Quartz tubes are essential components in various high-temperature applications, particularly in tube furnaces, where they act as reaction chambers. Their ability to withstand pressure is a critical factor in ensuring safe and efficient operations. The pressure tolerance of a quartz tube depends on several factors, including its material quality, wall thickness, diameter, and operating temperature. Generally, quartz tubes can handle moderate pressures, but their primary strength lies in their high-temperature resistance and chemical inertness. Understanding these factors is crucial for selecting the right quartz tube for specific applications.
Key Points Explained:
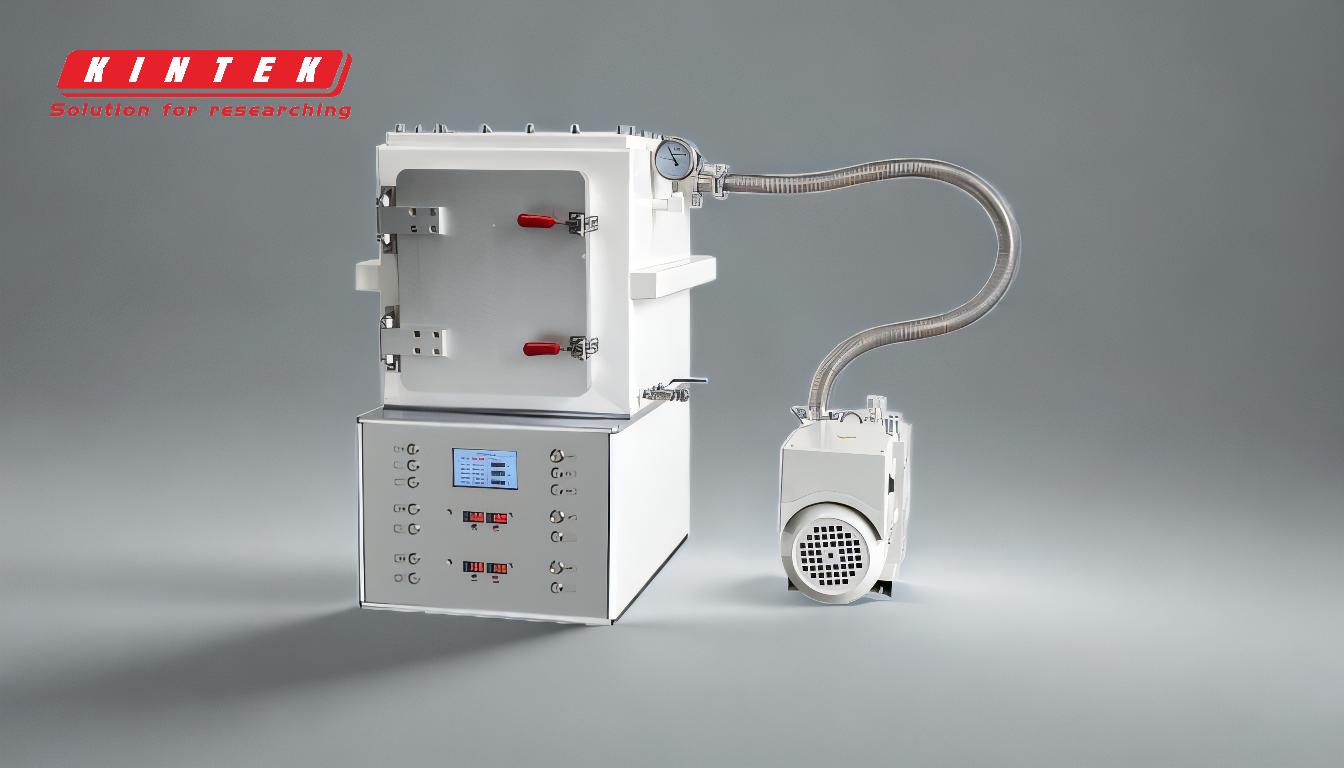
-
Material Properties of Quartz Tubes:
- Quartz tubes are made from fused silica, which provides excellent thermal stability, chemical resistance, and transparency to ultraviolet light.
- The softening point of quartz is around 1,650°C, making it suitable for high-temperature environments.
- However, quartz is brittle and has lower tensile strength compared to metals, which limits its pressure-bearing capacity.
-
Pressure Tolerance:
- The pressure a quartz tube can hold depends on its wall thickness and diameter. Thicker walls and smaller diameters generally increase pressure tolerance.
- Standard quartz tubes are typically designed for low to moderate pressure applications, often in the range of 1 to 10 atmospheres (atm), depending on the design and operating conditions.
- For high-pressure applications, specialized quartz tubes with reinforced designs or additional support structures may be required.
-
Temperature and Pressure Relationship:
- Quartz tubes are more susceptible to failure under pressure at elevated temperatures. As temperature increases, the material's strength decreases, reducing its ability to withstand pressure.
- Proper heating practices, such as gradual temperature changes, are essential to prevent thermal shock and maintain structural integrity.
-
Applications in Quartz Tube Furnaces:
- In a quartz tube furnace, the tube serves as the reaction chamber, where gases and materials interact under controlled conditions.
- The pressure inside the tube must be carefully managed to avoid exceeding the tube's limits, especially during processes like chemical vapor deposition (CVD) or annealing.
-
Safety Considerations:
- Always adhere to the manufacturer's specifications for pressure and temperature limits.
- Inspect quartz tubes regularly for signs of wear, cracks, or thinning, as these can compromise their pressure-bearing capacity.
- Use protective measures, such as safety shields or pressure relief systems, to mitigate risks in case of failure.
-
Customization for Specific Needs:
- For applications requiring higher pressure tolerance, custom quartz tubes with reinforced designs, such as double-walled or coated tubes, can be fabricated.
- Consulting with manufacturers or suppliers can help determine the optimal tube specifications for your specific requirements.
In conclusion, while quartz tubes are not primarily designed for high-pressure applications, they can handle moderate pressures when properly selected and maintained. Their strength lies in their ability to withstand high temperatures and harsh chemical environments, making them indispensable in many industrial and scientific processes. Always consider the interplay between pressure, temperature, and material properties to ensure safe and effective use.
Summary Table:
Factor | Impact on Pressure Tolerance |
---|---|
Wall Thickness | Thicker walls increase pressure tolerance. |
Diameter | Smaller diameters generally enhance pressure-bearing capacity. |
Material Quality | High-quality fused silica improves thermal stability and chemical resistance. |
Operating Temperature | Higher temperatures reduce pressure tolerance; gradual heating is crucial. |
Application Type | Low to moderate pressure (1-10 atm) for standard tubes; reinforced designs for high-pressure use. |
Need a quartz tube tailored to your specific pressure and temperature requirements? Contact our experts today for a customized solution!