallization, Grain Growth. |
Heating Process | Heat above recrystallization temperature, hold, then cool slowly. |
Benefits | Improved ductility, reduced hardness, stress relief, enhanced conductivity. |
Applications | Metalworking, electronics, automotive industries. |
Key Factors | Material type, initial condition, cooling rate. |
Optimize your metal properties with annealing—contact our experts today for tailored solutions!