Annealing steel is a critical heat treatment process that involves heating the steel to a specific temperature, holding it at that temperature for a certain period, and then cooling it slowly. The duration of annealing depends on several factors, including the type of steel, its thickness, and the desired properties. Generally, the annealing process can take anywhere from a few hours to several hours, depending on these variables. The goal is to achieve a uniform microstructure, relieve internal stresses, and improve machinability or ductility. Below, we will break down the key factors that influence annealing time and provide a detailed explanation of the process.
Key Points Explained:
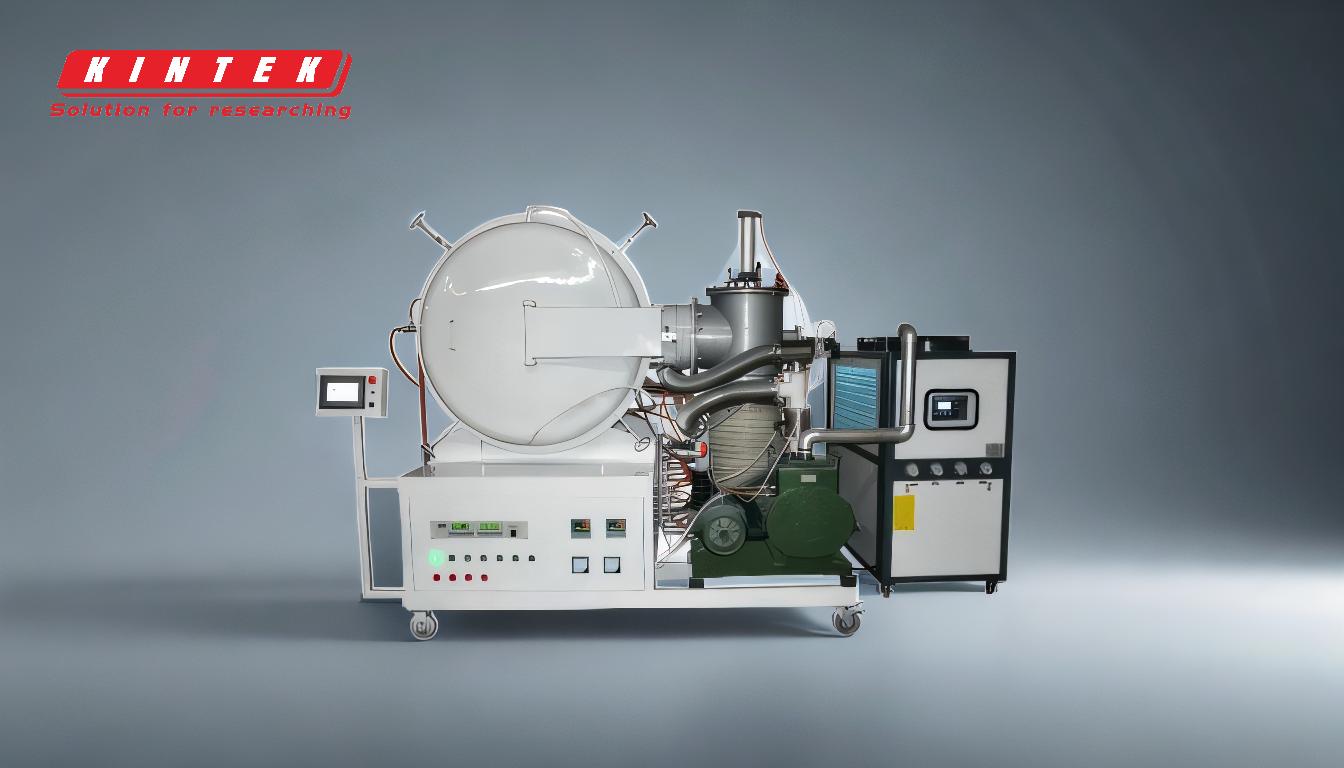
-
Type of Steel:
- Different types of steel require different annealing temperatures and times. For example, low-carbon steels typically need lower temperatures and shorter annealing times compared to high-carbon or alloy steels. The specific composition of the steel determines the optimal annealing conditions.
-
Thickness of the Steel:
- The thickness of the steel plays a significant role in determining the annealing time. Thicker sections require longer annealing times to ensure that the heat penetrates uniformly throughout the material. Thin sheets or wires, on the other hand, may require shorter annealing times.
-
Annealing Temperature:
- The temperature at which steel is annealed varies depending on the type of steel. For most steels, the annealing temperature is typically between 700°C and 900°C. The steel must be held at this temperature long enough to allow the microstructure to transform fully.
-
Holding Time:
- The holding time at the annealing temperature is crucial. It ensures that the steel reaches a uniform temperature throughout and that the desired microstructural changes occur. For many steels, the holding time can range from 1 to 4 hours, but this can vary based on the factors mentioned above.
-
Cooling Rate:
- After the holding period, the steel must be cooled slowly to prevent the formation of internal stresses or hardening. The cooling rate is typically controlled by allowing the steel to cool in the furnace or by using a controlled cooling medium. Slow cooling ensures that the steel remains soft and ductile.
-
Purpose of Annealing:
- The intended outcome of the annealing process also influences the duration. For instance, if the goal is to improve machinability, the annealing time might be shorter compared to when the goal is to achieve maximum softness or stress relief.
-
Furnace Type and Capacity:
- The type of furnace used for annealing can affect the process duration. Larger furnaces with better temperature control may allow for more precise annealing, but they might also require longer heating and cooling cycles.
-
Practical Considerations:
- In industrial settings, practical considerations such as production schedules, energy costs, and equipment availability can also influence the annealing time. Optimizing these factors is essential for efficient and cost-effective annealing.
In summary, the annealing time for steel is not a one-size-fits-all parameter. It varies based on the type of steel, its thickness, the annealing temperature, and the desired outcome. Understanding these factors and how they interact is crucial for achieving the desired properties in the annealed steel. Properly executed annealing can significantly enhance the performance and workability of steel, making it a vital process in metallurgy and manufacturing.
Summary Table:
Factor | Influence on Annealing Time |
---|---|
Type of Steel | Low-carbon steels require shorter times; high-carbon/alloy steels need longer. |
Thickness of Steel | Thicker sections require longer annealing times for uniform heat penetration. |
Annealing Temperature | Typically 700°C–900°C; holding time varies (1–4 hours). |
Cooling Rate | Slow cooling prevents internal stresses; controlled cooling is essential. |
Purpose of Annealing | Shorter for machinability; longer for maximum softness or stress relief. |
Furnace Type/Capacity | Larger furnaces may require longer cycles but offer better temperature control. |
Practical Considerations | Production schedules, energy costs, and equipment availability impact annealing time. |
Need help optimizing your steel annealing process? Contact our experts today for tailored solutions!