The cost of making a mold can vary significantly depending on several factors, including the type of mold, the materials used, the complexity of the design, and the production volume. Generally, molds can range from a few hundred dollars for simple, low-volume molds to tens of thousands of dollars for complex, high-precision molds used in mass production. The cost is influenced by the mold material (such as aluminum, steel, or composite), the manufacturing process (like CNC machining, 3D printing, or injection molding), and additional factors like surface finish, tolerances, and post-processing requirements. Understanding these variables is crucial for accurately estimating the cost of a mold.
Key Points Explained:
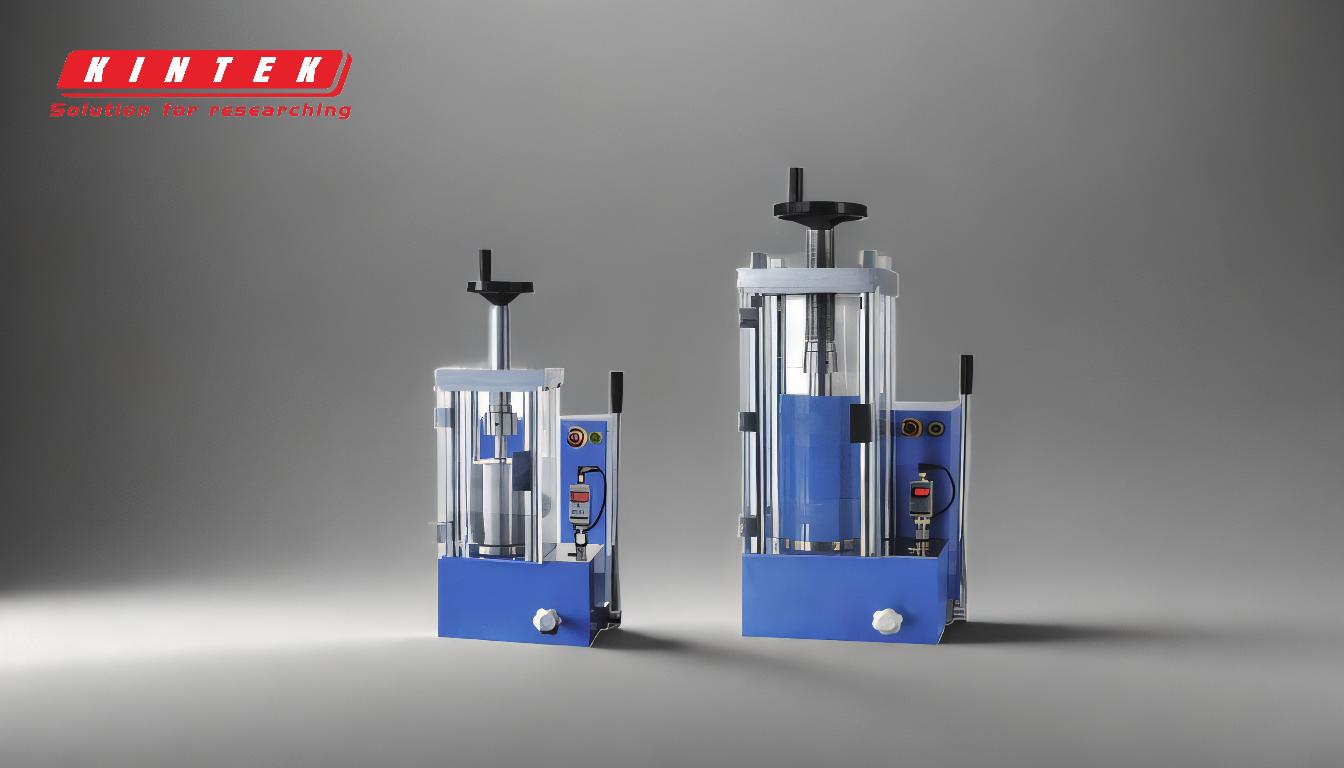
-
Type of Mold:
- Injection Molds: These are typically the most expensive due to their complexity and the precision required. They are used for high-volume production and can cost anywhere from $1,000 to $100,000 or more.
- Blow Molds: Used for creating hollow objects like bottles, these molds are less expensive than injection molds but still require significant investment, often ranging from $5,000 to $50,000.
- Compression Molds: These are used for thermosetting plastics and rubber. They are generally less expensive than injection molds, with costs ranging from $1,000 to $20,000.
- Rotational Molds: Used for large, hollow products, these molds are less precise and therefore less expensive, typically ranging from $500 to $10,000.
-
Material Costs:
- Aluminum: Aluminum molds are less expensive and easier to machine but are less durable. They are suitable for low to medium-volume production and can cost between $1,000 and $10,000.
- Steel: Steel molds are more durable and can withstand higher production volumes but are more expensive. Costs can range from $5,000 to $100,000 or more, depending on the type of steel used (e.g., P20, H13, or stainless steel).
- Composite Materials: These are used for specialized applications and can vary widely in cost, often falling between aluminum and steel molds.
-
Complexity of Design:
- Simple Designs: Molds with straightforward designs and fewer cavities are less expensive. These can cost as little as a few hundred dollars for low-volume production.
- Complex Designs: Molds with intricate designs, multiple cavities, and tight tolerances are more expensive. The cost can increase significantly, sometimes by a factor of 10 or more, depending on the complexity.
-
Manufacturing Process:
- CNC Machining: This is the most common method for creating high-precision molds. The cost depends on the complexity of the design and the material used, but it generally ranges from $1,000 to $50,000.
- 3D Printing: This method is becoming more popular for prototyping and low-volume production. Costs can range from $500 to $10,000, depending on the material and the size of the mold.
- Injection Molding: This process is used for high-volume production and requires expensive, high-precision molds. The cost can range from $10,000 to $100,000 or more.
-
Additional Factors:
- Surface Finish: A higher quality surface finish will increase the cost of the mold. This is particularly important for molds used in the production of consumer goods where appearance is critical.
- Tolerances: Tighter tolerances require more precise machining and therefore increase the cost. This is especially true for molds used in industries like aerospace or medical devices.
- Post-Processing: Additional treatments like heat treatment, polishing, or coating can add to the overall cost. These processes are often necessary to extend the life of the mold or to meet specific industry standards.
-
Production Volume:
- Low-Volume Production: For small production runs, less expensive molds made from aluminum or composite materials are often sufficient. These molds can cost between $500 and $10,000.
- High-Volume Production: For large-scale production, more durable molds made from steel are required. These molds can cost between $10,000 and $100,000 or more, depending on the complexity and the material used.
In summary, the cost of making a mold is influenced by a variety of factors, including the type of mold, the materials used, the complexity of the design, the manufacturing process, and the production volume. Understanding these variables is essential for accurately estimating the cost and ensuring that the mold meets the specific needs of the production process.
Summary Table:
Factor | Description | Cost Range |
---|---|---|
Type of Mold | Injection, Blow, Compression, or Rotational molds | $500 - $100,000+ |
Material | Aluminum, Steel, or Composite materials | $1,000 - $100,000+ |
Design Complexity | Simple vs. complex designs with multiple cavities and tight tolerances | $500 - $100,000+ |
Manufacturing Process | CNC machining, 3D printing, or injection molding | $500 - $100,000+ |
Additional Factors | Surface finish, tolerances, and post-processing requirements | Varies based on complexity |
Production Volume | Low-volume (aluminum/composite) vs. high-volume (steel) molds | $500 - $100,000+ |
Need help estimating your mold costs? Contact our experts today for a customized quote!