Synthetic graphite is manufactured through a series of complex processes that transform carbon-rich materials into high-purity graphite. The production typically involves the following steps: raw material selection, carbonization, graphitization, and purification. The process begins with carbon-rich precursors such as petroleum coke or coal tar pitch, which are heated to high temperatures to remove volatile components and form a carbon structure. This carbon structure is then further heated to extremely high temperatures (up to 3000°C) to align the carbon atoms into the crystalline structure of graphite. Finally, the material undergoes purification to remove impurities, resulting in high-quality synthetic graphite. This material is widely used in industries such as batteries, electronics, and metallurgy due to its excellent conductivity, thermal stability, and chemical resistance.
Key Points Explained:
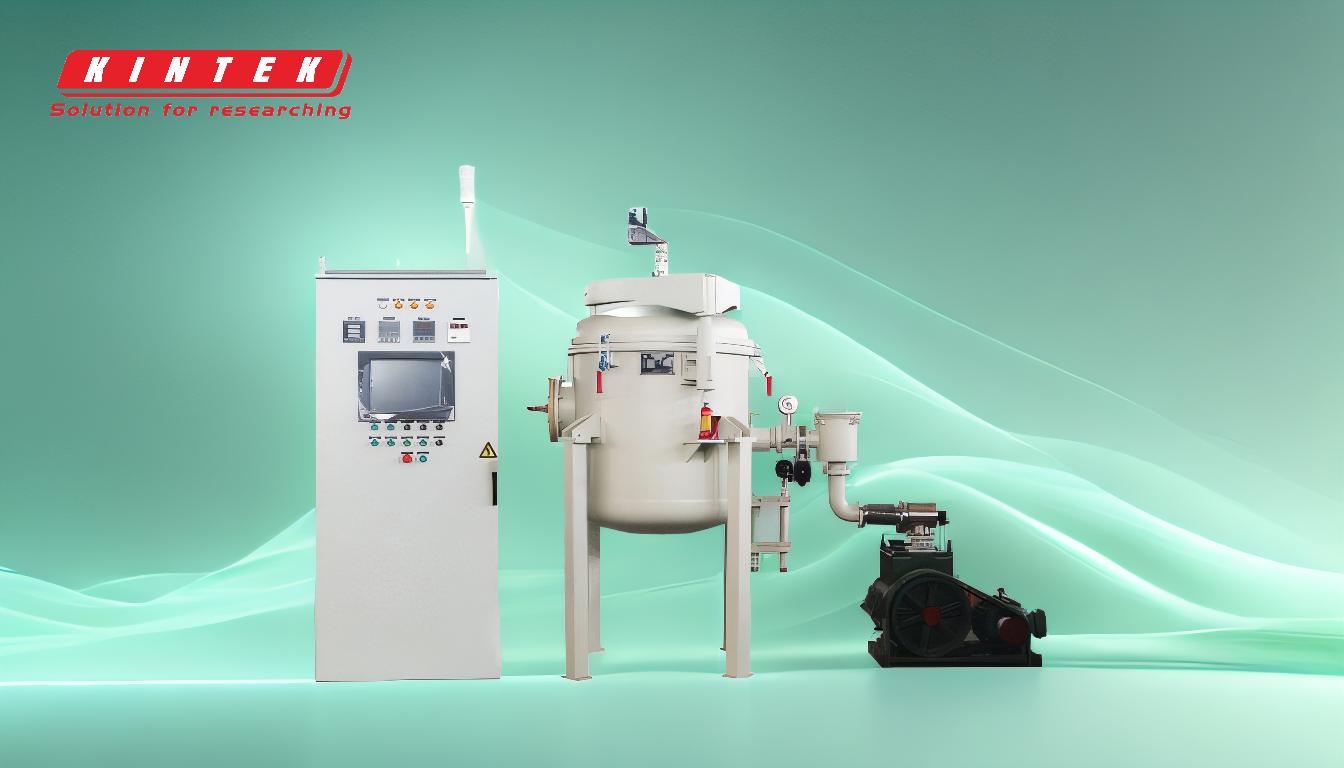
-
Raw Material Selection:
- The manufacturing process begins with selecting carbon-rich precursors, typically petroleum coke or coal tar pitch. These materials are chosen for their high carbon content and ability to form a stable carbon structure during heating.
- Petroleum coke is a byproduct of oil refining, while coal tar pitch is derived from coal processing. Both materials are cost-effective and provide the necessary carbon backbone for synthetic graphite production.
-
Carbonization:
- The selected raw materials are subjected to carbonization, a process where they are heated to temperatures between 500°C and 1500°C in an oxygen-free environment. This step removes volatile components such as hydrogen, oxygen, and nitrogen, leaving behind a solid carbon structure.
- The carbonization process is critical for forming the initial carbon framework, which will later be transformed into graphite.
-
Graphitization:
- After carbonization, the material undergoes graphitization, where it is heated to extremely high temperatures (up to 3000°C) in an inert atmosphere. This step aligns the carbon atoms into a crystalline graphite structure.
- Graphitization is essential for achieving the desired properties of synthetic graphite, such as high electrical conductivity, thermal stability, and mechanical strength.
-
Purification:
- The final step in the manufacturing process is purification, where the graphite is treated to remove any remaining impurities. This is typically done using chemical or thermal methods, such as acid washing or high-temperature treatment in a chlorine gas environment.
- Purification ensures that the synthetic graphite meets the high purity standards required for applications in industries like electronics and batteries.
-
Applications of Synthetic Graphite:
- Synthetic graphite is widely used in various industries due to its unique properties. In the battery industry, it is a key component of lithium-ion batteries, serving as the anode material.
- It is also used in the production of electrodes for electric arc furnaces in the steel industry, as well as in high-temperature applications such as crucibles and thermal management systems.
-
Advantages of Synthetic Graphite:
- Synthetic graphite offers several advantages over natural graphite, including higher purity, better consistency, and the ability to tailor its properties for specific applications.
- Its excellent electrical conductivity, thermal stability, and chemical resistance make it a versatile material for a wide range of industrial applications.
By understanding the detailed steps involved in the manufacturing of synthetic graphite, purchasers can make informed decisions about the material's suitability for their specific needs. The process ensures that the final product meets the high standards required for demanding applications, making synthetic graphite a valuable material in modern industry.
Summary Table:
Step | Description | Key Details |
---|---|---|
Raw Material Selection | Choosing carbon-rich precursors like petroleum coke or coal tar pitch. | High carbon content, cost-effective, and stable carbon structure formation. |
Carbonization | Heating to 500°C–1500°C in an oxygen-free environment to remove volatile components. | Forms solid carbon structure; critical for initial carbon framework. |
Graphitization | Heating to up to 3000°C to align carbon atoms into a crystalline graphite structure. | Enhances electrical conductivity, thermal stability, and mechanical strength. |
Purification | Removing impurities via chemical or thermal methods like acid washing. | Ensures high purity for applications in electronics and batteries. |
Discover how synthetic graphite can meet your industrial needs—contact our experts today!