Porcelain is a type of ceramic material that requires precise control of heat during its production. The process involves several stages, including forming, drying, and firing, with the firing stage being the most critical for achieving the desired properties of porcelain. The heat required to make porcelain typically ranges between 1200°C and 1400°C, depending on the specific composition of the porcelain and the desired final characteristics. This high temperature is necessary to vitrify the clay, transforming it into a dense, hard, and translucent material. The firing process must be carefully managed to avoid defects such as warping, cracking, or incomplete vitrification.
Key Points Explained:
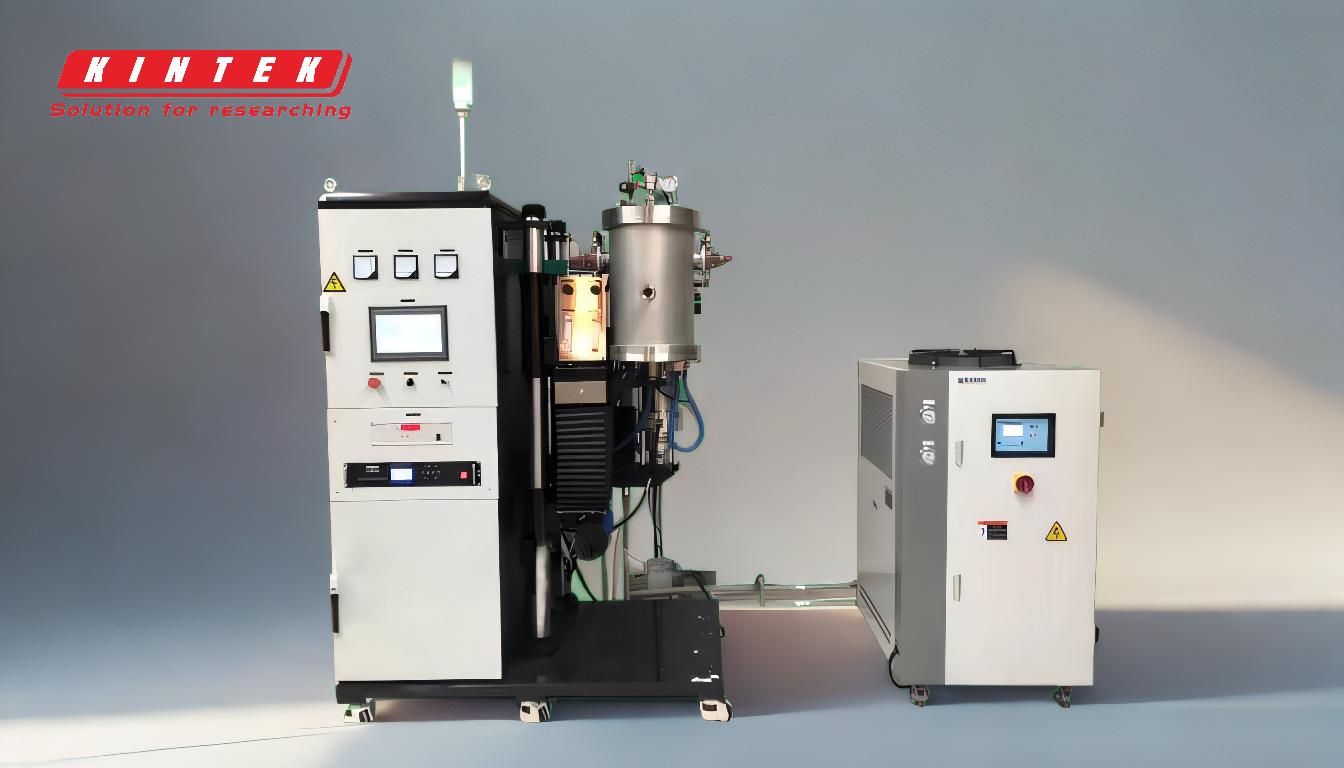
-
Stages of Porcelain Production:
- Forming: The raw materials, including kaolin clay, feldspar, and quartz, are mixed and shaped into the desired form.
- Drying: The shaped pieces are dried to remove moisture, which is essential to prevent cracking during firing.
- Firing: The dried pieces are subjected to high temperatures in a kiln to achieve vitrification, which is the process of turning the clay into a glass-like substance.
-
Temperature Requirements:
- Bisque Firing: This initial firing stage typically occurs at temperatures between 900°C and 1000°C. It hardens the clay and prepares it for the final firing.
- Glost Firing: The final firing stage, where the temperature is raised to between 1200°C and 1400°C. This stage is crucial for achieving the vitrification and translucency characteristic of porcelain.
-
Heat Sources and Kilns:
- Electric Kilns: Commonly used for smaller-scale production, electric kilns provide precise temperature control and are suitable for both bisque and glost firing.
- Gas Kilns: Often used in larger-scale production, gas kilns can reach the high temperatures required for porcelain and are more energy-efficient for large batches.
- Wood-Fired Kilns: Traditional kilns that use wood as a fuel source, which can impart unique characteristics to the porcelain but require more skill to control.
-
Factors Influencing Heat Requirements:
- Composition of the Porcelain: The specific mix of kaolin, feldspar, and quartz can affect the temperature needed for vitrification. For example, a higher feldspar content may lower the required temperature.
- Desired Properties: The intended use of the porcelain (e.g., tableware, decorative items) can influence the firing temperature. Higher temperatures generally result in stronger and more durable porcelain.
- Kiln Atmosphere: The atmosphere inside the kiln (oxidizing or reducing) can also affect the final properties of the porcelain and may require adjustments in temperature.
-
Energy Considerations:
- Energy Consumption: Firing porcelain at high temperatures is energy-intensive, and the choice of kiln type can significantly impact energy efficiency.
- Environmental Impact: The high energy requirements for porcelain production have environmental implications, leading to a growing interest in more sustainable firing methods and materials.
-
Quality Control:
- Temperature Uniformity: Ensuring that the kiln maintains a uniform temperature throughout the firing process is critical to avoid defects.
- Cooling Rate: The rate at which the porcelain cools after firing can affect its strength and durability. Controlled cooling is essential to prevent thermal shock and cracking.
In summary, the heat required to make porcelain is a critical factor that influences the material's final properties. The process involves careful control of temperature during both the bisque and glost firing stages, with the final firing typically occurring between 1200°C and 1400°C. The choice of kiln, composition of the porcelain, and desired properties all play a role in determining the exact heat requirements.
Summary Table:
Aspect | Details |
---|---|
Firing Stages | Bisque Firing: 900°C–1000°C; Glost Firing: 1200°C–1400°C |
Heat Sources | Electric Kilns, Gas Kilns, Wood-Fired Kilns |
Key Factors | Composition, Desired Properties, Kiln Atmosphere |
Energy Considerations | High energy consumption; environmental impact of firing methods |
Quality Control | Temperature uniformity, controlled cooling to prevent defects |
Learn more about optimizing porcelain production—contact our experts today!