Brazing is a process that requires precise control of heat, atmosphere, and material conditions to achieve strong and reliable joints. The heat required for brazing depends on the filler alloy's liquidus temperature, which must be at least 25°C (50°F) above this temperature to ensure proper melting and flow. The process typically involves temperatures ranging from 577°C (1071°F) to 600°C (1112°F), with dwell times varying from 1 to 8 minutes, depending on the specific application and materials. Additionally, the brazing environment must be free of oxidants, with oxygen content below 100 ppm and humidity below -40°C to prevent contamination and ensure optimal joint quality.
Key Points Explained:
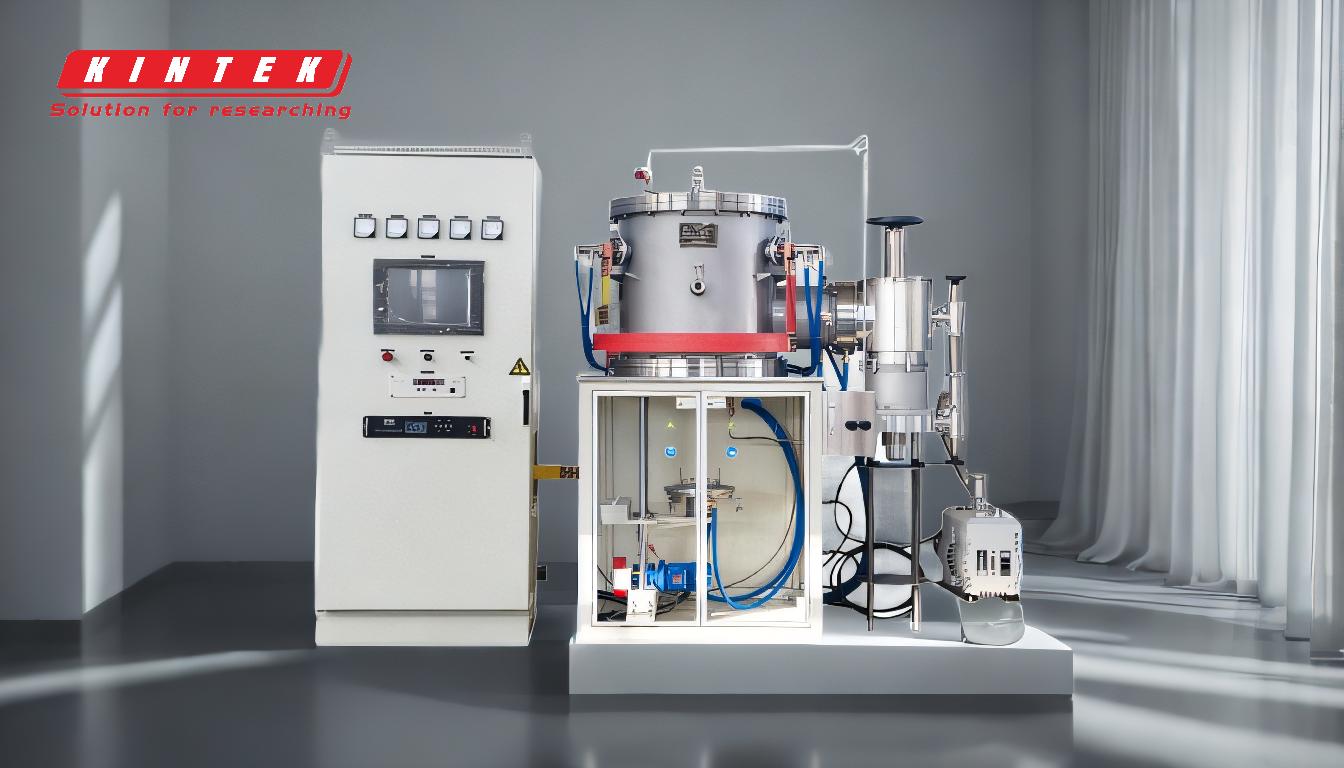
-
Brazing Temperature Requirements:
- The brazing temperature must be at least 25°C (50°F) above the liquidus temperature of the filler alloy. This ensures the alloy melts and flows properly into the joint.
- Typical brazing temperatures range from 577°C (1071°F) to 600°C (1112°F), depending on the alloy and materials being joined.
- The temperature should be the lowest possible within the recommended range to minimize thermal stress on the materials.
-
Dwell Time:
- Dwell time refers to the duration the materials are held at the brazing temperature.
- For temperatures ≥577°C (1071°F), a minimum of 5 minutes is required.
- For temperatures ≥585°C (1085°F), the dwell time should not exceed 1 to 8 minutes.
- Proper dwell time ensures complete melting and distribution of the filler alloy, leading to strong and uniform joints.
-
Atmosphere Control:
- The brazing environment must be free of oxidants, oxygen, and moisture to prevent contamination and ensure strong joints.
- Oxygen content should be below 100 ppm, and humidity should be below -40°C.
- A neutral gas atmosphere, such as pure nitrogen, is often used to maintain these conditions.
-
Joint Preparation:
- The surfaces to be joined must be clean and free of oils, greases, or other contaminants to ensure good wettability and adhesion of the filler alloy.
- The gap between the metals must be precisely controlled. Too narrow gaps can restrict filler flow, while too wide gaps can lead to weak joints with porosity.
-
Filler Alloy Selection:
- The filler alloy must have a melting temperature significantly different from the base metals but with compatible mechanical properties.
- The alloy should spread evenly within the joint cavity to create a strong intermediate layer.
-
Vacuum Brazing:
- In vacuum brazing, a high vacuum and elevated temperature are required to achieve optimal brazing results.
- This method is particularly useful for materials that are sensitive to oxidation or contamination.
By carefully controlling these parameters, you can achieve high-quality brazed joints that are strong, reliable, and free from defects.
Summary Table:
Parameter | Details |
---|---|
Brazing Temperature | 25°C (50°F) above filler alloy's liquidus; 577°C (1071°F) to 600°C (1112°F) |
Dwell Time | 1 to 8 minutes, depending on temperature and materials |
Atmosphere Control | Oxygen <100 ppm, humidity < -40°C; neutral gas (e.g., nitrogen) preferred |
Joint Preparation | Clean surfaces, precise gap control for optimal filler flow |
Filler Alloy | Compatible melting temp, even spreading for strong intermediate layer |
Vacuum Brazing | High vacuum and elevated temp for oxidation-sensitive materials |
Need expert advice on brazing? Contact us today for tailored solutions!